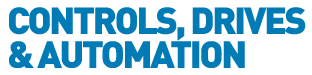
![]() |
Charlotte Stonestreet
Managing Editor |
Not all inverters are created equal
15 January 2014
The belief that all AC Inverters are created equal is exacerbated by the fact that inverters are often bought as commodity items, much like control gear. However, at least with regard to dynamic braking, this isn’t the whole story. Here, CP Automation investigates why anyone incorporating a drive into a system should think twice about their real needs before clicking ‘buy’.
There is a real danger in the specification of inverters for use in heavy duty applications - that is that most drives, fresh from the manufacturer, even ones with onboard brake choppers, will not be rated sufficiently for the braking demand of the application.
As a result, non specialist engineers can be faced with an extremely complex task when asked to choose the correct inverter, resistor and brake-chopper combination for a project.
To help counteract this problem, CP Automation has launched an external brake chopper unit that simplifies the process of inverter selection. Where an inverter doesn’t feature a built-in brake chopper, the new CP Automation unit, manufactured to the highest standards by TAE Pikatron in Germany, can supply that functionality. It’s a universal model that works with any inverter, from any manufacturer.
"However, the fact that a product is universal doesn’t simplify the selection process by itself,” explained Tony Young, managing director of CP Automation. "You also need to ensure that you choose the right integration and maintenance partner, who is not tied into a limited range of drives from a limited range of manufacturers.
"A good partner will provide an honest view of whether you already have the correct resistor and, if you don’t, supply one as part of a package to help meet your specific objectives.
"For instance, if the original inverter already had a brake chopper onboard it may be that the Ohmic value of the existing resistor doesn’t meet the criteria of the new one. This can lead to damage to the drive system and its environment and, in worst case scenarios, create health and safety problems.”
An additional benefit of the product’s universal nature is that, should a brake chopper and inverter package be installed - either along with the inverter or as a retrofitted item - and the inverter then fails, the end user can simply install any drive, from any manufacturer. The brake chopper and resistor package doesn’t tie the user to certain equipment, as the equivalent brought direct from the drives manufacturer would.
"It’s not unusual for an end user to have a range of drives in stock on their shelves,” explained John Mitchell, CP Automation’s business development manager. "This can even be true if the company has a single source policy. There is often older equipment that is still fully functional, sitting around on the shelf. From a pragmatic point of view it’s better to use the equipment already in stock and reduce downtime and its associated costs. I believe this is still true, even if you ultimately replace it with the single sourced option to ensure a fixed topology of devices.”
The seventh IGBT
Many drives manufacturers design and build their products with a seventh IGBT (Insulated-Gate Bipolar Transistor), in the form of a brake chopper, incorporated into the device. This isn’t true of every model and make, but it is common. However, if the end user isn’t aware that they need to check for the presence of the seventh IGBT, which is often only signalled by one digit in a twenty digit part number, it’s very easy to buy the wrong piece of equipment.
Often you will find that manufacturers will include a brake chopper up to a certain size of inverter, but beyond that size expect an external unit to be used. However, to reduce the cost of the drive to the end user, the seventh IGBT isn’t necessarily rated to the full power rating of the drive itself.
This isn’t to say that the built in brake chopper isn’t suitable for the drive – it may well be perfect from a general technical specification perspective.
However, if, for example, you have an eleven kW inverter, it may only have a 5.5 kW IGBT installed. This would mean that the braking unit would only be rated for 50 percent of the inverter’s capacity, and can result in the overall system simply not stopping fast enough. Furthermore, this isn’t a theoretical concept; it’s a very common problem that integrators up and down the country encounter on a regular basis.
Because it’s not possible to retrofit an internal brake chopper into the drive, a customer who has ordered the wrong part has no choice but to incur further cost, design time and potentially downtime by engaging a third party to provide a retrofit brake chopper.
Underrated IGBTs
Most inverter manufactures will argue that the cost benefit of not rating the IGBT to the full capacity of the drive is more than worth the loss of braking capacity. And there is an argument that this is a legitimate design decision - most manufacturers will claim that a very high percentage of end user applications don’t actually the full braking capacity.
In very light duty applications, such as emergency stop applications for instance, underrating the built in brake chopper wouldn’t be a problem. In fact, anything that is up to ten percent duty will be very unlikely to suffer any kind of issue at all.
In contrast, any kind of application where the drive system has to stop and start regularly, such as an elevator or conveyor, needs to pay more attention to the brake chopper.
The real problem is not the manufacturer’s decision to install a low capacity IGBT but the decision to not make this information very clear in the manual and the accompanying documentation.
"The key point is that in any application the mechanical stopping of the load is just as important as selecting the drive system,” explained Mitchell. "For instance, a fifty metre crane that lowers at half a metre per second will clearly take 100 seconds to lower fully. It may only do that twice per day, but the point is that when it does, it is operating at full capacity, not 30 percent or 50 percent. From a chopper and resistor point of view, that’s a continuous period that the drives onboard brake chopper couldn’t cope with.
"The drive manufacturer might argue that this only represents twenty percent duty but that’s where the application knowledge of the integrator or maintenance team becomes crucial. During the 100 seconds of descent, the application is dumping more and more energy and the resistors are getting hotter and hotter. It could be quite dangerous to attempt this kind of application with an inadequately sized internal seventh IGBT.”
The key to successful brake chopper integration is that the designer has to check the drive data before specifying the system. "All the details are there,” Mitchell explains. "But you do have to go and proactively look for them. One of the key values that we bring to our customers is that we take that pain away and make the entire process very simple. Our warning is that not all drives are created equal and the presence of the seventh IGBT doesn’t guarantee adequate braking performance for the system.”
Key Points
- Where an inverter doesn’t feature a built-in brake chopper, CP Automation's external brake chopper unit, can supply that functionality
- Many drives manufacturers design and build their products with a seventh IGBT (Insulated-Gate Bipolar Transistor)
- For successful brake chopper integration the designer has to check the drive data before specifying the system
- SME partnership promotes motor customisation
- Active harmonic filters
- Scaling-up drive production
- Tips for mitigating harmful harmonics
- Re SpA appoints CP Automation as sole UK distributor
- Active and passive harmonic mitigation
- The race to replace
- Active & passive harmonic
- Detailed product info
- Distributor recognised
- No related articles listed