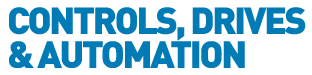
![]() |
Charlotte Stonestreet
Managing Editor |
Home> | MACHINE BUILDING & ENGINEERING | >3D Printing & Prototyping | >Orthotropy & additive manufacturing |
Orthotropy & additive manufacturing
01 July 2020
Orthotropy, or not to be? That is the question. The pertinent question for users of additive manufacturing, at least, as this article from Additive Flow explores
So you’ve printed a part and it’s failed. How could this be? You've meticulously gone through all the steps you should. Drawn up your CAD model, loaded up the design domain, ran it through your favorite topology optimisation tool, fixed it (with Magics / Netfabb or a-another) – and printed it with the perfect settings recommended by the print manufacturer.
So what happened? Well, most topology optimisation software packages out there are missing an important feature; most do not actually take into account how additive processes behave – which means that optimisations are taking place based on an assumption. And this assumption is invariably incorrect. The (intuitively sensible) assumption is that your 3D printed part will behave the same from all directions. This is called isotropy – but, unfortunately, it is not the case.
So why even bother topologically optimising with incorrect assumptions, and with tools that you know won't do the job? Unless you like to invite a whole bunch of testing, and insert a critical dose of ‘tacit knowledge’ into your organisation – it sounds like a lot of hassle, and a lot of risk.
Additive Flow took a different, wider approach to topology optimisation and has built from the ground up a suite of tools that optimise subject to the nuances of additive manufacturing processes.
What is orthotropy?
Orthotropy is a feature of 3D printed parts that behave differently based on the direction they are measured. Most topology optimisation tools assume 3D printed parts behave the same in all directions (isotropy), which means these results are neither accurate nor optimised.
Additive Flow’s topology optimisation capability is natively built to be ‘Additive Aware’ and optimises shape and material subject to the varying material properties, including orthotropy. If this is not taken into account, parts can fail and opportunities will be missed.
Additive manufacturing is the meeting point of material science, design engineering, production management, and much more. It is so multi-disciplinary that the human mind — no matter how intelligent or skilled up — can boggle. This is where a new breed of tools is needed, to help our boggling minds to make the most of this exciting, complex, technology.
Additive manufacturing tends to produce parts that are anisotropic along the build axis. This means that 3D printed parts are orthotropic, often weaker, to forces applied perpendicular to the build direction.
If these orthotropic properties are ignored, and engineers use the prevailing isotropic solvers on the market, results will be wrong, because they cannot take into account the actual material properties.
This means isotropic topology optimisation is severely limited because it is based on the false assumption that materials behave in the same way. The engineer has to choose from two bad options:
1. To optimise subject to the weakest direction – hence missing optimisation opportunities of additive — missing weight/cost/time saving gains
2. To optimise from an average of the material properties, which can result in key safety factors being missed — it would be certain that the weakness along the build direction was not accounted for — so how could the parts be used without further unnecessary design-test cycles?
For the majority of additive manufacturing processes that are orthotropic, how can engineers be confident about their results, and hence deploying AM in their businesses?
Composites: Orthotropy plays an even greater role with composites, where fibre alignment delivers enhanced engineering properties in specific directions. Additive manufacturing with both chopped and continuous fibres can result in seriously powerful mechanical properties. For example with an FFF process, Carbon filled ABS performed 2x to 4x better along the strongest plane in key mechanical tests vs. pure ABS.
How would the engineer properly design for these compelling material properties along certain axes? Especially when accounting for the fact that the weakness along the build direction for CFF is 50% weaker.
The orthotropic solvers within Additive Flow’s software stack are able to optimise topologies for single and multi materials – accommodating both the weakness of build directions and the superpower of composites. For example, the power of our solvers in application was demonstrated in our work with Royal HaskoningDHV – where they saved a further 20% in weight versus alternative isotropic solvers.
Key Points
- Most topology optimisation software packages do not actually take into account how additive processes behave
- Additive Flow has built a suite of tools that optimise subject to the nuances of additive manufacturing processes
- If orthotropic properties are ignored, and engineers use the prevailing isotropic solvers on the market, results will be wrong
- Industrial control & factory automation worth USD 293.2b by 2025
- Fighting labour shortages with cobot deployment
- Pump up the savings
- AMP Institute receives funding boost
- Retail robotics innovation wins award
- £37.6m UK Digital Twin Centre announced for Belfast
- Conformance test cases
- National Engineering & Construction Recruitment Exhibition
- PROGRAM EASES PUMP SELECTION
- Maintenance across borders