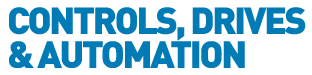
![]() |
Charlotte Stonestreet
Managing Editor |
Editor's Pick
Tool up & team up for digitalisation
14 October 2019
Enhancing asset performance through digitalisation should be achieved through a step-by-step journey, not one giant leap. Gavin Coull summarises the approaches, tools and support needed to capture digitalisation’s value at scale.
Machinery-based companies are leading the charge to digitalise everything from equipment and processes to entire business models. They see a diversity of digital technologies offering opportunities to pursue multiple sources of added value. This complexity is challenging, and it is compounded by the variety of asset types and issues. Even very similar machines can vary in their operating conditions and business criticality, so digital solutions cannot simply be cut and pasted from one site to another.
Improving operations incrementally, from the bottom up, avoids wasting time and resources on ill-fitting solutions. Frontline teams will quickly identify and capture new sources of value if they have the right tools and support. In some ways, digitalisation can work like a ‘supercharged’ version of lean improvement.
Critical roles for senior leaders in digital transformation include setting top-down and bottom-up sightlines and communicating their vision company-wide. They must also put the necessary enablers in place, such as IT infrastructure, training and digital skillsets.
A new set of tools and approaches should be developed for teams to modify and apply across all assets. A traditional lean toolbox uses tools such as root-cause problem-solving to improve operational productivity, quality or flexibility, however a digital toolbox may instead include remote condition monitoring, advanced analytics and collaborative robotics.
Value-focused
At every point in the digitalisation journey, managers must keep the focus of all activities on gaining value. However impressive a new technology might be, it should only be adopted if it truly adds substantial value and improvement.
To assess whether suggested developments are worthwhile, clear targets with performance indicators are necessary. Managers need to understand the rationale behind projects, allocate resources appropriately between different activities, routinely review their impacts and ensure their results guide future planning.
An individual business cannot master all aspects of digital technology or build every digital application from scratch. Collaboration with partners equipped to fill in the necessary expertise makes best sense.
A good example is the provision of equipment and services for condition-based maintenance, a high priority in many digital toolboxes. This is essential for monitoring machine health, predicting future problems and scheduling maintenance interventions to best effect. With a multitude of sensors and data analysis technologies to choose from, deep specialist knowledge is needed to pinpoint the ideal solution for a specific asset and set of circumstances.
SKF’s support in this area improves visibility into the health of customers’ machinery and turns data into insights which drive improved performance. Its digitally enabled solutions are built into the SKF Rotating Equipment Performance (REP) programme, which:
- Assesses - identifying and benchmarking key areas for improvement
- Detects - monitoring to detect impending machine failures and avoid unplanned downtime
- Maintains - selecting the right tools and mechanical maintenance services to optimise day-to-day operational health of all rotating equipment
- Solves - fixing problems through application engineering, lubrication, spare parts management, root-cause analysis and other solutions
- Rebuilds - extending asset life, cutting maintenance costs and improving sustainability with remanufacturing options
By linking machinery across plants and worldwide, Internet of Things (IoT) connectivity solutions take digitalisation even further. Data storage and sharing are enabled by the SKF Cloud, while SKF Enlight Centre dashboards, tailored to workflows, harness the power of Big Data. These facilities provide easy-to-understand data interpretation on which businesses can base sound decisions. Alternatively, customers can connect directly to SKF for expert diagnostics, analysis, insights and advice.
For an even smoother digitalisation journey, with minimal worries about cost and complexity, SKF offers the performance-based Rotation for Life option. An agreed monthly or quarterly all-inclusive fee covers SKF’s supply of application-specific digital technologies which move companies ahead at their chosen pace.
A successful digitalisation journey, delivering value at scale, depends on a managed, stepwise approach, an effective digital toolbox, an understanding of the tools’ use, and collaboration with good partners. With considerable experience as a guide on that road, SKF looks forward to helping more businesses to make digitalisation’s promises a reality.
Gavin Coull is Service Sales Manager at SKF
Key Points
- When the going gets tough
- Condition monitoring to prevent bearing damage
- From bearing management to the big picture
- Food-grade bearing
- White etching cracks: causes & mitigation
- Boost For Electric & Hybrid Mileage
- SKF power transmission products help simplify the supply chain
- Solar Linear Actuator
- SKF & Imperial College London extend relationship
- Super-precision series
- No related articles listed