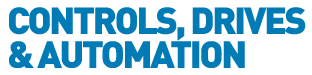
![]() |
Charlotte Stonestreet
Managing Editor |
Home> | DRIVES & MOTORS | >Servo Motors & Drives | >Steppers or Servos? |
Home> | DRIVES & MOTORS | >Stepper Motors & Drives | >Steppers or Servos? |
Editor's Pick
ARTICLE
Steppers or Servos?
05 November 2012
Stepper motors are a relatively simple and inexpensive approach to control motion moves. When is it best to invest in servo systems? Andy Pye looks at the development of servos which challenge steppers
While steppers use simple and inexpensive controllers and run open loop (having no position or velocity feedback), servo motors are used in closed loop control systems, where a digital servo motor controller directs operation by sending velocity command signals to the amplifier, which drives the servo motor. An integral feedback device (resolver) or devices (encoder and tachometer) are either incorporated within the servo motor, or are remotely mounted, often on the load itself.
Speed and torque are often the factors that determine whether servos or steppers are the best approach. When the application demands appreciable torque and/or relatively fast speeds, steppers often don’t work out.
Stepper systems also work well when loads don’t change.
Stepper motors stall when the situation calls for more than their rated torque. With a servosystem, output-torque capacity rises dramatically at higher speeds. The additional torque at these speeds can produce the desired movement much more quickly. Further, servosystems can warn of changing conditions and this information can be used to prevent production stoppages.
The accuracy of a stepper system is limited by the number of full steps per revolution. The repeat - ability will vary with the amount of frictional load. With a servo system, the position-control loop in the servoamplifier will assure the servo gets to the position that has been commanded, regardless of changing load conditions.
Also, it usually takes longer to get a servosystem up and running. Each feedback loop must be tuned to ensure the system remains stable throughout.
However, newer servo technologies address some of these concerns. For example, low-cost servo options have become available for as little as a 10% premium over the cost of an equivalent stepper. Some servo products, like the Junma Servo Series, available through Yaskawa Europe, have been designed specially to replace stepper technology at a comparable price.
This plug-and-play design concept requires no parameter settings or gain adjustments. To simplify things, the Junma servosystem detects load inertia automatically. Adaptive tuning algorithms optimise gains for the control loops with no user interaction. The amplifier comes with a pulse-and-direction input resembling that of stepper motors.
So in many instances, the servo can use the same controller and motion program as the stepper system that it replaces. Connect the power and feedback cables and the motor is ready to run, providing high torque output at speeds up to 4500rpm.
System parameters are set on system power up, machine load inertia is calculated automatically, and tuning gains are adjusted dynamically, even when the load changes, allowing the system to adjust to changing conditions.
Other functions include jogging, homing to marker pulse, electronic gearing, and torque limiting. Junma features four available servo motor and amplifier sets with rated outputs ranging from 100 to 750W, capable of both 100 and 200V input voltages. Servo motor feedback is provided with a 16-bit incremental encoder, providing a resolution of 65,536 pulses per revolution.
Users are not required to do any special tuning for machine vibration, because the Junma detects the vibration and performs automatic tuning. If any unusual noise occurs while the machine is running, the detected vibration may be different from the actual vibration. In this case, the solution is to increase the Reference Filter Setting (FIL) by one, and then return to the previous setting.
Speed and torque are often the factors that determine whether servos or steppers are the best approach. When the application demands appreciable torque and/or relatively fast speeds, steppers often don’t work out.
Stepper systems also work well when loads don’t change.
Stepper motors stall when the situation calls for more than their rated torque. With a servosystem, output-torque capacity rises dramatically at higher speeds. The additional torque at these speeds can produce the desired movement much more quickly. Further, servosystems can warn of changing conditions and this information can be used to prevent production stoppages.
The accuracy of a stepper system is limited by the number of full steps per revolution. The repeat - ability will vary with the amount of frictional load. With a servo system, the position-control loop in the servoamplifier will assure the servo gets to the position that has been commanded, regardless of changing load conditions.
MORE COMPLICATED
However, servosystems are typically more expensive than steppers, being more complicated and because of the additional feedback device and accompanying cable.
Also, it usually takes longer to get a servosystem up and running. Each feedback loop must be tuned to ensure the system remains stable throughout.
However, newer servo technologies address some of these concerns. For example, low-cost servo options have become available for as little as a 10% premium over the cost of an equivalent stepper. Some servo products, like the Junma Servo Series, available through Yaskawa Europe, have been designed specially to replace stepper technology at a comparable price.
This plug-and-play design concept requires no parameter settings or gain adjustments. To simplify things, the Junma servosystem detects load inertia automatically. Adaptive tuning algorithms optimise gains for the control loops with no user interaction. The amplifier comes with a pulse-and-direction input resembling that of stepper motors.
So in many instances, the servo can use the same controller and motion program as the stepper system that it replaces. Connect the power and feedback cables and the motor is ready to run, providing high torque output at speeds up to 4500rpm.
System parameters are set on system power up, machine load inertia is calculated automatically, and tuning gains are adjusted dynamically, even when the load changes, allowing the system to adjust to changing conditions.
Other functions include jogging, homing to marker pulse, electronic gearing, and torque limiting. Junma features four available servo motor and amplifier sets with rated outputs ranging from 100 to 750W, capable of both 100 and 200V input voltages. Servo motor feedback is provided with a 16-bit incremental encoder, providing a resolution of 65,536 pulses per revolution.
Users are not required to do any special tuning for machine vibration, because the Junma detects the vibration and performs automatic tuning. If any unusual noise occurs while the machine is running, the detected vibration may be different from the actual vibration. In this case, the solution is to increase the Reference Filter Setting (FIL) by one, and then return to the previous setting.
Junma will now be able to do automatic tuning again.
Key Points
- In some applications servomotors can be swapped for stepper motors with no change required in motor-drive electronics
- Where higher torque is required, servomotors have an advantage over comparable stepper motors
MORE FROM THIS COMPANY
- No related articles listed
OTHER ARTICLES IN THIS SECTION