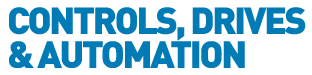
![]() |
Charlotte Stonestreet
Managing Editor |
The race to replace
04 April 2016
When aged legacy motors, drives or control systems in heavy industries need replacing, finding the right balance between cost, power, energy efficiency and simply doing the job can be tricky
When Tata Steel wanted to replace a 40-year-old motor used in one of its pipe manufacturing facilities, the company worked with Rockwell Automation and repair and supply specialist CP Automation to find a solution that boosted overall production and energy efficiency.
Tata Steel's Hartlepool SAW (pipe) mill, located in the North East of England, has three manufacturing facilities with a combined annual production capacity of 440,000 tonnes of tubular products for the construction, engineering, energy and power markets. At the very heart of the production process lies a powerful expander used to shape, size, and strengthen pipes.
The expander’s large gripper car moves 12.5m long pipes over the expander head and, until recently, a 40-year-old DC motor drove the gripper car. The motor used an obsolete control system that was not very accurate and, as a result of the low speed, it often caused bottlenecks in the production process.
Because of its age, the DC motor also required frequent maintenance and had high-energy consumption rates. As the motor was obsolete, the spares and DC drives it required were hard to come by, so the entire application had a serious reliability issue.
CP Automation worked alongside Rockwell Automation and Tata Steel to identify, deliver and install a replacement motor and drive for the application.
The right fit
“The need for better energy efficiency and accuracy meant an off-the-shelf motor and drive system simply wouldn’t suffice,” explained John Mitchell, global business development manager of CP Automation. “To fulfil the requirements, we worked with Spanish motor manufacturer and partner VASCAT to produce a bespoke 150kW motor, at 300Amps and with a speed of 1070rpm. Rockwell supplied the 250kW Powerflex 755 inverter drive with CIP motion function and associated PLC.”
The motor had to be about the same size as the previous one and come with pre-installed cabling so it was easy to position on the existing motor plate bed. The new motor is 1m long by 0.75m wide and weights 853kg.
“When the motor, drive and PLC were up and running, the stop and start function wasn’t as fast as we wanted it to be, partly because of the sheer size of the motor," explained Tony Brown, electronics engineer at Tata Steel. "The drive kept tripping, so we needed to find a solution.
“CP Automation suggested introducing a Revcon regenerative braking unit to make stops and starts more seamless and to increase the speed of the application. This is where we really reaped the benefits of the new equipment, both in terms of speed increase and energy efficiency.”
Clear improvements
“Perhaps one of the most significant improvements in the process came from the accuracy of the new servo drive system,” explained Brown. “The new drive system allows us to position the pipe within 1mm accuracy, whereas the old DC system’s accuracy was closer to 50mm. This increased level of accuracy coupled with a ten percent improvement in speed has resulted in productivity improvements throughout the application.
“The success of the project convinced us to replace the auxiliary drive system on the expander,” continued Brown. “We have already discussed the details with CP Automation and Rockwell and are hoping to upgrade the auxiliary drive unit during the 2016 summer shutdown.”
In an era of Industry 4.0 and smart factories, the temptation to fully replace an obsolete production line is high. However, this isn’t always the most cost-effective or productive approach. Sometimes it’s better to just replace the inefficient or unreliable parts of a system – and these are often the parts that work the hardest, like motors, drives or pumps.
Key Points
- 40-year-old DC motor with obsolete control system was causing bottlenecks at Tata Steel's Hartlepool SAW (pipe) mill
- CP Automation worked with Rockwell Automation and Tata Steel to identify, deliver and install a replacement motor and drive
- Increased accuracy coupled with a 10% improvement in speed has resulted in higher productivity
- Active and passive harmonic mitigation
- Scaling-up drive production
- Detailed product info
- Distributor recognised
- Active & passive harmonic
- SME partnership promotes motor customisation
- Not all inverters are created equal
- Re SpA appoints CP Automation as sole UK distributor
- Tips for mitigating harmful harmonics
- Active harmonic filters
- No related articles listed