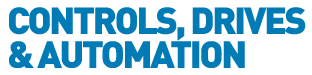
![]() |
Charlotte Stonestreet
Managing Editor |
Marine technology moves into the digital age
15 August 2018
Sensors, controls, connectors - Andy Pye takes a look at the technologies that are seeing the marine sector sail into the digital world
The advent of digital pneumatics promises to change how machines and processes are designed and managed throughout the industrial world. It’s a technological disrupter with exciting potential applications in offshore oil and gas exploration and production.
For example, Festo is using digital pneumatics to control and monitor latch opening on the fingerboard of an oil exploration platform. The benefits include cost and time savings in installation, a reduced safety risk for employees, lower energy cost and increased reliability through preventive maintenance.
The pneumatically based fingerboard-latching system for drill-rig tubulars safely indicates the exact locked or open position of each latch. This system operates reliably in harsh water- or land-based drilling environments and eliminates hard to maintain wire harnesses and electronic sensors on Fingerboards. This next generation pneumatic solution indicates to derrick hands on a colour touchscreen display the exact open or closed position of every fingerboard latch. The reliable, rugged pneumatic system eliminates the need for wire harnesses and electronics on fingerboards.
An application team developed this drilling industry solution utilising the Industry 4.0-based VTEM Motion Terminal. The VTEM Motion Terminal is the world’s first digital pneumatic system. Downloadable apps create an almost unlimited number of functions for the motion terminal. A single motion terminal can replace 50 different hardware components based on its combination of apps.
Temperature monitoring of marine engines
Instrumentation manufacturers are working with engine OEMs to develop solutions to meet the reliability and lifetime challenges for industrial engine sensors, while trying to minimise engine delivery cost. Temperature monitoring at critical engine locations provides important information on running behaviour, safety margins and the need for maintenance on critical components like cylinder liners, exhaust valve seats and bearings.
Marine engines with 4000 hours of operation represents only around nine months of running. However, 4000 hours of running for a car will bring them close to the end of their life cycle. With time between major overhauls for industrial engines varying from 30,000 to 50,000 hours, it is a challenge for fragile sensors to last this long with heavy day-to-day use.
Advanced electronic component reliability is allowing for better configuration and higher performance of marine horsepower engines, according to Patrice Flot, chief technical officer at CMR Group.
The evolution of engine technology makes the importance of reliability and long lifetime for exhaust gas temperature sensors increasingly critical. As reliable sensors are now mandatory for today’s common rail and electronic gas engines, any sensor failure, even for a few milliseconds, is unacceptable - failure of exhaust gas temperature sensors can lead to the immediate shut down of the engine.
Exhaust gas temperature sensors are now mandatory for smaller engines with electronic injection, offering considerable business opportunities to a few instrumentation makers that are able to produce sensors with excellent reliability. This situation will not last forever. New alternatives have been developed in recent years to overcome the weaknesses of low cost PT1000 sensors by incorporating sought after features such as fast response time, long lifetime, vibration resistance, high temperature reliability, small diameter and low wiring and integration costs.
These solutions use miniaturised electronic convertors attached to each sensor, transforming analogue signals to digital ‘CAN’ protocol, conforming to ISO 11898 and SAE J1939 standards. Also, a simpler measurement harness, reduced to 4 wires instead of dozens, can be directly connected to the HMI using only one standardised port dedicated to digital input, relegating the need for an HMI acquisition box.
Builders of advanced digital protocol engines with electronically injected fuels can embrace the latest digital technology and will benefit from cost advantages and the reliability gained through rigorous testing and qualification programs. Engine builders for commercial applications are recognising the flexible advantage of digital technology that allows fast implementation of additional sensors, without any physical change in input/output ports of the Engine Control Unit (ECU), allowing additional reserves of sensors imbedded in the ECU. The complexity of harness design is also reduced as any additional sensors simply require an additional harness connector, without an increase in harness size or additional wiring.
