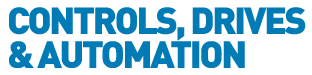
![]() |
Charlotte Stonestreet
Managing Editor |
Home> | POWER TRANSMISSION | >Brakes | >Scaling-up drive production |
Home> | MACHINE BUILDING & ENGINEERING | >Machinery | >Scaling-up drive production |
Scaling-up drive production
30 November 2023
Invertek Drives has achieved sustained growth and enhanced energy efficiency through a series of incremental improvements, bolstered by CP Automation's innovative regenerative braking and harmonic mitigation technology

BASED IN Wales, Invertek Drives specialises in the design and manufacture of variable frequency drives (VFDs). The company assembles, customises and tests the VFDs on a bespoke process line, or global assembly cells (GACs). A GAC is a chain of connected workstations, each performing a step in the production and testing process. GACs are modular, enabling Invertek Drives to scale-up production by adding more workstations to help meet increased demand.
The partnership begins
Originally, Invertek Drives used third party DC drives and motors and braking resistors on its GACs to test the VFDs that it manufactured. However, DC motors require more maintenance than their AC counterparts, particularly with regards to replacing the brushes.
The DC motors were also creating noise and heat, requiring a blower motor to keep them cool when running. As Invertek Drives expanded and added more GACs to its facility, the team found that power consumption was a growing challenge and contacted CP Automation.
CP Automation initially recommended switching to AC motors and fitting a REVCON regenerative braking unit to each GAC to capture and recycle energy otherwise lost to the braking resistors. The move to AC also allowed Invertek Drives to use its own VFDs to test its products, reducing reliance on third party suppliers.
“As our production process evolved, energy saving was a key priority for us,” explains Peter Evans, manufacturing engineering manager at Invertek Drives. “At first, we were pulling 30 amps of current from the supply during the load cycle, but after working with CP Automation we were only pulling 25 per cent of that.
“This saving meant we could install more GACs to match increased demand without needing to upgrade the mains power supply,” continues Evans.
Scaling-up
As Invertek Drives’ products grew larger, the company needed to scale-up its GACs while maintaining high energy efficiency. At this point, CP Automation worked with Invertek Drives to create a second, much larger, system with a capacity of 200 A and recommended installing REVCON harmonic filters on the GACs for when the Invertek Drives team was testing the drives.
“After working with CP Automation to install harmonic filters on the larger system, we saw improved quality and reliability of our internal testing,” says Brian Walker, senior GAC engineer at Invertek Drives. “The DC bus remained stable, the control side for loading was more consistent and the input phases were more balanced, all of which helped when we tested our drive products.”
“The design height of the GACs meant that space was an issue,” says John Mitchell, global sales and marketing director at CP Automation. “By installing two smaller harmonic filters in series we met Invertek Drives’ space constraint.
“The units also provided incremental improvements like reducing heat losses, improving phase angle and boosting the DC bus on the load drive, which all added up to improve efficiency,” continues Mitchell.
“The braking units boosted efficiency and the harmonic filters improved reliability,” adds Evans. “The production process is slicker and more streamlined and helped us manufacture an even more reliable product for our customers.”
The future
“The reliability of the systems has been great, one of the first units installed around ten years ago is still running now,” continued Evans. “One of the reasons we’ve kept working with CP Automation is because the technology is so reliable.
“The equipment CP Automation supplied worked really well on the small system, it worked well on the large, so now we’re going extra-large and working together on a third system that will go up to 450 A,” concludes Evans.
- Tips for mitigating harmful harmonics
- Active harmonic filters
- Detailed product info
- Active & passive harmonic
- Distributor recognised
- The race to replace
- Re SpA appoints CP Automation as sole UK distributor
- SME partnership promotes motor customisation
- Active and passive harmonic mitigation
- Not all inverters are created equal