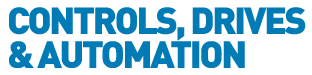
![]() |
Charlotte Stonestreet
Managing Editor |
Home> | DRIVES & MOTORS | >AC Motors | >PCB-Mounted Motors |
MORE FROM THIS COMPANY
RELATED ARTICLES
- HIGH EFFICIENCY
- BAE SYSTEMS TEAMS WITH QINETIQ TO DELIVER HYBRID ELECTRIC DRIVE
- Efficient Drives
- Loher motors available in UK
- HYGIENE SENSITIVE
- Surpass European Efficiency Levels
- EXTENSIVE STOCK & RAPID DELIVERY
- QUANTUM DELIVERS THE FACTS TO CLEAR UP THE FICTION
- IMPROVED MOTOR CONTROL
- Updated installation guide for power drive systems
OTHER ARTICLES IN THIS SECTION