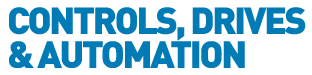
![]() |
Charlotte Stonestreet
Managing Editor |
Home> | INDUSTRY FOCUSES | >Rail | >CHALLENGES WITHOUT BORDERS |
ARTICLE
CHALLENGES WITHOUT BORDERS
23 October 2012
The rail industry is a major user of control technologies, but recent advances are leading to a reassessment of their capabilities. As we look forward to a new era of rail transport culminating in the controversial HS project, Andy Pye looks at a number of developments happening at this very moment
Passenger and freight trains are expected to operate reliably in some of the most challenging conditions imaginable.
Extreme temperatures, aggressive contamination, and shock and vibration can bring vehicles to a standstill, requiring dependable engineering technology. However, with rail operators also looking to make their fleets as energy efficient and cost effective as possible, these systems and components also need to be compact, lightweight and simple to install and maintain.
State of the art control systems can produce a wealth of information by creatively analysing the huge amount of data produced by various assets; for example by comparing maintenance records with technical specification, bespoke predictive maintenance programmes can be developed. If the full potential of current control innovations is realised, the rail industry is on the brink of a sea change that will lead to more efficiency, better reliability and reduced costs.
Technology needs to be based on adopting open standards, working in a flexible and high level programming environment and interfacing to communication protocols such as IEC 61850 and DNP3.
INFRASTRUCTURE UPGRADED
Despite these developments, legacy systems will need to be supported over many years.When its legacy control infrastructure started to suffer from obsolescence, patchy support and unacceptable reliability figures, Heathrow Express required a scalable system for managing the information from and control of safety, security and other monitoring sub systems.
A number of facets, including CCTV, PA, ventilation, safety scenarios, lighting and information boards all had to feed back into the central control room. An open, off-the-shelf system was seen as most appropriate.
Firstco recommended the complete replacement of the bespoke/closed incumbent SCADA solution and a SCADA approach based on RSView 32 from Rockwell Software was selected.
The existing PLC network utilised Allen-Bradley SLC PLCs for monitoring the utilities. Firstco was able to change the interfaces to other systems to a Rockwell Automation interface, which allowed the infrastructure to "talk” to all subsystems.
The complete T5 station and tunnel SCADA solution, based on Allen-Bradley ControlLogix PACs, comprises six sub systems: Fire monitoring; Tunnel ventilation (to SIL2); Public address system; Train information displays; CCTV;Utilities, including all equipment, faults, doors and access control.
By putting all of the control systems in a single EtherNet/IP and ControlNet architecture there is a high level of integration between the sub-systems. This means that they ‘listen’ to the relative statuses of each other and offer the controllers quicker reactions to issues – which is especially important due to the requirement of the station’s ‘sixminute/ no-action’ evacuation protocol. The security systems are also integrated to CCTV and the arrivals schedule is tightly linked to the lift controllers, meaning that elevators are waiting at the right level when trains arrive.
AUTOMATED SERVICING
Russian Railways is comprehensively automating its rolling stock service facilities to achieve a significant increase in productivity, starting with the works in Magnitogorsk, the city near the Kazakhstan border that is known mainly as a centre of the Russian steel industry. Before modernisation of the line, around 4300 rail cars were refurbished at the Magnitogorsk works every year. Following completion of the project and installation of the new technology the capacity of the works will have increased to around 7500 rail cars per year.
Factory automation specialist Technikon opted for the new Mitsubishi iQ Platform system recently launched by Mitsubishi Electric and this controls all the processes on the line, including the milling machines, the welding robots, the conveyor belts, the handling systems and component tracking with wireless RFID tags.
This multi-processor system unites four different controller types – conventional programmable logic controllers (PLCs), motion controllers, computerised numerical controllers (CNCs) and robot controllers – on a single common backplane. The control and communications tasks are shared by one PLC CPU and three

additional high-performance processors. There is seamless integration of CNC machine tools and robots in plant and machinery configurations within a single automation platform. Data and signals are exchanged between the controllers via a common, highspeed backplane bus synchronised with the processing cycles of the processor, which has a cycle time of just 0.88ms.
All the controllers in the system are connected via a Mitsubishi Electric MELSECNET/H network with a redundant architecture.
This network supports high-speed cyclical data transfers and uses fibre-optics cabling for interference-free communications and a "floating master” system that guarantees reliable network operation, even if the field-bus manager fails. The optical network is immune to electromagnetic interference; this is important because of the high-powered electrical welding machines used at the works, the switching operations of which could easily cause interference in nearby control cables. Only a single cable that also carries the power supply is required for communication at rates of up to 25 megabits per second. Connections are simple, further reducing the installation overheads and the wiring costs.
