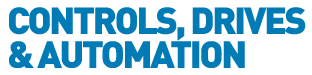
![]() |
Charlotte Stonestreet
Managing Editor |
Get the low down on dirty power
07 May 2013
In any industrial environment, poor or ‘dirty’ power quality can impact on energy efficiency and operational and financial performance says Kevin Lacey from Brammer UK
As well as increased electricity consumption, the hidden costs of poor power quality include downtime caused by excessive harmonic distortion, excess heat generation and reduced component life.
Most power quality problems relate to harmonics, created primarily by how current is drawn. Until the last 20 to 30 years, most electrical equipment drew current in a linear fashion, with smooth, repetitive current and voltage waveforms. However, many modern loads draw current in a non-linear fashion, with the current waveform regular but containing sudden peaks and troughs which can affect power quality.
Harmonic distortion
Many companies have already switched to low energy products. However, harmonic distortion can drastically reduce savings achieved, High-efficiency lighting products can have total harmonic distortion up to 80 per cent – meaning any savings could be more than cancelled out by clean-up costs.
Other harmonic distortion effects include increased transformer losses and nuisance circuit breaker tripping. Meanwhile, excess heat can cause breakdown of cable insulation; random thermal tripping of circuit breakers; transformer failures and, with third or triple-n harmonics, neutral overload.
Furthermore, capacitors naturally offer low impedance to high frequencies, absorbing harmonic current, making them heat up and reducing life expectancy. Combining capacitors with motor or transformer inductance can also cause undesirable resonance.
Random logic faults can occur in CNC equipment microprocessors, PLCs, drives, uninterruptible power supplies and computers, as well as silicon-controlled rectifiers (SCRs) found in DC drives, battery chargers and DC power supplies.
Other common issues include incorrect power readings and reinjection of harmonic currents into the utility network - highly significant because of ENA Engineering Recommendation G5/4-1, strictly limiting the distortion industrial users can place on the network. Sanctions are severe, usually resulting in supply disconnection.
Product-based harmonic reduction devices include six or 12 pulse drives, with choke or blocking filters, and active front end clean power technology. Site-based solutions include passive and active filters; surge protection and voltage reduction technology; isolation transformers; fault level increase bolstering; and power factor correction.
Power factor
In an electric power system, a low power factor load draws more current than a high power factor load for the same useful power transferred. Higher currents increase energy lost in the distribution system, and require larger wires and other equipment. Utility companies usually charge more where the power factor is low. Corrective action is achievable through standard capacitors or inductors on linear loads, although standard capacitors should not be used on motors fed by variable speed drives or soft starters, or on networks with active filters. For non-linear loads, the choice is usually between either passive power factor correction using a filter, or an active power factor corrector, controlling the load’s input current so the current waveform is proportional to the mains voltage waveform. Meanwhile, de-tuned automatic capacitors at the main switchboard will not resonate, overheat or prematurely fail in the presence of harmonics, will contribute towards power factor correction and may also absorb some 5th harmonic current.
Reducing voltage can also help lower electricity costs and stress on connected equipment, reducing the risk of blackouts and notching – which can cause equipment faults – and extending service life. All electrical equipment manufactured for the UK after 1995 can be run at voltages as low as 209V. The use of constant voltage transformers (CVTs) can help keep voltage within set tolerances, with savings of around 15% achievable on power use by reducing voltage from 240V to 220V.
Numerous companies offer independent, low-cost power quality surveys, identifying any areas of concern, suggesting how these should be addressed and giving an assurance that the site is compliant. They can also advise on how to negate problems associated with other ‘transient’ impactors on power quality, such as lightning strikes, and individual site requirements in the area of electro-magnetic compatibility.
Implementing these recommendations, alongside a strategic and sustained approach to power quality management, can contribute significantly to improving efficiency, maintaining productivity and reducing downtime, while creating impressive savings.
Key Points
- Poor power quality causes excessive harmonic distortion and reduced component life
- Savings from low energy products can be cancelled out by harmonic distortion
- Reducing voltage helps lower electricity costs and stress on connected equipment
- MRO products for hard environments
- Brammer to sponsor Hillhead 2014
- In the shadow of Concorde…
- Power transmission products
- GETTING THE BEST OUT OF GEARBOXES
- Efficiency In Tough Environments
- Brammer Buck & Hickman rebrand unveiled
- New regional MD for Brammer UK
- Encouraging energy compliance
- Quick guide to VSD specification
- No related articles listed