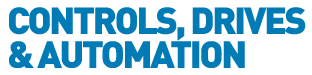
![]() |
Charlotte Stonestreet
Managing Editor |
Home> | AUTOMATION | >Handling & Logistics | >Robots on the move |
Home> | AUTOMATION | >Robots | >Robots on the move |
Editor's Pick
Robots on the move
14 May 2024
Over time, robots are certain to become a more common sight at home, in pedestrian areas, on the roads, and in workplaces like factories, warehouses, and farms. With this in mind, Mark Patrick takes a look at building location-aware robots to operate in unstructured environments

UNLIKE THE restricted areas in which industrial robots are typically installed, outdoor environments, agricultural sites, and some industrial sites like mines, quarries, or factories are quite unstructured. It is often not practicable for robots to move according to prescribed patterns to reach a desired destination, such as following markings on the floor or moving pre-programmed distances. The environment contains many obstacles and is continuously changing in ways that are unpredictable and require the robot to “think on its feet”; that is, to react autonomously and in real-time.
Accurate contextual awareness is both mission-critical and safety-critical. This includes geographical location, both to navigate to the destination and to avoid unsuitable areas. To protect its cargo and complete the journey safely, a delivery robot needs to keep away from the road except in special circumstances, such as when needing to cross it.
Satellite positioning is an effective option to enable mobile robots to operate in unstructured environments. Autonomous ground vehicles used in agriculture utilize satellite positioning to determine their precise positions in large and complex fields. This information is essential for tasks like precision farming, enabling robots to plant seeds or apply fertilisers and pesticides with pinpoint accuracy. In this way, precision farming delivers improved resource utilisation and potentially higher crop yields. In addition, autonomous ground vehicles equipped with satellite navigation can perform tasks such as soil sampling, data collection, remote monitoring of plant health, harvesting, and transporting crops or raw materials.
Optimising GNSS performance
Mobile robots that are designed for carrying cargo such as retail goods for home delivery, components within a factory, or seeds to be sowed on farmland, tend to be relatively large. Although energy is not for wasting, power restrictions are less tight than is the case with many other connected, smart devices. The global navigational satellite system (GNSS) can be designed to deliver the best possible performance, with an antenna optimally sized for strong reception and receiver circuitry designed for optimum sensitivity. In addition, positioning the antenna in a prominent position on a suitable external surface of the vehicle can ensure the best line of sight to the sky under most circumstances. Mouser Electronics has a selection of GNSS antennas, including the XAHP.50 Colosseum X Active Multiband GNSS Antenna from Taoglas (Figure 1), optimised for different applications such as autonomous vehicles suited for external mounting.
Using a single GNSS constellation, the location can be accurate by three to ten metres. Multi-constellation tracking can improve accuracy by providing more satellites from which to calculate positions. Several other services are available to improve accuracy, including differential services and real-time kinematics (RTK) that transmit data to correct factors such as atmospheric interference and satellite clock drift, which can reduce location errors to within one metre. Precise point positioning (PPP), satellite-based augmentation, and ground-based augmentation are primarily used for aircraft navigation and help to enhance the accuracy of positioning systems.
Satellite signals can become obscured for various reasons, depending on the application. Delivery robots operating in towns and cities can be vulnerable to the well documented urban canyon problem or when moving through underpasses or tunnels. Agricultural robots can encounter problems with tree cover, which can be seasonally dependent. Robots that operate in covered areas such as large warehouses, or that move between outside and indoor areas, may experience inconsistent service.
Pseudo-satellites, or pseudolites, can be installed on the ground to mimic satellite signals, thus ensuring availability in areas where direct connection to satellites is known to be difficult. Alternatively, to implement supplemental dead reckoning, a common approach is to use a robot’s on-board inertial sensors to compensate for impaired or absent satellite signals. On the other hand, location awareness can be achieved using radio signals from public or private networks.
RF networks with localisation
With LTE cellular networks, the 3GPP NB-IoT protocols allow several methods for positioning including Location and Positioning Protocol (LPP), observed time difference of arrival (OTDOA), and cell ID (E-CID), as well as Narrowband Positioning Reference Signals (NPRS). Support for these services can be network-operator dependent. LoRa networks can also determine location time-delay calculation based on the timing information collected and transmitted by the network gateways. Modules like the Murata ABZ LoRa® Module (Figure 2), which integrates a microcontroller, wireless transceiver, RF switch, and balancing chip, can help quickly set up LoRa connections and start evaluating the geolocation capabilities.
The long-range transmission capabilities of LoRa and NB-IOT, which deliver advantages in many applications, tend to challenge the accuracy of time-delay positioning calculations. To overcome this, robot operators can consider setting up their own private 5G networks to provide communication and location services. Otherwise, ultra-wideband (UWB) localisation and Bluetooth® indoor positioning are possible. A UWB network can be established by placing base stations, or anchors, only a few metres apart to ensure accurate localisation based on time-delay calculations. The UWB signal strength also helps to reduce multipath errors that can afflict weaker localisation signals such as GNSS.
While Bluetooth® has supported approximate positioning by calculation, the latest Bluetooth® 5.x specifications add direction finding to raise the possible accuracy to within a metre through received signal strength indications (RSSI). These include Angle of Arrival (AoA) and Angle of Departure (AoD). AoA direction finding is performed at the anchor, which contains an antenna array and calculates the position of a transmitting mobile device based on the observed phase differences as the signal is received at the different antennas. AoA is suitable for real-time location and tracking. In AoD, the mobile device observes the phase differences between signals received from the anchor’s antennas. AoD is suitable for navigation and wayfinding. The u-blox XPLR-AOA-1 Explorer Kit works out of the box to help developers experiment with Bluetooth® direction finding.
Robots are going mobile as businesses seek greater productivity and their customers demand improved services. Increasingly, robots will be found moving through industrial sites, urban areas, and agricultural spaces, often transporting raw materials, components, and finished products. In these unstructured environments, self-localisation is mission-critical and safety-critical to avoid collisions with humans and hazards such as motor vehicles or animals.
Although GNSS is an obvious and well proven solution, availability can be less than ideal. Several approaches are viable to compensate, including enhanced satellite services, pseudolites, dead reckoning with inertial sensors, and long-range or private indoor RF networks such as UWB and the latest Bluetooth® direction-finding capabilities.
Mark Patrick is director of technical content for EMEA at Mouser Electronics
- eBook explores next generation tech
- Building better HMIs
- All Things IoT eBook
- Energy-friendly MCUs for smart devices
- Alternative energy resource hub for design engineers
- Connectivity solutions for I4.0 eBook
- New eBook - Industry 4.0 and Beyond
- Mouser expands industrial automation offer and resource hub
- Mouser Electronics named Global High Service Distributor of the Year by ON Semiconductor
- How can AI improve AOI?
- Balls to Gravity
- ROBOTS GIVE FASTER CELL TOOL CHANGE TIMES
- ROBOT FOR DELICATE ASSEMBLY
- FIRST FASTBOX
- NUMBER OF ROBOTS IN UK ON THE RISE
- Tailor Made For Automated Warehouses
- Number of Operators Reduced
- Prevents Potential Material Release
- Integrated or Standalone
- The future is bright - The future is automation!