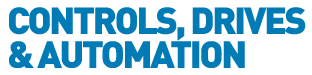
![]() |
Charlotte Stonestreet
Managing Editor |
Electric switch turns on energy savings
22 August 2024
Companies are increasingly making the switch from pneumatic systems to electric automation (EA) – and with good reason, says Aniq Rehman

REDUCING ENERGY consumption is a key financial and environmental imperative for most companies looking to upgrade or replace their pneumatic systems. It is one of the more obvious reasons why electric automation (EA) has gained a higher profile in recent years.
Compressed air systems are generally accepted to cost eight to ten times more than electric systems, while an average 30% of a company’s entire energy costs can be attributed to compressed air generation, according to British Compressed Air Society (BCAS) calculations.
The potential savings offered by EA can be illustrated by comparing one pneumatic cylinder unit with a travel time of 1.29 seconds and a Festo electric cylinder unit with the same travel time.
In this scenario the Festo unit achieves energy savings of 705kWh per year – a saving of roughly £120 per year at current tariffs – and a 93% reduction in carbon emissions. This is for just one cylinder - imagine the saving scaled up to a large industrial plant with multiple units.
However, EA also delivers significantly over air driven processes in a number of other ways.
Speed, agility, precision
EA allows multiple positions and differing speeds to be programmed within a given stroke. Pre-set ‘recipes’ can be stored and selected at the push of a button, while adjustment via a simple touchscreen or keyboard is quick and highly accurate. This minimises the risk of human error and makes the working environment safer by placing operatives at a distance from potentially hazardous machinery. Higher speeds can also be achieved with EA than pneumatic systems (taking the load into account).
The agility and precision offered by EA are particularly beneficial to applications such as conveying and packaging, which demand constant gripping, pushing and pulling.
Hygienic, low maintenance, reliable
Electric systems do not expel microscopic moisture and oil particles into the environment. This makes them ideal for the food and drink or pharmaceutical industries, where every effort must be made to eliminate the risk of contamination.
Electrically driven systems are also more compact and quieter than air cylinders. They do not present the risk of equipment failure and unscheduled downtime, for example due to burn out, and demand significantly lower maintenance. Malfunctions are also quicker to identify and repair.
Is EA the right choice?
To establish whether electric automation is the appropriate choice for your needs, it is helpful to consider whether your processes would benefit from any of the following:
- Multiple positions within a given stroke
- Differing speeds of movement, especially within the same direction
- Controllable acceleration and deceleration in any movement
- High accuracy and repeatability for any of the above
In reality, the only environments not ideally suited to electric systems are ones exposed to high levels of moisture or dirt. ATEX zones can also be a challenge due to the volatile nature of the environment.
Automated packaging is an excellent example of where EA can improve productivity. The nature of automated packaging presents a number of challenges. Frequent changes of direction and differing speeds are required along the line, there is a need for absolute precision during repeat actions and, where the packaging of consumables such as food and drink or pharmaceuticals is involved, scrupulous cleanliness must be maintained.
Pneumatic systems can rarely meet these challenges quickly or easily, as they often demand frequent manual intervention to set and readjust the drive at multiple stages of the packaging process. In contrast EA can provide a fast and responsive solution.
Case study: Fast-paced Electric Automation
One Thorite customer, a packaging company serving the food and drink industry, achieved long term benefits by upgrading to a fully electrically automated system.
Thorite was asked to assist a long-term customer which was struggling to develop a food-grade packaging machine that would run at a faster speed than their current equipment.
They were using a combination of pneumatic cylinders and some electric drives to try and achieve a packaging cycle of one product every five seconds, without success, and procedural change requiring a wrapping motion with multiple rotation processes had added an additional complication.
An initial inspection by Thorite established that the machine, which had undergone programming and timing modifications, was at the limit of its components and needed a ground-up redesign, employing different technologies specifically optimised for this exact application.
Working closely with the customer, Thorite’s Technical Solutions team used exact load and motion data to configure electric drives that were capable of achieving the increased speeds. They also configured an ERMO unit which could achieve continuous rotation in the same direction. CAD models of the drive units were then used to build the final design.
Thorite configured and supplied five linear motion systems, one rotary motion system and one servo unit to drive a conveyor. The final design included a combination of servo and stepper drives, simplified motion and IO-Link connectivity.
The cost-effective design of the new machine, with optimised drives, enabled the customer to achieve the significantly faster packaging cycle of one product every five seconds. The components used also enabled the facility to achieve the closure method that other alternatives were unable to deliver.
The result: improved productivity, reduced manpower and maintenance demands, a reduction in energy use and carbon emissions and ongoing cost savings.
EA might require a higher capital outlay, however it is well worth considering when you factor in the benefits it offers in terms of enhanced equipment functionality and speed, reduced risk of downtime, cheaper maintenance costs and carbon reduction.
- Foundation in Pneumatics training courses to restart
- Two-hand controller
- Pneumatic products
- ELECTRIC DRIVES & VACUUM TECHNOLOGY COMBINATION
- Total fluid & air solutions
- Thorite scoops Festo UK Distributor of the Year award
- C-130 Hercules flies again
- Automated inflation system technology
- Technical expertise & systems engineering teams
- Fluidic muscles
- No related articles listed