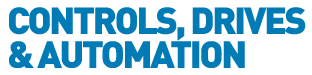
![]() |
Charlotte Stonestreet
Managing Editor |
SECTOR SUPPORTED BY INJECTION OF ENGINEERING
30 October 2012
From the simplest syringe to the most sophisticated MRI scanner, the medical industry requires an enormous range of products and equipment. CDA looks at some of the engineering that lies behind this important sector
Engineers who regularly design drives for medical equipment soon realize that there are many requirements that are common to most, if not all, applications. It goes without saying that medical equipment has to be sterile and easy to keep absolutely free of bacteria; it also needs to be easy to use and should be nonintimidating for possibly nervous patients.
Whether the application is a systolic pump, heart monitor, whole body scanner or even a simple patient winch, we can sum up key design requirements as including: small package, high accuracy, smooth motion, low noise and exceptional reliability.
According to David Baillie managing director of specialist supplier, HT Servo, nearly all machinery includes drive motors and for medical equipment it is often found that stepper motors provide the best motive solution given the above criteria. Induction motors are generally too big and noisy and cannot achieve the required accuracy, while servo motors can be expensive and their need for closed loop control make them too complex for nontechnical environments.
There are a number of ways in which stepper motors measure up to the key medical requirements: Compact size – Stepper motors provide a good power output in comparison to their size. Most steppers come in standard frame sizes, such as the NEMA designation, including miniature sizes. For most medical axes, small motor dimensions are an advantage because it keeps the overall machine size down and also allows room for thorough cleaning/sanitizing.
There are large and powerful steppers available for high-load axes, meaning a single motor technology can satisfy all motion requirements even on the most complicated machinery. Also many manufacturers produce nonstandard sized steppers, which may be suitable for space-constrained installations.
Accuracy – Not every axis in a machine needs to be pin-point accurate, but when it comes to say laser eye surgery, microscopically precise motion is an absolute. And lasers are becoming a first choice medical technology for incisions, tumour eradication and many other procedures. Similarly, keyhole surgery has become almost the default technique for most operations.
The big advantage of stepper motors is their inherently digital motion. They step forward one precisely defined measure of rotation at a time – there is an error, but importantly it is a precisely known error so can be accounted for in real time by the control electronics. Typical stepper errors are a fraction of one arcminute (0.0167deg) and can be guaranteed by the manufacturer.
ULTIMATE ACCURACY
For ultra-precise positioning, medical engineers tend to use microstepping motors in preference to servos, thus maintaining a single technology philosophy. It is worth noting that for the ultimate in accuracy steppers can be used with closed loop feedback control systems.
WHEN ACCURACY IS CRITICAL IT IS WORTH INVESTIGATING THE MANUFACTURERS’ PRODUCTION PROCESSES
Design engineers can look up the accuracy of a given make of stepper in the sales catalogue, and will typically find specification of 0.45deg or even 0.22deg. But when accuracy is critical it is worth investigating the manufacturers’ production processes, looking at Six Sigma results, Defects per Million Parts and other measurements.
Smooth Motion - Stepper motors can stop at any location they are programmed to. For instance a typical motor may have a step size of 1.8deg (i.e. 200 steps per rev), and it might be set to rotate 250 steps, settle then turn again by 150 steps. The major motion is very smooth through the steps, but they may take a few microseconds to settle in the new position (the final step), creating a slight oscillation. In some applications these oscillations can add up and cause jittery, unsmooth motion.
An experienced drives design engineer will know that there are ways to create an operation environment for the motor such that smooth motion is possible. It is perhaps counter intuitive, but a motor that is overly powerful is more likely to judder. So it is important to select a motor that has just the right amount of torque.
Experience counts for a lot here, so talking to an applications engineer will help eliminate the guesswork on choosing the right motor. If your chosen motor is indeed too powerful, decreasing the voltage or current will decrease torque. Dampers can be purchased and placed on the end shaft of a step motor in order to create more weight on the motor, thus, dampening the jittery motion.
