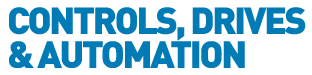
![]() |
Charlotte Stonestreet
Managing Editor |
Home> | IIot & Smart Technology | >Industry 4.0 | >I4.0 digital control systems collaboration |
Home> | CONTROLS | >Systems | >I4.0 digital control systems collaboration |
Editor's Pick
I4.0 digital control systems collaboration
25 February 2019
Ypsomed and Harting collaborate on development of Industry 4.0 digital control systems for retrofitting to plastic injection moulding machines
Ypsomed Group, an international medical technology company specialising in the development and manufacture of injection and infusion systems for the self-injection of liquid medicines, has selected Harting as a collaborative partner in a development project to retrofit legacy protocol plastic injection moulding machines with an integrated Industry 4.0 digital control system that is also linked with a factory-wide MES/ERP system. This approach offers simple and minimal physical integration with an existing production line for a reasonably low level of investment, with long-term benefits including improved productivity, cost savings and extended machine lifetimes.
Introduction
An important element of Industry 4.0 is the ability to apply digitisation to the production environment by adding more intelligence into existing processes. Initially manufacturers have been wary of Industry 4.0, on the assumption that effective implementation would require major (and expensive) changes to production lines. However, through a digital retrofit approach, it is possible to “smarten” up existing processes for minimal cost over a short period of time, resulting in a fast return on investment and immediate productivity gains.
Digital retrofit provides four different ways to improve production processes, increase cost savings and extend the lifetime of different types of machinery:
- Legacy machine protocol conversion
- Condition monitoring (including energy measurement)
- Asset management
- Predictive maintenance.
Legacy machine protocol conversion
Central machine monitoring and process optimisation offer the best way to ensure that production lines and their associated constituent parts operate more effectively and economically. Many machines in well-established production lines, which may be between 15 and 30 years old, can still perform their main functional tasks successfully. However, they do so much less efficiently than their modern-day counterparts. For example, they do not have the same level of computing power, enough memory capacity to record and store relevant data, or the ability to communicate with their modern equivalents. In many cases, these machines also use data formats and communications protocols from the 1980s and 1990s, which are no longer used by today’s PLCs and industrial PCs.
A prime example of a production environment that accommodates mixed protocol legacy machines is a plastics injection moulding machine (PIMM) line. Such machines, when well maintained, can attain as much as a 30-year operational life. However, some of the older software protocol operating languages (e.g. EUROMAP 15) cannot be directly connected to a modern factory MES (Manufacturing Execution System) without expensive annual custom software licensing charges. In many factories these machines still require individual programming by an operator, which can be very time-consuming in larger installations - potentially requiring input from multiple personnel.
An innovative solution to these challenges is offered by Harting’s MICA (Modular Industrial Computing Architecture): an edge computing device in the form of a digitally retrofittable IP67 package with Linux-based open-source software. This modular software and hardware architectural design platform permits the user to choose the programming language and development environment they are most familiar with. MICA is rugged, compact and maintenance-free, and so is suitable for use in the harshest industrial environments.
For the plastic moulding manufacturing environment, Harting has developed the MICA EUROMAP 15 and MICA EUROMAP 63 Gateway variants, which convert the legacy EUROMAP 15/63 TCP/IP machine operating communications protocol into OPC UA, for example, via an intermediate JSON software format. This approach also offers the potential to provide IIoT web enablement and access to Cloud services for Big Data analysis or virtualisation, via an optional downloadable MQTT container. All operational software is housed in separate sandbox containers, ensuring that the MICA EUROMAP 15/63 Gateway provides a secure, fully configurable interface to the plant MES/ERP, eliminating expensive custom MES access software licencing charges that may have previously applied.
As an established Harting customer, Ypsomed saw the immediate potential benefits of applying this Industry 4.0 Digital retrofit approach in its manufacturing operation at its headquarters in Burgdorf, Switzerland. Ypsomed produces several hundred million products a year and meets the highest medical technology quality standards. Due to the high proportion of individual plastic components in its products, the company possesses a large number of plastic injection moulding machines in its production plants.
