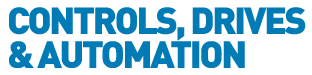
![]() |
Charlotte Stonestreet
Managing Editor |
Distributed units replace servos
26 June 2013
After extensive consultation with NORD Drivesystems, Sacha Bakker, managing director and co-owner of Dutch engineering company SYMACH Palletizers, made the decision to incorporate distributed drive technology in the company’s equipment.
NORD drive units, comprising geared motors and distributed frequency inverters, provide dynamic performance and design possibilities that result in improved reliability and cost savings. The first series of palletisers with integrated motor control is now being used successfully throughout the world.
In contrast with other available systems, Symach palletising machines place products on the pallet individually, using a specially designed manipulator head that allows both precise and gentle handling. In the past, Symach always used centralized drive control units, which required switching cabinets to be mounted on the top of the machine. This took up a lot of space and resulted in additional costs.
"The height of a palletising machine requires the installation of steps in order to carry out maintenance work,” explains Bakker. "The switching cabinets for the servo controls obstructed access. By converting to compact NORD drive units, it was easy for us to eliminate this problem.”
In the new palletisers, geared motors with SK 200E series frequency inverters mounted directly on the motor perform the complex movement sequences of the manipulator and the centreing unit.
Following the recommendation of NORD, it was decided to use dynamic asynchronous induction motor technology instead of servo technology. The advantages of this solution not only include lower procurement costs, but also greater selection possibilities for machine designers, as asynchronous induction motors are widely available, maintenance-friendly, and can be easily combined with various types of gear units. In addition, the shaft and flange mounted versions are easy to replace. In total, these advantages mean that ‘asynchronous palletisers’ incur lower overall operating costs than palletisers equipped with servo motors
Tailor-made solutions
Distributed automation applications place great demands on drive systems. Comprising several performance-graded models and various functional upgrade options, NORD’s SK 200E frequency inverter series enables users to select tailor-made solutions for each specific requirement. Models of sizes 1 to 4 cover performances between 0.25 and 22 kW. The modular series enables the economic implementation of distributed applications ranging from simple start-stop control functions to complex positioning tasks. Upgrade options include external brake resistors and a separate 24 V power supply for stand-alone control voltage regulation.
In addition to fieldbus interfaces for CANopen, DeviceNet, and Profibus there are also gateways for integration into PROFINET and EtherCAT networks. Interfaces for further industrial Ethernet standards are currently being developed. The fieldbus communication interfaces are available as external bus technology units with or without additional I/Os, which can be mounted directly on the inverter or separately on the machine frame or nearby equipment.
Symach palletising machines use the POSICON function, a standard feature of all SK 200E frequency inverters, which enables highly dynamic positioning functions with a maximum precision of approximately 1/100 of a rotation of the motor. The new and very compact NORD MG encoder system is used to detect position and orientation.
The distributed inverter enables considerable simplification of installation and wiring. The drive manufacturer supplies the ready-wired motor, brake resistor, and motor holding brake.
Symach uses machine-integrated SK 215E inverters with the additional ‘Safe Stop’ function, which ensures the necessary personnel safety. Further features of the versatile SK 215E units are used in the palletising machines: sensors and actuators are simply connected to the inverter I/Os with information sent to and from the control unit via CANopen communication. This also reduces the number of cables which need to be wired.
Key Points
- Dynamic asynchronous induction motor technology used instead of servo technology
- Advantages include lower procurement costs and greater selection possibilities for machine designers
- Distributed inverter enables simplification of installation and wiring
- More communications options
- Crane drive synchronisation
- NORD joins GATE
- Servo-level performance
- Two-stage helical bevel gearboxes
- New no frills frequency inverter
- Competent support for economical and energy-efficient drive systems
- Drive units for baggage handling
- Smaller Models
- Rotary feeder drive solutions
- No related articles listed