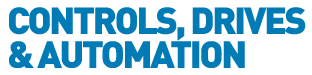
![]() |
Charlotte Stonestreet
Managing Editor |
How machine learning is transforming predictive maintenance
29 October 2018
Predictive maintenance is becoming essential to the smart factory. The ability to accurately track machine performance and anticipate failures before they occur is helping manufacturers improve overall equipment effectiveness and reduce wasted time and costs
Traditionally, plant managers relied on preventative maintenance schedules provided by a machine’s manufacturer, including regularly replacing machine components based on a suggested timeline. However, these timelines are only estimates of when the machine will require service, and the actual use of the machine can greatly affect the reliability of these estimates.
On one hand, this means that you could be paying for unnecessary maintenance plans and replacement parts that aren’t needed. On the other hand, many things can go wrong between scheduled maintenance visits. For example, if bearings wear prematurely or a motor overheats, a machine may require service sooner than anticipated. Furthermore, if a problem goes undetected for too long, the issue could escalate to further damage the machine and lead to costly unplanned downtime. Predictive maintenance helps avoid these problems, saving time and costs.
A leading solution for predictive maintenance is condition monitoring which plays a key role in predictive maintenance by allowing users to identify critical changes in machine performance. One important condition to monitor is vibration. Machine vibration is often caused by imbalanced, misaligned, loose, or worn parts. As vibration increases, so can damage to the machine. By monitoring motors, pumps, compressors, fans, blowers, and gearboxes for increases in vibration, problems can be detected before they become severe and result in unplanned downtime.
Uniform measurement
Vibration sensors typically measure RMS velocity, which provides the most uniform measurement of vibration over a wide range of machine frequencies and is indicative of overall machine health. Another key data point is temperature change (overheating). Machine learning takes this information and automatically defines a machine’s baseline.
However, collecting machine performance metrics is only the beginning. The ability to accurately interpret and communicate this data is essential for system reliability, and that’s where machine learning comes into play. Condition monitoring with machine learning will recognise the machine’s unique baseline of vibration and temperature levels and automatically set warning and alert thresholds at the appropriate points. This makes the condition monitoring system more reliable and less dependent on error-prone manual calculations.
Wireless condition monitoring is easy to deploy quickly. The ability to monitor machines in inconvenient locations allows for more comprehensive monitoring and increased reliability.
Based on a white paper from Banner Engineering: "Predictive Maintenance Trends: How Machine Learning is Transforming Machine Maintenance”
- Take part in CDA's 'Attitudes to Industry 4.0' survey & win a £100 Amazon voucher
- Starting made simple
- Inteq becomes new name for Invar Group
- Sage report into UK manufacturing sector
- Brexit study demonstrates importance of EU for UK robotic surgery research
- Elisa Smart Factory & TCS partner to deliver advanced analytics solutions to manufacturing sector
- Nineteen Group sells WBE magazines back to management team
- Optimising palletising productivity
- Centre of Excellence in emerging digital technologies opens in Liverpool
- Predictive tool to improve human-machine interactions
- No related articles listed