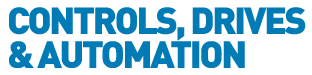
![]() |
Charlotte Stonestreet
Managing Editor |
Home> | INDUSTRY FOCUSES | >Rail | >Keeping Technology On Track |
Keeping Technology On Track
17 January 2013
As the demands placed on railway infrastructure change and develop, so to does the technology that drives continuous improvement throughout the sector
While the collapse of the West Coast Main Line bidding process and controversy surrounding the HS2 rail link may be grabbing all the headlines, behind the scenes the rail network in Britain – which includes underground railways, light rail and tramways, as well as the mainline network – provides a service that is vital to the UK’s economy.
There is little doubt that inefficient services that do not meet needs in terms of routing or frequency are to the detriment of businesses and employment. Added to this is the fact that increasing the amount of journeys made by train and, in turn, reducing the amount of journeys made by road, along with the drive to reduce emissions from trains and even the stations themselves, can make a significant contribution to meeting the UK’s carbon reduction targets. Little wonder then, that there is an ongoing commitment to expand and improve the rail network.
One example of this is the upgrade of the Northern Line on the London Underground, which began last year. The work being carried out on the busiest line on the Tube network to implement a new, high-tech signalling system and control centre will make journeys faster and smoother, increasing capacity by a fifth once the upgrade is complete in 2014. The project follows a similar upgrade to the Jubilee line, which has been successfully completed.
Traditionally, testing for this type of project would have involved the use of a fully operational train and the closing of services, resulting in high costs and disruption to passengers. So the challenge was to generate an alternative testing solution that could alleviate many of the burdens of the traditional method and ultimately lead to a less-costly and more time-efficient means of testing new technologies. The solution also had to be in line with the Underground’s stringent health and safety policy.
Stepping up to the mark, leader in transportation solutions, Thales UK, was commissioned to install the automatic signalling solution for the Jubilee and Northern lines. The project involved installing a Thales S40 SelTrac Transmission-Based Train Control (TBTC) system on both the track and the entire rolling stock fleet of trains. Before these retrofitted trains could use this new system in service, the track installation needed to be tested. The engineering team devised an innovative test rig that could mimic a passenger train fitted with a Thales TBTC system. It needed to be portable and quickly assembled in almost any location along the Underground. Another goal was to reduce the number of test staff and test time so that standard engineering hours could be followed instead of requiring costly weekend closures.
From an environmental perspective, the system needed to run reliably in any environment that could be experienced on the Underground network. This can vary from snow and rain to deep, dark, and dusty tunnels. Additionally, the solution needed to be bidirectional to offer a massive advantage during testing/ fault finding, thus increasing efficiency and optimising track time. Finally, the software needed to be intuitive to reduce the impact during the transition to the new design.
A normal test train is only permitted to travel forward, but the VTT can reverse and retest missed track, rather than loop around the line
Virtual test trains
The solution was to create several virtual test trains (VTTs) using CompactRIO hardware and LabVIEW system design software from National Instruments. The VTT operates as a portable, battery-powered railway trolley that carries testing staff and the Thales communications equipment used to test the SelTrac TBTC system.
The VTT runs with the CompactRIO control system interfaced to custom hardware. Thales used a CompactRIO real-time controller, an FPGA-equipped chassis, and flexible modular signal interfaces to implement the system, all of which were programmed with LabVIEW system design software. This platform provided the onboard SelTrac TBTC signalling equipment with the appropriate signals to mimic an actual passenger train, hence the term ‘virtual test train’.
The company also programmed data-logging functions in the LabVIEW application to easily record technical data on an SD memory card, in case the data was required for the testing and commissioning of the SelTrac TBTC system. To review the test data, a VTT viewer program was also developed using LabVIEW. This VTT viewer program means that the testers on-site can review data immediately to make necessary corrections and ensure the appropriate signals are monitored.
Since work has moved on from the Jubilee line upgrade to the Northern Line, use of the VTT has dramatically increased and diversified. In addition to serving as a testing tool, the VTT is a useful fault-finding tool. Another major advantage is the VTT’s bidirectional ability: A normal test train is only permitted to travel forward, but the VTT can reverse and retest missed track, rather than loop around the line, which inevitably takes time. Another bonus is that the VTT can perform testing whilst other work is being performed in parallel. This is not possible using traditional methods because a train requires that power be available trackside.
Besides providing the control element, CompactRIO can automate data capture. The user can test, gather data, and analyse it all in a short amount of time, which speeds up testing and commissioning.
According to Thales’ Anthony Afonso the use of Labview was a key factor in the success of this project. "The software offered several benefits, such as graphical programming, easy-to-read code, maintainability, and scalability, that all proved essential for a large project. It also featured built-in tools that reduced development time by providing proven sections of code,” he says. "Finally, the user interface design, which is usually every programmer’s nightmare, was simple because LabVIEW offered tools for quick customisation.”
Electrification
It’s not just the UK that is constantly upgrading its rail networks – one of the most pressing issues in the sector worldwide is the electrification of railways. Compared with diesel traction – the most commonly used alternative – electrification offers advantages in terms of enhanced fuel efficiency and reduced maintenance requirements.
Addressing the continued electrification of railways, TE Connectivity (TE), a leading technology partner for railway companies, has created the VESA vacuum circuit breaker (VCB), which is an all electro-magnetically operated system for 25kV and 15kV vehicles. Part of the specific VESA system solution for high-voltage technology in the train, the product is TE’s answer to the increasing trend of operating electric passenger trains and is positioned, says the company, to lead the way into the next generation of the electric rail market.