In order to improve existing levels of plant productivity, Ypsomed has chosen to implement Industry 4.0 process improvements through digitisation at an early stage. To achieve this strategy, Ypsomed selected Harting as a collaborative partner for its development project to connect legacy protocol machines to their MES/ERP system through a digital retrofit approach.
In 2017, one of the first tasks was to make data from a legacy injection moulding machine available for analysis. The machine in question only offered the old EUROMAP 15 protocol, and consequently Harting's Edge Computer MICA was installed and programmed within two days as the protocol translator. Selected production data could then be collected and written to a database for offline analysis.
The next goal is to connect several different types of machines to the IT system at Ypsomed’s internal testing and validation centre and present critical operational data remotely at a centralised factory control station. The machines are connected to the MES system via the MICA, which handles the protocol translation between the MES system and the shop floor. Here, the configuration data record belonging to a production order from the ERP system is retrieved from a database and automatically transferred directly to the machine via the MICA, without requiring intervention by a machine operator. Machine process parameters can now be modified more quickly, reducing downtime and enabling manpower to be much more effectively employed. During manufacturing, production and process data are temporarily stored on the MICA and fed back to a database or ERP system for ongoing quality improvement or record storage purposes. Machine operators can even monitor and affect the process of the production line from off-site, via a smartphone or suitable tablet device.
The new production plant in Schwerin is planned to start up operations in summer 2019. Automated control of production orders will be implemented by 2020.
Condition monitoring
Additional real-time condition monitoring of key operating processes can help to reduce downtime and extend lifetime, thus achieving manufacturing productivity improvements. This can be accomplished by digitally retrofitting additional stand-alone MICA devices to store, analyse and process data from existing or extra retrofitted sensors. As a result, tasks such as monitoring pressure, temperature and flow rates becomes easy, whilst allowing remote centralised process control adjustment via the MES network. Communication with the machine fitted sensors is achieved via a simple Ethernet switch and interlinked active I/O blocks.
Asset management
For asset management, A MICA RFID variant converts the MICA device into a specific RFID Reader, which, when used in conjunction with passive UHF read/write transponders that are fitted to key replaceable mould tools, allows maintenance records to be written and stored onto that particular tool. This can ensure the optimum refurbishment scheduling of high-value mould tools.
Predictive maintenance
Critical operating parts of a plastic injection moulding machine which are subject to continuous wear and tear include the plasticising screw pump and associated check valves. As wear increases, this can result in a significant number of rejected parts and expensive financial losses. This situation can be resolved by monitoring the changes in the operating power curve characteristics of the screw pump and the pressure loading at the check valves.
Integration of a MICA Energy variant provides RS485 Modbus TCP/IP compatible I/O interfaces for linking to the appropriate functional I/O blocks on a machine that access this specific operating data. By pre-setting critical safe operational limits, the MICA Energy can set up alarm conditions for when these limits are breached, allowing machine operators to carry out corrective maintenance as part of the important predictive maintenance process.
For further information visit https://www.harting.com/UK/en-gb
Key Points
- An important element of I4.0 is the ability to add more intelligence into existing processes
- Through a digital retrofit approach, it is possible to “smarten” up existing processes for minimal cost over a short period of time
- Central machine monitoring and process optimisation offer the best way to ensure production lines operate more effectively
- More power for system devices
- New connector ranges
- Cyber security in edge computing
- Enhanced cabling termination
- Discover AI and IIoT solutions at Industrial Ethernet Week
- Industrial computing platform improves productivity
- Integration with high mating cycle connectors
- IIoT & virtualisation whitepapers
- Drive industrial transformation at Industrial Ethernet Week
- HARTING to discuss future technologies at Industrial Ethernet Week
- Reduce Fault Times
- Vision Control Makes The Cut
- MULTIPLE PROTOCOL CONVERSION
- MAKE SURE YOU CATCH THE RIGHT BUS
- Smarter, Faster & More Compact Robot Controller
- What Does Windows 8 Mean For Test & Measurement?
- Thyristor Stack Controllers
- Easy To Automate
- Understanding Thyristor Control
- Introduction to embedded control and monitoring webcast