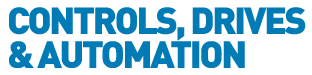
![]() |
Charlotte Stonestreet
Managing Editor |
Home> | POWER TRANSMISSION | >Gearboxes | >GETTING THE BEST OUT OF GEARBOXES |
GETTING THE BEST OUT OF GEARBOXES
31 October 2012
In any industrial environment, the management of plant-critical assets is integral to maintaining productivity and reducing downtime, says Jeremy Salisbury, Brammer UK
At the heart of many manufacturing processes, the industrial gearbox often has to perform under arduous conditions. By employing effective maintenance and repair procedures, the risk of premature gearbox failure can be significantly reduced. Indeed, paying particular attention to factors such as lubrication, oil and vibration analysis can help sustain a gearbox’s service life, avoiding costly replacements and rebuilds.
Where unplanned downtime is simply not an option, gearboxes must be inspected regularly and repaired and refurbished as necessary to enable their continued operation. In addition to regular visual inspections, companies can help to maintain production schedule adherence and maximise their production efficiency and asset effectiveness by using condition monitoring equipment.
Condition monitoring – for example vibration analysis – can help identify a problem before it creates a line stoppage, allowing for maintenance for replacement or repair with minimal disruption during the next convenient plant downtime. Furthermore, it removes the need for gearboxes to be changed on a time basis – possibly when change may not be required – and instead allows for change on a condition basis, which can extend service life and maintenance intervals.
CONTAMINATION
Contamination is a major cause of gearbox problems. Oil contamin - ation can reduce the operating life of rolling element bearings. Any failure in this area will certainly damage other components and may lead to a catastrophic failure of the gear train.
Water contamination will cause gear oil to break down, affecting the performance of the oil between the teeth of the running gear train, causing increased wear.
Finally, corrosion-induced fatigue failure is a possibility if pitting is allowed to occur.
However, this is a far less likely outcome than a problem created by solids in suspensions and sludge formation inside the unit – these issues can be minimised through regular, planned maintenance. A detailed maintenance schedule with reports on condition and actions undertaken is also critical to maintaining the conditions of warranties and guarantees.
It goes without saying that gear oil should be changed at the interval specified by the manufacturer. If contamination is an issue, additional filtration systems may be required.
Noise and vibration analysis of the gearbox under normal operating conditions will help identify any problems, and a detailed visual inspection should also occur. For this, the gearcase inspection covers should be removed and the interior inspected for signs of contamination, and the gear teeth and rotating components checked for visible wear.
A full inspection, required less frequently, should involve removing gear internals from the gearcase, removing shaft end covers, inspecting the bearing bores, removing sludge deposits and thorough cleaning. The gear train should be completely dismantled, with all components cleaned and inspected. All oilways should be checked to ensure they are clear, and any sludge removed.
Gears and shafts should be checked for excessive wear, cracking and concentricity.
APPROPRIATE REPLACEMENT
Industrial gearboxes generally have a considerable service life and, if they do fail, can usually be repaired or reconditioned. However, their performance and energy efficiency after reconditioning may make replacement with a more energyefficient product advisable.
Each application should be thoroughly examined and a decision made on the right way forward. Energy savings of up to 20% can be achieved over traditional worm boxes by installing either a helical bevel or planetary gearbox, depending on the application.
Where numerous gearboxes are in use, the time spent maintaining them can be considerable, particularly if maintenance intervals are simultaneous. An increasingly popular option is to outsource the entire gearbox management and maintenance function to a specialist partner familiar with all makes of gearbox.
Outsourcing in this way gives the flexibility for gearboxes to be overhauled simultaneously, with independent advice available on when it makes more sense to replace than to repair, and on the most economical and energyefficient way forward when replacement is indicated.
Key Points
• By employing effective maintenance and repair procedures, the risk of premature gearbox failure can be significantly reduced
• Condition monitoring can help identify a problem before it creates a line stoppage
• Energy efficiency after reconditioning may make replacement with a more energy-efficient product advisable
- Fan Solution
- New regional MD for Brammer UK
- Brammer & CEJN connect
- Get the low down on dirty power
- Supplier of the year award
- Engineering service centre capability boosted
- 1000s of products just a click away
- Efficiency In Tough Environments
- Brammer to sponsor Hillhead 2014
- In the shadow of Concorde…
- GEARBOX IS CHEAPER TO REPLACE THAN REPAIR
- PLANETARY/SPUR GEARBOXES
- PLANETARY GEARS WELL SUITED FOR RETROFIT
- AGEING WORM GEARS REPLACED BY PLANETARY GEARS IN SEWAGE PLANT
- REHFUSS BRINGS QUALITY AND VERSATILITY TO GEARBOX DESIGN AND SELECTION
- FLEXIBLE COUPLINGS
- A Guide to the Selection
- Greater Corrosion Resistance
- Fits existing parameters
- Brammer awarded Tata Steel Europe contractor of the year