Mitsubishi (Russian rail) – seven high-performance modular controllers, each with one CNC processor and one PLC processor, control the milling machines, welding robots, conveyor belts and handling systems, and also the wireless RFID component identification system
ELECTRICALLY INSULATED BEARINGS
The move away from traditional DC to AC traction motors on locomotives and multiple unit trains, combined with the widespread use of high power AC frequency inverters to control large rotating machines, has resulted in increased demand for electrically insulated bearings.
Train operating companies are looking for lower maintenance costs and more intensive train utilisation for running very high operational distances for new generations of electricity powered trains, with the expectation of a 10 year traction motor life. This is up to twice that of previous generation trains equipped with AC traction motors; hence the longevity of the electric motors is crucial to meeting these ambitious targets.
Traction motor bearings, and other bearings used in high-load electrical applications, have to be electrically insulated in order to prevent current passing through the bearing to earth, which can damage the bearing via erosion and cratering of the bearing raceway and rolling element surfaces.
Specialist UK bearing manufacturer Revolvo has recently supplied electrically insulated bearings for new passenger rolling stock and freight locomotives used in the Channel tunnel rail link; and in Rapid Transit Trams operating in Manchester and Tyne and Wear.
Revolvo uses plasma spraying, using aluminium oxide to insulate the outer surface of either the inner or outer bearing raceway in order to insulate it from the electrical current. This method is preferred to flame spraying and epoxy coating as the plasmasprayed coating is harder and thinner, leading to both greater accuracy and durability.
HYDROSTATIC FAN DRIVES
Diesel exhaust emission standards such as Euro 6 or the US Tier 4 apply to newly manufactured, as well as remanufactured railroad locomotives and locomotive
engines. Tier 4 standards, which are expected to require exhaust gas after-treatment technologies, become effective from around 2014-2015, though current regulations also include more stringent emission standards for remanufactured locomotives.
One consequence of these higher exhaust gas standards is that radiator cooling capacity may need to rise by up to 40%, resulting in size increases of 20%.
Hydrostatic fan drive systems offer a cost-effective and energyefficient method of cooling engines and exhaust systems in rail vehicles. By continuously adjusting cooling effort to match changing requirements, the new systems greatly reduce energy use and they also occupy up to 20% less space in the engine compartment.
Controlled hydrostatic fan drives such as those supplied by Rexroth are superior to conventional units driven with V-belts because variable control of fan speed reduces fuel consumption and reduces exhausts and noise. It is used with the BODAS RC controller, a flexible programmable vehicle PLC used in mobile applications with hydrostatic transmissions through sophisticated closed loop controls.
Intermittent reversing of the fan is used to clean the radiator and restore cooling performance in dusty or dirty environments. The controller can be connected to the CAN bus of the engine thus making additional sensors unnecessary.
PNEUMATICS
Pneumatics has been used throughout the rail industry for many years, used to control everything from braking systems and pantograph mechanisms to doors and toilets. One of the reasons for this widespread use of compressed air systems is their ability to provide a simple and affordable yet also precise and reliable method of motion control both on-board and at the trackside.
Pneumatics form a key element of an automation system developed for one of Europe’s biggest manufacturers of Falns self-discharging freight wagons.
These vehicles are designed for transporting coal. They are loaded mechanically at the upper part of the box and feature four trapdoors, two on each side of the box, for subsequent unloading by free-fall beside the track. For these trapdoors to be controlled easily and reliably, pneumatics technology is used.
There are two large bore actuators mounted under the vehicle, which open and close the hopper doors at the side of the wagon. These are operated by heavy duty manual push buttons via brass body valves that are built into the control panel. As the wagons are used in applications where contamination from coal dust and other particles is rife, these components need to be extremely robust and damage resistant.
Additionally, the pneumatic system is also responsible for locking the doors, so the reliability of the setup has direct implications on safety.
In this instance, the pneumatic control system was developed as part of a complete automation solution, incorporating everything from the pneumatic valves and cylinders to piping and connectors. This consolidation of supply helped the wagon manufacturer keep costs to a minimum, while using a single supplier also helped ensure the final design was fully integrated and simple to install.
Key Points
- Heathrow Express upgrades control infrastructure with an open, off-the-shelf system
- Russian Railway automates rolling stock service facilities using Mitsubishi iQ Platform system
- Move away from traditional DC to AC traction motors increases demand for electrically insulated bearings
- Industrial security to help maintain the safety, availability and operational integrity of critical systems and infrastructure
- Pneumatics form key element of automation system developed for freight wagon manufacturer
MORE FROM THIS COMPANY
- No related articles listed
RELATED ARTICLES
OTHER ARTICLES IN THIS SECTION