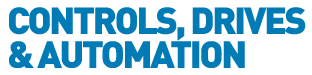
![]() |
Charlotte Stonestreet
Managing Editor |
Home> | DRIVES & MOTORS | >Actuators | >ACTUATOR PROVIDES RESEARCH FOUNDATION |
ACTUATOR PROVIDES RESEARCH FOUNDATION
24 October 2012
SmartDrive is providing expertise behind groundbreaking research into the behaviour and likely performance of large building foundations
Advances in ‘foundation engineering’ have contributed significantly towards infrastructure developments that underpin modern society.
Cambridgeshire-based SmartDrive is providing expertise behind groundbreaking research into the behaviour and likely performance of construction, which is vital to ensure safe economic construction.
Supporting the University of Sheffield, SmartDrive has been working in conjunction with Dr Jonathan Black to develop a pioneering approach to modelling phenomena of vibrated stone column foundations.
The Geotechnical Engineering Group at the University of Sheffield is one of the UK’s leading research groups in the area of physical geotechnical modelling.
Maintaining state-of-the-art test facilities is an important aspect in delivering new advances in knowledge.
Their primary function is to improve bear ing capacity and reduce total/differential settlements of weak soil layers.
"In recent years the vibrated stone column technique has witnessed widening participation by the construction industry as it is considered a flexible, cost effective technique.
"However there is a lack of understanding about their interaction behaviour.
"This research project uses the novel method of transparent soil modelling, an artificial synthetic soil material that has similar properties to naturally occurring soil. Laser-aided imaging is used to track the displacement of the soil during foundation loading which provides increased understanding of the deformation and failure behaviour.” The new test system recently developed is a bespoke four-degree of freedom X,Y,Z_R motion control load actuator, which provides advanced capabilities to simulate complex multi-directional load conditions.
The system, developed by Dr Black in conjunction with SmartDrive, is part of the research project funded by the UK research council Engineering Physical Sciences Research Council (EPSRC).
Specific details of the required system were to provide multidirectional loading of model tests in 4-dimensional co-ordinate axes. Applied loads varied up to 5kN with stroke lengths up to 600mm.
VALUABLE DATA
The SmartDrive Control system provides required feedback from stress and strain gauge loading conditions, which are captured in conjunction with laser and image values, providing valuable data for advanced research techniques into transparent ‘see through’ soil.
In addition to providing all motion controllers, drives, motors and gears and carefully calculated support structure, SmartDrive designed a bespoke graphical PC user-interface to allow a variety of users easy access to the machines capability. By uploading preprepared co-ordinate files, users can create complex motion sequences in minutes. On-Screen controls allow the user to easily adjust parameters such as speeds, accelerations and rotation, meaning operators can quickly gather the required data without specialist knowledge of the complex mecha tron ics behind the experiment.
Dr Black recognised the importance of SmartDrive’s contribution to the project success: "The development of the X,Y,Z_R system was central to the success of this project,” he said.
Located in the Cambridgeshire technology belt, SmartDrive has grown to be one of the UK’s leading design specialists within the field of motion control.
SmartDrive managing director, Dennis Murphy, comments: "We have a strong heritage in designing motion control products at component level, so over the past twenty-four years, we have built a very knowledgeable R&D team.
Whilst we sell a wide range of our own motion products as well as some leading brands, it is our systems integration and systems ability that has really become our speciality.
"Our business has extended from standalone components such as stepper motors, servo drives, encoders, HMI’s, control panels and motion controllers, through to multi-axis systems incorporating linear slides, vision systems and plc control.
Key Points
- A bespoke four-degree of freedom X,Y,Z_R motion control load actuator simulates complex multi-directional load conditions on foundations
- The SmartDrive Control system provides feedback from stress and strain gauge loading conditions
- No related articles listed