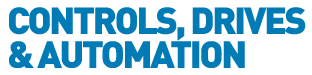
![]() |
Charlotte Stonestreet
Managing Editor |
Home> | AUTOMATION | >Machinery Safety | >OPENSAFETY STANDARD UNDERPINS NESTLÉ PACKAGING AUTOMATION |
Home> | INDUSTRY FOCUSES | >Printing & Packaging | >OPENSAFETY STANDARD UNDERPINS NESTLÉ PACKAGING AUTOMATION |
OPENSAFETY STANDARD UNDERPINS NESTLÉ PACKAGING AUTOMATION
31 October 2012
The dedicated engineering group that takes care of Nestlé’s packaging environment focuses bases strategy on the implementation of standards and open technologies, in this case the OpenSafety standard
Historically, Nestlé’s packaging engineering groups mainly focused on packaging materials and packaging design, but never got involved in the automation engineering of packaging machinery directly.
Nevertheless the Nestlé central engineering group saw many potential benefits in terms of efficiency improvements and improved effectiveness of their packaging facilities, by taking a more active role in the packaging plants. A dedicated engineering group has been established, in order to take care of Nestlé’s packaging environment. This group quickly identified some key elements that need to be addressed.
Instead of specifying only one supplier, Nestlé has identified Rockwell, B&R, Siemens and ELAU as its preferred suppliers for packaging automation control. That means in the future Nestlé will focus less on one specific control provider for packaging equipment, but will base the strategy on the implementation of standards and open technologies. Nestlé was and will still be very dogmatic about whom they will use for automation technology in the process plants.
Also the way this equipment is used is clearly specified.
Nestlé is committing to use the OMAC Packaging-Machine- Language guidelines ‘PackML’. At the present time, the company is doing a pilot implementation together with the preferred suppliers. "Using the PackML PackTags and the OMAC PackML State Model (Fig 1) in conjunction with a standard communication protocol, the Nestlé central packaging automation engineering team will provide a clear specification for packaging machine equipment. This specification will also provide a common setup for horizontal machine-to-machine communication”, says Bryan Griffen, global head of Automation and Process Control, Nestlé Corporate Engineering.
The goal is to exchange all necessary information for easy packaging line integration, based on one global standard. The information includes, for example, start-stop, halts, error handling and support automatic integration of machines from different suppliers and OEMs using different automation control equipment.
Using the OMAC PackML State Model guarantees a common engineering approach, independent of the machine builder and/or control provider. The first implementation step is based on the existing libraries for the OMAC PackML implementation of the preferred suppliers. This already shows a lot of benefits and is the base for the proof of concept.
In the second phase, Nestlé will work on a more detailed specification document and, together with the technology providers, this specification will be reviewed, tested on real equipment and translated into standard, ready to use libraries.
IMPLEMENTING THE OPENSAFETY STANDARD
Working with different technology providers also raises the question of a common safety technology standard. Each technology provider normally pushes its own safety protocol, based on the proprietary communication network. In order to guarantee that all applications can exchange the safety-related information based on one safety network, Nestlé is supporting the OpenSafety standard. OpenSafety provides one single communication standard for safety application across the board of all technology suppliers.
All these efforts will allow Nestlé to write one detailed specification on how to provide a packaging machine that can be easily integrated into a complete packaging line and the whole Nestlé environment, without being too dependent on the used control hardware.
OPENSAFETY EXPLAINED
OpenSafety (often written openSAFETY) is a communications protocol used to transmit information that is crucial for the safe operation of machinery in manufacturing lines, process plants, or similar industrial environments. Such information may be an alert signal triggered when someone or something has breached a light curtain on a factory floor. While traditional safety solutions rely on dedicated communication lines connecting machinery and control systems via special relays, OpenSafety does not need any extra cables reserved for safety-related information. It is a bus-based protocol that allows for passing on safety data over existing Industrial Ethernet connections between end devices and higher-level automation systems – connections principally established and used for regular monitoring and control purposes.
In contrast to bus-based safety solutions created to complement a specific Industrial Ethernet protocol, OpenSafety is designed for general interoperability. Though conceived by the Ethernet Powerlink Standardization Group (EPSG) and originally developed as a safety companion to that organisation’s own Industrial Ethernet variant, the safety protocol is no longer bound to Powerlink.
Instead, it can be used with various major Industrial Ethernet implementations, namely Profinet, Sercos III, EtherNet/IP, Modbus-TCP, and Powerlink itself.
Key Points
• Instead of specifying only one supplier, Nestlé has identified Rockwell, B&R, Siemens and ELAU as its preferred suppliers for packaging automation control
• Using the OMAC PackML State Model guarantees a common engineering approach, independent of the machine builder and/or control provider
- Gearbox without gear
- Edging ahead
- Control systems to combat climate change
- Robots get touchy with smart skin
- Automation firm secures funding for major JLR contract
- UK robot pioneers win Queen’s Award for Enterprise for Innovation
- Electric & autonomous lighting the way
- How robots can make manufacturing plants more efficient
- Minimising machine safety risk
- Hyundai & Kia debut VR design evaluation system