With a transition from pneumatic to electro-magnetic actuation, train manufacturers are provided with a lower overall cost solution due to reduced maintenance needs and minimised train energy consumption, further enhancing the economic benefit for the operator. TE is leading the VCB technology shift and is currently one of the few suppliers with a substantial quantity of electro-magnetically operated VCBs in the field. A proven technology, the first unit was installed over five years ago and there are now more than 800 units in service on four continents.
The VESA VCB not only eliminates the disadvantages of conventional mechanical pneumatic circuit breakers. It is lighter and easier to mount, safer to use as it utilises an external drive approach, and more economical to operate. The VESA VC is also more reliable as it needs less servicing than conventional systems.
Cross border travel
On the continent it is not uncommon for trains to travel across national borders and although for the passengers this might be a seamless operation, the traction unit pulling the train has to make a transition as it crosses from one country to another. The power drawn from the overhead line – in most cases supplied by a national rail service – will be discontinuous at the border: it may – or may not – be of similar voltage and frequency each side of the transition. As a result the traction set must be ‘multi-standard’ and able to operate from any power supply it will encounter across the network. There also needs to be accurate monitoring of the power drawn by the traction motors at all times, as each authority supplying power on the network needs to be paid for the energy that an international train uses while it is within its national boundaries. To produce accurate billing information power has to be measured and logged at frequent intervals throughout the journey, using GPS to pinpoint where the train was at each measurement point. As modern traction systems employ regenerative braking, returning power to the network, for full fiscal accuracy the energy measurement system has to be bidirectional.
To harmonise operation of international services a European standard has been drawn up that specifies exactly how the energy measurement function (EMF) is to be carried out – prEN50463. Where EN50463 sets new challenges is in the accuracy it demands, specified in terms of ‘class R’ (rail) figures. The overall requirement is for measurement of energy to an accuracy of +/-1.5% for AC and +/-2% for DC. There are three main elements in the measurement and recording of energy; transducers to measure instantaneous current and voltage, and a meter that takes those readings, computes and stores the energy values. For AC readings, it must take account of the phase angle difference between voltage and current waveforms to derive both real and reactive power figures.
To enable traction system designers to meet the requirements of EN50463, LEM has assembled a matched offering of transducers with enhanced accuracy, together with the new EM4T II energy meter.
High-accuracy current, voltage transducers
Due to the challenges of the application, in many cases an indirect current measurement is preferred. Several technologies exist to make indirect measurements based on the magnetic field generated by the current in the conductor feeding the tractions set. In their physical form, they appear superficially similar, a toroidal sensor with the primary conductor passing through the centre of the ring. Measurement of the magnetic flux induced in the toroid by the primary current relates directly to the value of that current.
One form of this sensor uses the Hall effect to translate magnetic flux to a measurement value. However, Hall Effect sensors have difficulty in maintaining linearity over a large dynamic range, such as that specified in EN50463; and may also exhibit limited accuracy at high and low extremes of their measurement range, due to saturation and residual magnetisation effects in the magnetic material.
LEM has chosen to address the problem with a Fluxgate sensor, that will carry certification to Class 0.5R (+/-0.5% accuracy). The Fluxgate sensor uses a nulling principle; it generates a magnetic flux in the toroidal core to exactly balance that induced by the primary current, and from the drive level needed to do so, infers the value of the current. In operation, the sensor drives the magnetic core with a high-frequency AC signal that constantly reverses the magnetisation of the core, driving it around the characteristic known as its B-H curve. The additional magnetic field that arises due to the primary current modulates this behaviour; using this approach the sensor can detect the null condition with extreme sensitivity.
At all values of measured current the magnetic material is driven to saturation in both directions, removing any direct dependency between measurement linearity and the magnetic core’s characteristics. The result is a sensor that can offer very high accuracy and linearity over a wide dynamic range.
Voltage measurement is provided by a transducer from LEM’s DV series, available with 1% or 0.75% full-range accuracy (Class 1R or Class 0.75R certified accuracy, as expressed in the rail traction standards). The series meets or exceeds all of the performance and safety demands of rail traction systems, both those in use today and planned for the future. It offers insulated voltage measurements from 1200 to 4200V, in a package significantly smaller than any other product in the market.
Metering to fiscal standards
Completing the offering is a new, enhanced, version of LEM’s EM4T energy meter, EM4T II, also rated and certified to Class 0.5R accuracy. The compact unit is a single-phase energy meter that meets all current and proposed standards for on-board rail-traction energy monitoring and, specifically, complies with all of the requirements of the new EN 50463 draft.
Key Points
- Thales used NI CompactRIO hardware and LabVIEW software to create virtual test trains
- TE has created the VESA vacuum circuit breaker (VCB), an all electro-magnetically operated system for 25 and 15kV vehicles
- Maintenance in the era of 4.0 - it's still all about the people
- Artificial muscles can lift loads 80 times own weight
- Space to innovate
- Bosch Rexroth confirms event partnership for Maintec 2018
- UK launch for MOONS’ Industries
- Collaboration key for car production
- Industrial control & factory automation worth USD 293.2b by 2025
- 5G smart factory recognised as 4IR pioneer
- Ai-Da Robot announced as artist in residence at Glastonbury
- Robert Langer wins Queen Elizabeth Prize for Engineering