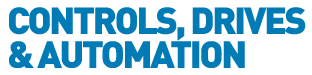
![]() |
Charlotte Stonestreet
Managing Editor |
Home> | DRIVES & MOTORS | >AC Drives | >Technology wins on aggregate |
Home> | AUTOMATION | >Networks | >Technology wins on aggregate |
Home> | AUTOMATION | >Robots | >Technology wins on aggregate |
Technology wins on aggregate
09 May 2013
From drive train upgrades to robotic palletising systems, CDA takes a look at some of the latest equipment to find application in the mining and quarrying sectors
Although certain sectors are by no means as prolific as they once were, mining and quarrying are still carried out on a large scale in the UK. There are around 2100 mine and quarry sites are worked and UK coal mining produces 17,874 thousand tonnes each year – 7520 thousand tonnes from deep mining and 9854 thousand tonnes from surface mining.
Companies in these sectors are often large and power hungry; with sizeable aggregate operations sometimes using as much energy as a small city. Little wonder then, that the Carbon Trust has suggested a target for aggregate companies to reduce their emissions by 20%. Not only will this have a positive effect on CO2 emissions, it will also result in reduced energy bills.
An essential part of any mining or quarry operation, making optimum use of drives and motors is one of the ways in which companies can maximise efficiency. In one recent example, a rock salt mine in Cheshire reviewed the condition of its existing main hoist and concluded it should be replaced with a more efficient drive system from Brevini Power Transmissions.
With the original hoist equipment, driven by a helical gearbox, installed in 1973, concerns were raised over the reliability and safety of this plant. The main contractor responsible for the scheme who was to replace the drive system, approached Brevini Power Transmission, a long term supplier of drive solutions, to advise on the project. Initial site investigations showed the full extent of the complications that would have to be overcome in order to ensure a successful conclusion.
The original hoist lifted a 9t skip over a distance of 155m in just over 1 minute. To capitalise on the work which would be carried out it was decided that the new equipment should offer improved capacity, as well as efficiency and reliability, so the site would benefit from improved productivity once the project was complete.
The new motor power was specified at 780kW at a speed of 590rpm with the required output speed of 21rpm. The duty cycle would see the skip accelerate for 10 seconds, travel at nominal speed for 25 seconds before decelerating for 10 seconds and unloading. This must be repeated for 24 hours per day, six days per week - a very demanding schedule and one with little margin for unplanned maintenance or repair work.
With the specifications laid out, Brevini was set the challenge of designing the new gearbox, while the engineers from the main contractor planned how the exchange would be carried out. The new drive had to be designed in such a way that it would fit into the footprint of the original helical gearbox and not interfere with the existing machinery which was to be retained. This included the original tacho drive system, which provides real time data on the position and speed of travel of the hoist. The whole project to remove and install the new gearbox would all have to be completed inside a very tight timeframe.
The layout of the original drive train included the gearbox and coupling as well as a long driveshaft which would have to be cut and then machined to match the new drive coupling supplied by Brevini. Clearly, once the shaft had been cut there would be no turning back and the new drive system would have to be successfully installed and commissioned to meet the client’s production requirements.
The engineers at Brevini based the gearbox design one of the largest models of the PIV Posired 2 range, the PD85 gearbox which was modified to ensure that it fitted in to the space available when the original drive was removed. Weighing in at around 13 tonnes, the operation of replacement would require careful planning and coordination by all the engineers involved.
The output shaft of the PD85, measuring 370mm, was designed for a shrink fit to the drive coupling which was also supplied by Brevini. The final connection to the driveshaft of the hoist would require on site machining before the whole installation could be commissioned.
Dave Brown, sales manager for Brevini UK, comments: "This was a project with a number of challenges for us, not least the tight timeframe for delivery. We have delivered a bespoke solution to meet the exacting requirements of the client by using our expertise in the field of heavy duty drive applications. More and more of our retrofit work for similar applications is being won on the basis that we will provide a customer-specific solution, rather than something off the shelf, but without the traditional downsides of cost and long lead times.”
Reduced noise & vibration
The new hoist drive was successfully commissioned on time and the rock salt production continued to plan. Not only does the new drive system provide reliable and efficient service it has also considerably reduced the noise and vibration levels within the shaft and increased the mine's output capacity. The new gearbox has also reduced the maintenance requirements on the hoist system allowing the engineers to concentrate on other areas of the mine.
The Posired 2 range of gearboxes is a series of universal modular drives with a wide range of accessories and options. It is available in 25 different sizes with nominal output torques up to 1,000 KNm. This versatility and ease of use makes the Posired 2 range well suited to a wide variety of applications and are able to satisfy the majority of clients' needs.
Comms technology
There are also benefits to be gained from implementing the latest connectivity technologies, as Austrian contractors, Rankweil found out during its upgrade of the BSL Lorüns crusher and screening plant BSL. In addition to changing over to a state-of-the-art process control system and replacing the entire power section, Eaton‘s new SmartWire-DT communication and connection technology was also implemented in combination with the PKE electronic motor-protective circuit-breaker.
Experts in the field know the problem of starting iced up elevating conveyors in the morning in freezing temperatures all too well: The stiffness of the empty conveyor belts due to frozen water in the belt pockets causes the motor currents to increase right up to the operating limits. When material is then added, the drive enters the overload range and the motor protection shuts down the conveyor. A restart is then mostly only possible after the conveyor line has been emptied by tediously shovelling off the conveyed material by hand.