Low noise – Some patients are nervous and will find noisy equipment upsetting, and because in a busy ward, clinic or hospital several machines may be in use at once, quiet operation is effectively essential.
Low noise and smooth motion go hand in hand. But noise from a motor can be a result of several factors. Mechanical noise can be caused by an imbalance of inductance or resistance readings from phase to phase (stepper motors generally have two phases where electrical characteristics must match). Other times, noise can be caused by poor design and manufacturing of each component in the step motor.
Once again, looking for a manufacturer’s six sigma capabilities is key to getting good quality and long lasting step motors.
Reliability - Medical applications need reliability, it is as simple as that! But searching for the right motor is perhaps not the best approach. Searching for the right motor manufacturer is likely to pay far higher dividends, because a long term, two way relationship can be developed.
Medical equipment designers could (and should) request MTBF specifications (Mean Time Between Failure) to ensure that their potential motor will last a certain number of cycles. But it is worth considering that while stepper motors are very robust under correct usage conditions, what would happen if they were used inappropriately.
Generally, if a stepper motor is used under the correct load conditions (both axial and radial loads of the shaft), and if environmental conditions are within specifications, step motors will last a long time. The life of a step motor usually correlates with the life of the bearings within the motors, which can last as long as 20 years.
Motor abuse can be largely avoided by careful machine design.
Drives systems should be protected from impacts and dampers used if there is a possibility of shock loads.
Speed controls should be preset, so that operators cannot over strain motors with excessive speed. Free air flow will prevent overheating.
In short, good practice design will ensure a long and reliable life for a stepper.
MAGNETIC RESONANCE IMAGING
Hailed as the most important diagnostic imaging discovery in medicine since the discovery of XRay by Roentgen in 1890, the chances are that if you haven't had an MRI scan yourself, you will know someone who has. Used to produce high quality images of the inside of the human body Magnetic Resonance Imaging is based on the principles of nuclear magnetic resonance (NMR), a spectroscopic technique used by scientists to obtain microscopic chemical and physical information about molecules. Unlike CT scans or traditional X-rays, MRI does not involve the use of ionizing radiation and its associated risks.
MRI is particularly well-suited to picturing the soft-tissue structures, within the human body.
It is able to do this because what MRI in fact maps is the distribution of water molecules.
Every different part of each organ will have a characteristic density of water contained within it – it is well-known that a high proportion of the chemical make-up of every human being is water – and by building up a picture of the different water densities, you also assemble an image of the organs that contain the water.
Water is not, conventionally, thought of as a "magnetic” material, and the parameters that are measured in MRI depend on a subtle effect at the atomic and molecular level; a weak signal that is only revealed under powerful, but extremely precise, stimulus.
When first devised, MRI scanners typically employed, within their control systems, current sensors that exploited the Hall Effect (the production of a voltage difference across an electrical conductor, transverse to an electric current in the conductor and a magnetic field perpendicular to the current). In time, this became a limitation on the precision and quality of results.
Now, a new generation of sensors has contributed to greatly improving the detail available in MRI images. LEM makes the high accuracy transducers that go into MRI scanners.
ONE OF THE KEY ELEMENTS IN THE CURRENT CONTROL LOOP IS THE GLOBAL ACCURACY OF THE CURRENT TRANSDUCER
Most of today’s MRIs generate the static field with a magnet using coils of niobium-titanium (NbTi) wires immersed in liquid Helium at a temperature of 4K. Gradient coils superimpose a magnetic gradient to the static field Ho in order to provide spatial information from which the geometry of the image is constructed. Imaging takes place in just one plane or slice at a time. To ensure that signals are received only from nuclei in that plane, only those exact nuclei must be stimulated into resonance.
The appearance of the resonance is strongly dependent on the value of the magnetic field Ho – in other words, the resonant peak is very sharp – and the gradient coils superimpose a magnetic field to ensure that the final magnetic field is exactly equal to Ho, only and exactly in the plane of interest. To set up the gradient, a pair of coils carrying opposing currents is orientated to augment the static field at one end of the region of interest, and oppose it at the other.
