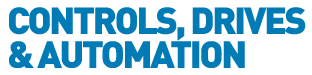
![]() |
Charlotte Stonestreet
Managing Editor |
Home> | IIot & Smart Technology | >Industry 4.0 | >Wireless technology: Key to accelerating I4.0? |
Home> | AUTOMATION | >Sensors | >Wireless technology: Key to accelerating I4.0? |
Wireless technology: Key to accelerating I4.0?
11 December 2018
Today’s smart wireless communication devices are increasingly being used in a wide variety of industrial applications where the potential productivity gains are huge, writes Martin Walder, VP Schneider Electric Industry
Globally, the manufacturing industry is undergoing a major transformation. The industry is using smart technologies to provide reliable power infrastructures, efficient energy use and improved manufacturing productivity. Consequently, particularly for existing facilities, wireless technology is being used to rapidly deploy smart infrastructure and Industry 4.0 solutions.
In recent times, there have been huge strides in the progress of wireless for use with sensors. This includes very low power and long-range wireless with up to a 10-year battery life to battery-less self-generating communications capabilities.
For many businesses, implementing wireless sensors is a no brainer. Wireless sensors offer reduced installation time, both for new machinery and the revamping of existing installations. They can also help to minimise downtime and improve the MTTR (meantime to repair) – for example trying to find the faulty section in a long sensor cable run and then replace it.
Whilst battery technology is improving rapidly, becoming capable of storing more energy with a smaller footprint, it is still a limiting factor in some industrial applications with a high frequency of operations.
This is where mechanical energy harvester technology comes into play. This technology is independent of ambient light or vibration or temperature, as the energy is generated by the actuation of the push-button or the limit switch actuation head. This means it is both long-lasting and consistent with industrial machinery costs.
When the operator pushes the button, or when the limit-switch head is actuated, mechanical energy is transformed into electrical energy. This supplies the transmission of a one-time radio message to one or multiple receivers. In addition, up to 32 push buttons and limit-switches can be synchronised to one receiver, providing even greater mobility in any environment. This battery free solution offers permanent availability, benefits the environment and eliminates costly battery maintenance, re-charging and recycling. Ultimately, more companies ought to be implementing mechanical energy harvester technology for this reason.
Enabling Industry 4.0
We are constantly bombarded with Industry 4.0 updates and predictions. We only need to turn on the TV or open a newspaper to hear about factories and manufacturers implementing new automation technologies, robotics and machine to machine communication. However, the Industry 4.0 discussion is about much more than these automation technologies – and wireless technologies play a huge part in driving Industry 4.0.
By engraining these wireless sensors into the operations taking place on the factory floor, data can be gathered and computed to make automated decisions with a greater degree of confidence and speed. By bringing more unity to Industry 4.0 and wireless sensors, manufacturers are starting to move away from more traditional, manual and time-consuming processes. Instead, manufacturers are able to constantly collect data from operations across the floor, allowing for more predictive maintenance and more productive operations. With increased insights from this data, wireless sensors enable automation wherever possible. Increased automation means less risk of human error, less manual labour, increased efficiencies and productivity, as well as more informed decision making.
The industry is moving away from reactive measures, towards more proactive practices. By implementing modern technology solutions such as wireless sensors, manufacturers gain the ability to ensure that operations are optimised and can act in a more predictive manner to prevent downtime and to boost efficiencies. As wireless and energy harvesting technologies become more popular on the market, they will also become integrated into smaller and smaller form-factors including limit-switches and more low power electronic sensors.
Key Points
- Wireless sensors offer reduced installation time, both for new machinery and existing installations, and help minimise downtime
- Mechanical energy harvester technology provides permanent availability and eliminates battery maintenance, re-charging and recycling
- Data can be gathered and computed to make automated decisions with a greater degree of confidence and speed
- Smart is sustainable too
- Young innovators take part in Primary Engineer programme in partnership with Schneider Electric
- Schneider Electric named World’s Most Sustainable Corporation for second time
- Schneider’s commitment to sustainability recognised
- Joint initiative to drive industrial digital transformation
- Variable Speed Drives: digitising the industry
- Future-ready I/O solution
- Schneider & Cisco partner to bridge OT/IT in building management systems
- Optimising safety in hydrogen processes
- Cutting-edge application control