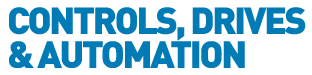
![]() |
Charlotte Stonestreet
Managing Editor |
The route to energy saving efficiencies
26 April 2013
Nigel Evenett, motor specialist at Lafert Electric Motors, looks at the benefits to be gained from investing in energy efficient electric motors
Energy efficient motors are not new and the benefits are well known but, as always, it is a matter of the OEM educating/convincing the end user that it is worth the initial investment in a higher efficiency to gain the benefit from minimising the ever growing running cost.
To increase the efficiency of a three phase squirrel cage induction motor (SCIM) more active material has to be used, this in turn, results in a heavier motor and a higher cost. This simple but effective design solution has been applied to all previous voluntary or mandatory increases in efficiency, so when the Commission Regulation (EC) No 640/2009 implementing European Directive 2005/32/EC which came into force on 16 June 2011 most motor manufacturers were prepared for it.
This regulation made IE2 levels of efficiency mandatory within Europe and also laid down a time table of efficiency improvements, the next level being in January 2015 when motors with outputs between 7.5 - 375kW shall be at the higher IE3 level or be IE2+Variable Speed Drive (VSD). In January 2017 this same Directive then incorporates motors with outputs between 0.75 – 375Kw.
These increases in efficiency up to IE3 levels can still be achieved by adding active material into the SCIM and by designing out some of the smaller losses. The situation remains that to achieve the IE3 efficiency levels the motor is a larger and heavier beast than it once was. When the newly established IE4 efficiency levels become mandatory the SCIM will be more difficult to select because of this and the alternative technologies now available to motor manufacturers to achieve the required higher efficiencies.
Greater power
As a major European manufacturer Lafert will continue to offer as much as is practical in the SCIM but for motors between 0.75 and 30kW the Group can offer an innovative alternative. Drawing upon the Group’s experience with permanent magnet servo motors and drives, Lafert is able to provide a smaller, lighter motor solution that will comply with the IE4 efficiency level.
By integrating the standard components of the squirrel cage induction motor with the permanent magnet rotor of the servo motor Lafert have developed their High Performance range. The major advantage with this solution is that the power/weight ratio is lower rather than higher. Also, in many cases the IEC frame size reduces by two (see diagram example 5.5kW 3000 rpm). The system needs a sensorless drive and many standard drives can be configured for it. Another key benefit is that the efficiency remains high over a wide speed range not just at the duty point.
Lafert have developed two configuration types: the ‘HPI’ which includes the drive as an integral unit with the motor, and the ‘HPS’ which is a more conventional stand-alone motor and drive. The HPS is particularly appealing to the OEM because they can benefit from the use of standard motor components plus the option of Lafert’s motor customisation capabilities.
The EU’s eco-design demands now extend to fans, pumps and compressors with the first tier of efficiency levels already introduced in January this year and the second tier scheduled for January 2015. This ErP (Energy related Products) regulation covers the whole fan/pump/compressor system so a higher efficiency in the motor can compensate for higher losses in the fan or vice-verse.
The Lafert IE4 Permanent magnet synchronous motor (PMSM) solution helps OEM manufacturers of these products to achieve these mandatory efficiencies but in addition gives them the opportunity to both reduce the weight and size of their products.
- No related articles listed