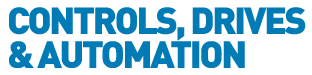
![]() |
Charlotte Stonestreet
Managing Editor |
Home> | DRIVES & MOTORS | >Variable Speed Drives | >Quick guide to VSD specification |
Editor's Pick
Quick guide to VSD specification
01 November 2013
Kevin Lacey from Brammer UK looks at what to consider when specifying variable speed drives
The benefits of variable speed drives (VSDs) are proven – energy-saving capabilities for centrifugal and regenerative type loads, process improvements, production flexibility, and an increased life for mechanical drive train components due to lower stresses, to name but a few.
But the specifier should not either under or over-specify in terms of the type, size and capabilities of VSD for their requirement.
Before selecting VSDs, the full motor specifications and load requirements must be fully understood to avoid sizing and selection errors.
The motor is a source of torque, which is relative to both power and speed, and the required torque/speed curves differ according to the application. When selecting a VSD, most applications are suited to either a variable or constant torque drive.
Variable torque rarely requires much more than 100% overload on start-up, although large fans with high inertias generally have long ramp times and so these drives tend to be rated for 110% overload for 60 seconds. The variable torque drive should have an adjustable parabolic v/f output to match the fan’s torque speed curve requirements and thus maximise available energy savings. It should also have a PI(D) input and where required the option for pump cascade control.
Constant torque loads generally feature in applications where the load remains constant across the speed range. It is important to know the overload requirements, as constant torque drives are rated differently between brands in terms of available power. Some typically list two or three options, for example ‘light duty’ of 100% or no overload, ‘standard duty’ at 120% and ‘heavy duty’ at 150% (based upon 60 seconds). A drive with ‘heavy duty’ overload will give the best chance of keeping the motor running in potentially unforeseen and demanding conditions.
Staying in control
The motor control mode should be understood to ensure correct drive selection. In general, constant torque drives range from simple and cost-effective V/F drives - ideal for applications without wide speed ranges or rapid load changes - through to the high-performance Vector Control series which, even in SLVC, offer near ‘closed loop’ performance without needing an encoder.
Likewise, with regard to interfacing and controlling the inverter, consideration should be given to input/output requirements, for example, the number of digital I/O and functionality, analogue I/O, PI or PID control, PTC/KTY input and so on. Field bus requirements - likely to be an optional extra - should also be established.
Generally, basic V/F drives have limited I/O while SLVC drives are better equipped. The controls needed are often likely to determine drive selection, and again onboard I/O varies between brands – sometimes with surprising omissions.
The method of stopping the motor can also have an impact. For a controlled ‘ramp to stop’, the motor can usually be stopped in about the same time taken to ramp it up, without any special braking requirements. If rapid deceleration is required, DC injection braking may be needed, although the number of stops and the load’s inertia should be considered to ensure this will suffice.
Another option is dynamic braking where a brake chopper ‘dumps’ excess kinetic energy fed back from the load across a resistor. Without accurate inertia information, precise sizing of the resistor(s) is not achievable, but usually the standard manufacturer’s brake resistor will have a reasonably high peak load rating and suffice.
Regenerative braking is also becoming a more popular solution for AC drives. This is a ‘specialist’ drive solution offering obvious advantages over the traditional 4Q DC motor solution in terms of maintenance while still providing energy savings by returning the regenerative voltage back into the mains.
Harmonic & EMC requirements
When AC drive inverters are operated, they have undesirable effects on the line supply. This is caused by the non-linearity of the device and the high control frequency of the output transistors.
The magnitude of these effects depends on factors including the characteristics of the line supply, point of common coupling, the type of inverter and power. End users will often not know much about their supply system, fault levels and existing harmonics, meaning that without a power quality survey, specifying the right drive is a matter of judgement.
In general, when specifying standard drives the best advice is to recommend an input choke, especially for 1AC drives 3kW or over and 3AC drives 37kW and over. To meet a specific EMC level a choke may also be mandatory.
The decision on whether an output choke is required will depend largely on the length of the motor cables (combined if more than one motor is being driven) and whether the cable is shielded or not.
Finally, the end user will often be able to specify whether an RFI filter is required. This is generally a must for 1AC fed drives. Once selected, correct installation and commissioning is vital – indeed, any VSD will only perform as well as it is commissioned.
Key Points
- It is important not under- or over-specify a VSD in terms of type, size and capabilities
- The motor control mode should be understood to ensure correct drive selection
- When AC drive inverters are operated, they have undesirable effects on the line supply
- PUMPED UP PERFORMANCE
- SOFT STARTER OR VARIABLE SPEED DRIVE?
- Jeans With Less Energy
- Enhanced to Withstand Tough Environments
- Savings From Improved Torque Ratio & Efficiency
- Modular VSD
- ENERGY SAVING: AN OLD MESSAGE WITH NEW PROMISE
- Updated installation guide for power drive systems
- UK drives manufacturer seals global automation deal
- WEG motors & drives power high-efficiency air blowers