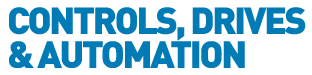
![]() |
Charlotte Stonestreet
Managing Editor |
Keeping the beer flowing
18 July 2018
For many people, there’s nothing like a refreshing cold lager on a hot summer’s day. If the beer dries up, the vendor loses business and the customer goes thirsty. SKF's work at a wheat beer brewery in Germany is helping to prevent this situation
The threat of downtime strikes fear into the hearts of manufacturing managers because it can lead to enormous financial losses. It has been estimated that annual stoppages in food companies can exceed 400 hours on many production lines, leading to huge costs. Depending on the application, a production line shutdown can cost between €5,000 and €50,000; minimising this is a management priority.
Lubrication is critically important to keeping the line moving in food and drink processing plants and crucial when it comes to minimising the risk of unplanned maintenance events. However, manual lubrication is not always possible. This was the case at a family-owned wheat beer brewery in Germany where SKF is helping Erdinger Weißbräu to keep its 1.81 million hectolitres of beer flowing at its redesigned filling plant.
With more than 3000 lubrication points across the site, from brew house to shipping, Erdinger and its machinery supplier realised that an automatic centralised lubrication system would be needed. SKF’s EDL1 (Electric Driven Lubricator) sectional system was therefore specified to increase system availability, reduce the use of lubricant, and minimise wear and tear on the equipment.
The EDL1 system installed at Erdinger comprises 90 sections and three barrel pumps that supply the main lines across the thousands of lubrication points in two halls and a connecting tunnel.
The system’s electrically-driven pressure booster pumps can generate high outlet pressure from low inlet pressure, enabling even the furthest points in the shipping bay to be reached with ease. EDL1’s integrated status monitoring feature also enables the availability of real-time operational data and remote maintenance, increasing the reliability of the zoned system.
Tackling contamination
However, automation is not the only consideration when it comes to lubrication for food-grade facilities like breweries. Although critical to efficiency and productivity, servicing and lubrication can also have a potential downside – contamination.
There are, essentially, two main approaches to tackling the problem of contamination – seal components to reduce the chance of a lubricant leak, or replace grease with a ‘dry’ lubricant.
Sealing the bearing very tightly to create an impassable barrier can prove challenging in the food and beverage processing environment, where high pressure washing with hot water and caustic agents creates a variety of reliability problems; lubricants can be washed out and corrosion can occur creating flaking and possible contamination.
However, SKF Food Line Y-bearing units are maintenance-free bearing units designed for the wet, humid, contaminating environments. They feature composite housings, stainless steel bearing inserts and a special multi-lip seal (called a 2RF seal) that prevented grease displacement and water ingress.
One example of dry lubrication is an option is replacing traditional bearings with ones that use graphite cages. Tiny graphite particles rub off the cage and are deposited as a thin layer onto the surface of the steel balls. Because graphite is a very effective lubricant, this thin, protective layer is enough to prevent the direct metal-to-metal contact that destroys bearings over time.
A similar approach is to retain the use of oil – but one in semi-solid form. A product like Solid Oil is designed to banish the need for re-lubrication. Solid Oil is a polymer matrix that is impregnated with lubricant. It remains ‘trapped’ within the bearing, so will not leak out by operations such as high pressure wash down, for instance.
With sports and good weather driving beverage sales across Europe, keeping the production lines running has never been more important.
Key Points
- With more than 3000 lubrication points across the site, Erdinger needs an automatic centralised lubrication system
- SKF’s EDL1 (Electric Driven Lubricator) sectional system was specified to increase system availability and reduce use of lubricant
- EDL1’s integrated status monitoring feature also enables availability of real-time operational data and remote maintenance
- SKF and EPTDA address the challenges of counterfeit bearings
- Seamless engineering
- Super-precision bearing system
- Friction cut
- SKF seizes counterfeit bearings
- UPGRADED ROLLER BEARING RANGE
- SKF Commences Civil Action Over Counterfeit Bearings
- Spherical roller bearings cut maintenance costs
- Bearing with food safety features
- Bearing rating life model
- No related articles listed