Diesel engine awarded EPA Tier III certification
The US EPA Tier III NOx requirements entered into force in 2016 for Category 3 engine sizes (engines with a cylinder displacement at or above 30 litre/cylinder) to be installed in USA flagged or registered vessels. At the same time, the International Maritime Organization’s (IMO) NOx Tier III requirements also entered into force in North American and US Caribbean emission control areas (ECAs) from January 2016 for vessels with a keel-laying date on or after 1st January 2016 and an engine output of = 130kW.
Wärtsilä has announced another milestone achievement with regard to its Wärtsilä 34DF dual-fuel engine. The 34DF engine has been awarded the USA Environmental Protection Agency’s (EPA) Tier III certification for diesel mode operation when installed together with the Wärtsilä NOx Reducer (NOR) system.
The Wärtsilä NOR is a selective catalytic reduction (SCR) system that converts nitrogen oxides (NOx) with the aid of a catalyst into diatomic nitrogen (N2) and water. Wärtsilä is the first engine manufacturer to be awarded this certification.
The benefit of this award is that shipyards now need only a single party to certify both the engine and the SCR system for full compliance with the latest emission regulations. The Wärtsilä 34DF has already been awarded EPA Tier III certification of emissions compliance from the EPA in 2017 for operating in gas mode without an SCR system.
“This is a very meaningful achievement since it allows operators complete fuel flexibility when sailing in NOx emission control areas. It represents further validation of Wärtsilä’s technological leadership in working towards greater environmental sustainability and a cleaner shipping industry,” says Stefan Wiik, Vice President, Marine Power Solutions, Wärtsilä Marine Solutions.
The 34DF engine features advanced dual-fuel technology and high efficiency. For marine applications, it is manufactured in configurations from 6 to 16 cylinders covering a power range of 2880 – 8000kW. Based on the well proven and reliable Wärtsilä 32 diesel engine introduced in the mid-1990s, the Wärtsilä 34DF’s fuel flexibility means that the engine can be optimised for constant speed generating sets, as well as variable speed mechanical drives for main engine applications.
Couplings for tugboat winch
Tugboat winches operate under extremely harsh conditions. Often towing vessels that are many times the size and weight of themselves, their winches must overcome rough seas and extreme loads. Typically hydraulically driven, high pressure pumps are used to convert power from the ships’ engines to the winch.
The nature of the application means that the winches are not only expected to tow extreme loads, they will also experience incredibly high levels of shock loading as the movement of the two vessels will be affected by the water current and waves. With this in mind, hydraulic winches are typically specified over mechanical systems as the design will accommodate these challenges more readily.
One leading designer and manufacturer of tugboat winch systems has opted to specify hydraulic winches, using Stromag Vector couplings to accommodate the shock loading and misalignment inherent in the application and connect the winch’s hydraulic pump to the tug’s engines.
The manufacturer wanted to harness 450 HP from one of the tug’s twin 1500 HP diesel propulsion engines. The coupling would need to accommodate a large amount of radial and axial misalignment due to the sway of the resilient mounted engine. Further, it would be required to transmit extremely high torque loads reliably while also offering easy maintenance.
Stromag engineers identified the Vector 20 coupling as the best fit. The coupling utilises an elastic element concept with high tensile strength fabric embedded into the rubber. This extremely durable material allows the coupling to transfer up to 19,800Nm of torque with practically zero backlash. The flexibility of the elastic material accommodates high levels of misalignment in all directions while absorbing torque shock loads.
The coupling’s flexible element is incorporated in a radial arrangement which allows for installation and removal without the need to displace the connected equipment. This simple installation and maintenance procedure makes it suitable for marine applications where maintenance and repair operations may occasionally have to take place away from shore.
Bearings - standard & specials
In the offshore and marine engineering sector there is a requirement for reliable and effective turntable bearings that meet the sector-specific performance and safety standards. R. A. Rodriguez own-brand turntable bearings that not only fulfil these requirements but also provide off-the-shelf availability of the most popular part numbers.
These bearings are manufactured at the R. A. Rodriguez factory in Germany, using branded and in-house tested components. The products are specified from a wide choice of materials, coatings and seals to provide conformity with the relevant insurance certification.