Three pairs of gradient coils are located around the cylinder of the MRI apparatus to create three orthogonal magnetic fields. So, it is possible to adjust the magnetic field at any point in the volume of the cylinder. Gradient amplifiers operating in a closed servo-type loop drive the currents in the gradient coils (Figure 7). Each MRI therefore needs three such current control loops, and it is in these control loops that new sensor technology is making a significant contribution.
Image clarity and resolution is directly linked to applied magnetic field, and therefore to the control of the current injected into the gradient coils. One of the key elements in the current control loop is the global accuracy of the current transducer, which needs (among other parameters) to exhibit extremely low non-linearity error, of under 3 ppm of measuring range; very low random noise with low frequency noise from 0.1Hz to 1kHz; very low offset and sensitivity drifts over temperature range of under 0.3 ppm/K; very high stability of offset versus time, to handle scans lasting tens of minutes; measuring range of 1000 A peak; and wide bandwidth, with a –3dB point of 200 kHz.
With superficial similarities to a Hall Effect device, but with significant advantages, the double fluxgate closed loop transducer (ITL 900) achieves all of these requirements, and for many other high-accuracy current measurement functions in addition to MRI gradient amplifiers. In its present form, the technology is limited to a relatively narrow operating temperature range (typically +10°C to +50°C) but further development of the technology is on-going, with the objective of extending high-current measurement precision even further. According to LEM, its ITL 900 transducer could prove to be as significant for the future of MRI scanning as the Hall Effect transducers were for its introduction.
VOLUME MANUFACTURED
Seemingly at the opposite end of the scale to highly sophisticated MRI scanners, volume medical devices such as disposable syringes must still be manufactured to very exacting standards. Optimal Industrial Automation is helping manufacturers in this sector to meet increasing competitive pressures, with state-of-the-art vision inspection systems that optimise production efficiency in highly regulated production environments.
With its ability to look inside the production process, Optimal is able to undertake a process of continuous inspection, using specialist optical vision equipment to inspect product features and identifiers, to verify critical-toproduct attributes in real time.
Optimal has successfully completed multiple medical device inspection projects including needle inspection, injection moulded device inspection, print on device inspection and diagnostic strip critical parameter and dimension inspection.
For example, a needle inspection project was for the high speed examination and checking of critical dimensions, including the detailed measurement of the needle facets. For this a PC based Cognex VisionPro vision system was used, this in turn interfacing to a 21 CFR Part 11 compliant front-end software package. The system provides real time information and process improvement data to the operators to enable the optimisation of the process.
A second example is for the inspection of critical dimensions, features and the correct assembly of a multi component plastic medical device. Multiple inspections were required down the assembly line, and for this project multiple Cognex In-Sight vision systems were used, these, in turn, interfacing to synTI – Optimal’s regulatory compliant operator interface ‘front end’ for vision inspection projects. With its ability to interconnect to a complete range of inspection and printing devices, synTI offers the facility to configure a complete line inspection system to check virtually any parameter including bar codes, 2D codes, OCV, OCR, vignettes, physical dimensions, misshapes or serialised codes.
This inspection system measures critical dimensions, checks for the presence and alignment of critical parts of the moulding, checks for correct printing on the moulding and verifies that the assembly machine has located the components in the device correctly.
The system also provides real time feedback to the machine to enable the rejection of faulty items, thus minimising waste by preventing continued additions to an already scrapped component and providing real time process improvement data to the machine’s operators.
Key Points
• For medical equipment, stepper motors can provide a particularly suitable motive solution
• Magnetic resonance imaging shows greater detail thanks to highperformance current sensors from LEM
• Volume manufacturers of medical devices benefit from state-of-the-art vision inspection systems
- Cleanroom SCARA robots automate medical syringe manufacturing
- UK manufacturing sector stabilises as political uncertainty subsides
- Single- or multi-supplier philosophy?
- Prescription for production
- Polymers in robotic gearing
- UK tech that ‘teleports’ humans into robots in finals of global robotics competition
- Keeping heavy loads moving without cage creep
- Micro managing
- It's all about data
- Making automation affordable in cost-cutting times
- No related articles listed