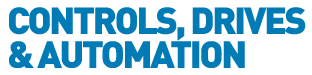
![]() |
Charlotte Stonestreet
Managing Editor |
Editor's Pick
Industrial transformation
23 January 2020
The growing pace of technological change, increasingly uncertain prospects for the global economy and political debate about trade relations and Brexit are putting the manufacturing industry under pressure. Rather than simply going with the flow, Festo aims to play an active role in this complex scenario
Taking a closer look at individual sectors of industry and markets, increasing volatility even within these ecosystems is apparent, for example in the automotive or electronics sector – and industry must find solutions that can flexibly deal with these fluctuations. Industry 4.0 initiated the fusion of state-of-the-art information technologies with the manufacture of machinery and production systems. Industry is now in the midst of an industrial transformation from large-scale series production to individually customisable products down to batch size one.
With its smart digital solutions, automation expert Festo is blending its comprehensive expertise in industrial applications with current developments in information technology, in order to realise software applications for industrial practice in automation. In digital communication, Festo accompanies its customers on the 'Digital Customer Journey', which securely and comprehensively leads them through the performance portfolio of Festo – from the acquisition of information and configuration, through ordering and delivery, up to commissioning and maintenance.
This is all now being supplemented by the skills and methods being made available by artificial intelligence (AI). For the first time, they are enabling data to be derived directly from machinery and industrial production systems by means of sensors, so the data can be evaluated in real time and thus add to the overall knowledge of dependencies and interactions in the manufacturing process. Thanks to digitalisation and AI, the complexity of these processes is becoming fully controllable.
AI is the key to the world of tomorrow
Festo is focusing on transferring its core competence of factory automation to the AI-supported, digitalised production of tomorrow. Today, algorithms analyse the data from machinery and provide forecasts of failures or prevent them from occurring. Tomorrow, algorithms will monitor, control, navigate, supervise and regulate value flows in a complex network. While they will not replace decisions by humans, they will support them in their decision-making.
The classic automation pyramid, with a linear connection between the production and corporate levels, is dissolving and is now orienting its structure towards networked, synchronised production. At the same time, digitalisation is generating virtual twins of machinery, systems and value flows. The great advantage here is that processes, parameterisations and configurations can be acted out in these computer-generated simulations without the need to intervene in existing production processes. Setting-up time and downtime are reduced. This saves costs and time – which is crucial for countries with a high labour content in manufacturing costs, so that they can remain competitive on the global market.
"High productivity due to full automation makes stockpiling of many spare parts necessary, for example, and gives rise to high personnel costs in preventive maintenance. AI, and here in particular machine learning with anomaly recognition, will help reduce these costs in future," says Dipl.-Ing. Dr. h.c. Oliver Jung, Chairman of the Management Board of Festo AG.
To generate added value and increase efficiency with the methods from the algorithmic toolbox, use cases must be precisely defined. Satisfactory results are only possible if the data are strategically prestructured and are available in sufficient quantity. “We have taken a close look at quality assurance with AI in a production process at our own factories and have come to the conclusion that the big data approach from the consumer market is not successful in industry. We only managed to significantly increase efficiency once we united the expertise of the machine operators with the appropriate statistical methods of AI," says Jung.
Festo is currently focusing above all on AI assessments “on edge”, in other words directly on the component, or on location within a production network. This saves costs, ensures real-time assessments and avoids latencies. Only intricate evaluations involving production locations distributed throughout the world need the large computer capacities of a connected Cloud infrastructure.
With the Festo IoT Gateway, existing production plants can be made AI-capable without major intervention. Algorithms and models can be updated directly on a device without modifying the PLC, independently of the computer capacity or the free resources of the PLC.
From mechanical to smart products
With the Festo Motion Terminal VTEM for example, Festo has already paved the way for digitalised pneumatics: the functions of the valve terminal can be controlled by app, so that different tasks can be carried out with the same hardware. In sectors of industry that manufacture products strongly oriented to individual customers’ wishes, such as kitchens, the potential degree of automation therefore rises.
So, what does this mean for people? As an innovation leader in factory and process automation, Festo always focuses on people in addition to technical solutions and sees the role of technical education and training as crucial both to technological innovation and to promotion of the labour market.
As early as the 1950s, Festo realised that new technologies can only develop their potential when people know how to deal with them, and as a result founded Festo Didactic SE. As a global partner to educational institutions, governments, state-run facilities and companies throughout the world, Festo Didactic SE establishes and maintains training centres and laboratories as well as integral learning solutions and training programmes that systematically prepare people for working in dynamic and complex environments.
“Vocational training is thus a key to a company’s competitiveness”, emphasises Oliver Jung. The workplace is therefore becoming a place of “lifelong learning”. Companies rely on constant learning on the part of their employees to maximise their productivity. Self-controlled learning, and learning in contexts of application, are also gaining significance. With digitalisation, the competence required in both existing and new professions will continue to change, and with it also the requirements on education and training.
Condition monitoring in the cloud
Detecting irregularities at an early stage and initiating the necessary measures before a system failure is now made possible by the dashboards and IoT gateway CPX-IOT from Festo. The turnkey, preconfigured dashboards do not need any additional programming or software. The collected data improves operating transparency for production managers and operators.
Further processing and long-term analysis of data takes place in the cloud. Festo dashboards visualise the information gathered. Festo thus supports machine builders and end users in several steps – through the visualisation and processing of data. The result is increased productivity through better utilisation (overall equipment effectiveness (OEE)), lower costs due to greater energy efficiency and fewer downtimes thanks to comprehensive diagnostics, condition monitoring and improved maintenance. System operators can compare the process control systems of their machines across several locations and identify potential for saving energy. The data can be called up at any time.
The IoT gateway CPX-IOT connects components and modules from the field level – such as the valve terminal CPX/MPA, the energy monitoring module MSE6-E2M or handling systems – to the Festo Cloud through the OPC UA interface. CPX-IOT collects information and data on Festo devices and their statuses through an Ethernet-based interface and a standardised communication protocol, such as OPC UA. It then sends that information to the cloud through the second Ethernet connection using IoT protocols. The preconfigured dashboard visualises the appropriate information and spares users tiresome programming work. Suitable IT security mechanisms ensure data security in the process.
Key Points
- Industry is in the midst of a transformation from large-scale series production to individually customisable products down to batch size one
- The classic automation pyramid is now orienting its structure towards networked, synchronised production
- Festo is focusing on transferring its core competence of factory automation to the AI-supported, digitalised production of tomorrow
- Superconductors & their potential for industrial automation
- Bio-inspired robots
- Electric drive tech achieves ideal Easter egg flavour combos
- Entering the next stage with artificial intelligence
- Networking made easy
- Packaging system concepts
- FREEBIRD - THE THIRD DIMENSION
- Smarter workers
- Festo Process Automation Mobile on tour
- Industry 4.0 comes out of its Shell
- No related articles listed