Two basic versions of the standard R. A. Rodriguez turntable bearings are available. The KDL series is for light applications where high accuracy is not a pre-requisite and the KDM series which provides a higher order of performance for greater loads.
Both are manufactured, as standard, in high grade carbon steel or stainless steel and shipped pre-lubricated and ready for use. All bearings are of a proven, four-point contact design which allows them to support axial, radial and tilting moment loads. They consist of a single row of balls with a ‘gothic arch’ raceway and either spacer or spacer balls to ensure smooth running or one-piece separators for low frictional torque.
Standard bearing diameters range from 100mm to 3900mm and are available as flanged units or with external or internal gearing and induction-hardened raceways.
Immersible connectors
The new SWIM connector range (Shallow Water IMmersion) is designed for marine applications in depths down to 300m, which are considered shallow immersion. These connectors are designed for innovative applications like surface drones for environmental evaluation missions, maritime surveillance equipment, oil exploration, weather buoys, commercial diving and even for OCROVs (Ocean Class Remotely Operated Vehicles).
Using surface drones for oceanic observation requires them to have connections to numerous sensing devices (hydrophones, temperature sensors, salinity sensors etc.). The SWIM range satisfies all these connection needs.
It is not true because a connector is watertight at great depth that it will be equally so in shallow water. The watertight design has to take into account the pressure exerted on the seams, and therefore the immersion depth. With SWIM, the connector plug is screwed into the receptacle to lock both parts together and two O-rings at the mating interface ensure the connection stays watertight even at low pressure. The moulding of the cable to the plug adds to the watertight protection.
Manufactured in thermoplastic material, SWIM is resistant to seawater and temperature variations between -20 and +70°C over long periods. The screw mating and the coding pins make it easy to blind mate the plug with the receptacle, even with a large number of pins.
Vincent Mansour, Product Manager Marine: "Marine connectors contribute to system reliability by facilitating maintenance and increasing the modularity of the architecture. In military vessels, they resist the effects of shock and vibration and the "step" test. In a submarine, they ensure the continuity of the electrical connections between the watertight sections as well as connecting the on-board electronic equipment with the external sensors. For other commercial applications, for example to interconnect divers or Remotely Operated Vehicles (ROVs), SOURIAU connectors provide minimum external dimensions combined with high pin density and total reliability
Clamp technology for subsea well intervention
The two, first of a kind modular subsea clamps have been delivered to energy industry leader TechnipFMC for operation from the specialist well intervention vessel, Island Constructor.
The modular design will allow the capacity of the clamps to be adjusted for both shallow and deep-water operations, providing TechnipFMC with a highly flexible solution for use across a range of well intervention projects.
RED Engineering has been working with TechnipFMC for over 10 years and completed this latest project in under six months.
This included the design, build and testing of the clamps on a turnkey basis, with RED’s in-house test facility being used for rapid proof of concept and factory testing prior to delivery.
“The project offered a challenge to produce a pair of adaptable clamps that would safely retain two side-by-side umbilical cables,” said RED’s engineer, Mike Stobbart.
“As with previous clamps, these new ones feature spring applied pads to ensure a consistent and reliable clamping force is applied to the umbilicals. However, we have now added a hydraulic actuation system to improve the efficiency of deployment.”
Key Points
- Festo is uses digital pneumatics to control and monitor latch opening on the fingerboard of an oil exploration platform
- Advanced electronic component reliability allowing for better configuration and higher performance of marine horsepower engines
- For marine applications, Wärtsilä's 34DF is manufactured in configurations from 6 to 16 cylinders covering a power range of 2880 – 8000kW
- The new SWIM connector range (Shallow Water IMmersion) is designed for marine applications in depths down to 300m
- The business case for UPS
- Transforming industry with smarter automation
- Successful field tests for astronaut smart glove
- US and UK businesses show least confidence in AI amid global tech race
- Integrated Industry at Hannover Messe 2013
- Accelerating robotics from cloud to edge
- Airbus UAS in first free flight
- SCHUNK to invest 85 million euros in production sites
- Ford recruits robot test drivers
- Amazon invests €400m+ in cutting-edge robotics
- No related articles listed