After upgrading the sand and gravel plant with SmartWire-DT, the iced up belt can be automated to "run warm” until the operating current has dropped to "idle running”, and only then is material conveying enabled. Any accidental material conveying and likewise any excessive warm running are prevented. A far greater benefit for BSL is the controlled operation of the plant close to its maximum output limit, i.e. optimised and safe plant operation.
This is because varying total weights are transported at the Lorüns crusher and screening plant, due to the humidity and grain size of the transported material. The outstanding benefit is the enhanced drive monitoring functions: The actual motor current can be displayed and evaluated continuously without the need for any expensive analog I/O technology.
With conventional motor control using motor-protective circuit-breakers and contactors, the switching states of both components (ON) are interrogated to make an indirect evaluation of the operating state and the detection of a standstill.
A hardware solution such as a speed sensor, load shedding relay etc. is required for a real and reliable feedback signal. When the set current value of the drive is exceeded in the event of an overload, the drive is shut down immediately in order to protect the motor from being destroyed and a fault is indicated. This results in several unplanned breaks in operation that can take a lot of time to rectify and often involve high downtime costs.
It is in this particular aspect that SmartWire-DT shows its tremendous benefits: The evaluation of the actual operating current makes it possible to distinguish between the following six operating states at BSL (according to the drive task):
- Motor switched off
- Motor underload
- Motor idling
- Motor operation
- Motor overload
- Motor fault
The individual load limits as well as the time characteristics can be programmed as required for the particular drive application at hand. This enables the plant operator to detect imminent faults early on and enables interventions in the production process before an unscheduled interruption occurs.
Manfred Keckeis, general manager at Keckeis Elektrotechnik, Rankweil Austria, made this assessment: "The decision made jointly with BSL to not only upgrade the power section but also to replace it with SmartWire-DT in combination with Eaton‘s PKE electronic motor protection has not only paid for itself very quickly in terms of investment but also in terms in system availability. As well as the neat and extremely fast "wiring” of SmartWire-DT, its space saving design was particularly ideal for the limited space available in the control room. The aim is also to give our customer a convenient solution that is easy to operate. SmartWire-DT‘s status messages and self-diagnostics options are therefore a tremendous help.”
Robotic palletising
In a custom installation thought to be the first of its kind, Pacepacker Services has built a containerised sack packing and robotic palletising line for Suffolk-based aggregates supplier Earsham Gravels. The investment has not only doubled capacity and reduced reliance on manual labour, but also given Earsham Gravels a portable turnkey line that can be easily transported between quarries.
Earsham Gravels bags aggregates, from sand to gravel, shingle, limestone and granite, into plastic sacks for trade customers supplying the DIY and construction industries weighing up to 40kg. Historically, aggregates were bagged on a manually operated line, but as the company’s customer base expanded, this became unworkable.
Earsham Gravels tasked automatic packing systems specialist Pacepacker with designing an automated line that would fit within a purpose built trailer container, enabling the equipment to be transferred with ease to different locations. The kit needed to be compact enough to fit within the confined space, measuring 40 x 8 x 8ft, and robust enough to withstand the harsh quarry environment where it is situated as the aggregates are often abrasive and wet which can damage and corrode machinery.
Pacepacker built a portable turnkey cell incorporating its innovative Total Bag Control (TBC) sack closing system, its C21 sack placer a bag kicker, a bulk hopper and a weigher. Within the container, the sack placer opens the empty sacks and presents them to the aggregate specification weigher, for filling from the bulk hopper. The TBC system then takes hold of full sacks with a pair of motorised grip arms and motors toward the sealer, "As the bag top is held at all times prior to sealing, the system stabilises the bag throughout the closing process,” explains Paul Wilkinson, Pacepacker’s business development manager. "To ensure the TBC can cope with harsh conditions, all parts that come into contact with the aggregates are made from stainless steel, and the feeder uses heavy duty rubber belting.”
Following the success of the first portable turnkey cell Earsham Gravels constructed a second purpose built trailer which Pacepacker equipped with a FANUC R2000 palletising robot. Once sealed within the first container the sacks pass through a sack kicker and into the second container, where they travel to the FANUC R2000 palletising robot via a flattener conveyor with powered rollers, followed by a ‘pick’ conveyor, whose roller design and spacing facilitates picking of the sacks.
The six-axis robot loads sacks onto two pallet stations, which are rotated and wrapped before being taken away by fork lift trucks. Earsham Gravel reports that automating the line has ramped up bagging speeds from five or six sacks per minute to nine or ten sacks per minute.
Key Points
- Main hoist at a rock salt mine replaced with a more efficient drive system from Brevini Power Transmissions
- Eaton's SmartWire-DT communication and connection technology implemented at crusher and screening plant
- Containerised sack packing and robotic palletising line from Pacepacker increases aggregate bagging speeds
- Severstal invests in robotics to automate advanced composites manufacturing
- Control systems to combat climate change
- Force-controlled parallel robot
- Cutting-edge motor-drive design hub
- Ways to reduce waste
- Kawasaki Heavy Industries to expand production in China
- Fuelling innovation
- Selecting soft starters for use with IE3 motors
- The smart answer to maintenance management
- AI model generation service