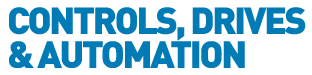
![]() |
Charlotte Stonestreet
Managing Editor |
Home> | POWER TRANSMISSION | >Pneumatics & Hydraulics | >Simplicity & efficiency with selection & assembly |
Simplicity & efficiency with selection & assembly
29 April 2015
The theme of this year’s Hannover Fair was Industry 4.0 and future production. Festo was leading the way with its Bionics displays addressing the challenges of the manufacturing world of the future. Steve Sands, product manager at Festo reports
Concepts for resolving important topics like functional integration, miniaturisation, flexible and adaptive systems, or how to operate machinery intuitively through de-centralised control concepts were visualised through bionic models including the BionicANTs and eMotionButterflies.
Cutting edge collaborative approaches for Industry 4.0 were demonstrated on a machine display showing the latest output from the German Government sponsored OPAK project. The project is exploring the future of the digital factory, from concept to visualisation, off-line modelling and programming to the realisation of a machine utilising intelligent modules operating in a highly de-centralised and yet collaborative way.
Pneumatic systems will remain a vital part of factories for the foreseeable future due to their speed, power and efficiency. Festo is responding to the demand for simplicity and efficiency with a new generation of standard VUVS new solenoid valves.
Versatile mounting
The key here is not so much the well proven function of the valves but the approach to make the selection, mounting and maintenance as quick and easy as possible. Highly versatile mounting options supplement the standard valve range, offering a higher degree of flexibility and reducing the need for costly and time consuming custom designed manifolds or brackets. Production costs have been reduced through highly automated production lines. Clever design ensures a wide range of functionality with high commonality of parts, increasing production part volumes and further decreasing costs.
The theme of efficiency continues with our new design tool (FDT3D) configuration software. This enables users to design cylinder assemblies combining the core actuator with matching mountings and accessories to produce a complete 3D CAD model that can be ordered as a single part number for the complete assembly or the bill of materials for self assembly.
The configuration software reduces the risk of errors when selecting, designing and ordering pneumatic actuator assemblies. Specifying system modules as a complete package, each with a unique product key, speeds-up and simplifies design, logistics and assembly operations. It allows users to select their required pneumatic drive easily and then automatically and correctly places the chosen accessories on the cylinder in accordance with their application.
Festo’s approach to addressing customers’ efficiency doesn’t end there. It also extends to electric drive systems where we have developed a new system for configuring ready-to-install handling systems in less than 20 minutes. The Handling Guide Online (HGO) significantly reduces design, assembly and delivery times, halving project times for a complete handling system.
Quick calculations
A system that is this easy to use enables accurate costs to be quickly calculated, a boon to special purpose machine designers who can be sure even at the concept stage of the price and performance of key, custom parts of their machine design. In the past, designers went through a lengthy or risky estimation process to calculate their handling systems. This unique online software makes ordering and configuring handling systems a quick and easy experience and the cost process cost savings we make are directly passed on to our customers.
To meet rising demand and drive down costs, Festo is fully committed to making use of the latest production concepts within our own factories. We are nearing completion of a highly automated production plant in southern Germany. At this site alone we have invested more than £110m in the development of state-of-the-art production facilities.
Our Technology Factory represents a significant step towards the production of the future. New concepts from Industry 4.0 are being applied and tested here. On completion of this facility, a wide range of our valves, valve manifolds and electronic components will be manufactured here demonstrating how through advanced automation, European manufacturing sites can remain competitive on the global stage.
Key Points
- Pneumatic systems will remain a vital part of factories for the foreseeable future due to their speed, power and efficiency
- Making selection, mounting and maintenance as quick and easy as possible is key
- Clever design ensures a wide range of functionality with high commonality of parts, increasing production part volumes and decreasing costs