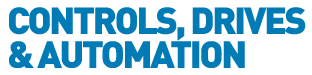
![]() |
Charlotte Stonestreet
Managing Editor |
E-vehicle revolution powers on
15 December 2021
Warren Harvard describes developments in automation technology that will improve production of Lithium-ion batteries
THE ECONOMIC and environmental drivers for change in mass transportation and energy generation and storage are placing increasing pressure on production of essential components. One example is the switch to Lithium-ion (Li-ion) battery technology.
In the UK, it is clear that if the domestic car assembly sector is to survive the transition from internal combustion engines to battery-driven electric vehicles (ELVs), the supply chain for batteries has to be secured, shortened and cost optimised. Research indicates that to comply with the Government's banning of internal combustion engine sales by 2030, and hybrids by 2035, the country will require up to 13 so-called Gigafactories by 2040.
This urgency to secure efficient and reliable battery production is not limited to the UK. Globally, battery manufacturers are seeking to reduce costs and increase batteries' lifetime, performance, and safety. Batteries are the highest single cost element in an electric vehicle and limit range and performance. Incremental improvements in all of these areas require faster machinery with higher productivity and delivering higher precision and flexibility.
Clearly, the speed of change to ELVs is creating both enormous pressure and opportunity for battery manufacturers. In turn this is driving industrial automation specialists to provide solutions that can help to meet the rapidly growing demand.
Combined effort
One example is the collaboration between Festo and Siemens to improve the performance of the Multi-Carrier System (MCS) to match battery production challenges.
The MCS modular transport system comprising linear motor tracks, customisable carriers, guide systems, conveyor tracks and sophisticated drives and controls. Housed within the track are the electric windings of the motor (stator), which generates a moving magnetic field that drives the motion of the permanent magnet plate(s) housed in the dynamic carriers. There is a direct relationship between the applied current, the magnetic field and the feed force applied to the carrier. Accelerations of up to 50m/s² and speeds of up to 4m/s are possible, making it a highly dynamic system.
The independent carriers are 'handed' from one linear motor track section to another. They can also seamlessly transit onto a traditional conveyor transport system, enabling the linear motor track to be used only where needed. The high dynamics of linear motors offer smooth accelerations, high speeds and precise positioning.Traditional conveyor systems cost considerably less per metre, and provide features such as recirculating carrier loops, buffer stations, intricately curved sections, diverter/handover loops etc. The combination creates a highly flexible, dynamic and alterable solution.
Initial applications for the MCS system have been centred around high-end packaging and printing applications, enabling high speed, flexible packaging utilising the system's dynamics to handle products whether they are bottles, tubes, boxes or pouches. MCS systems are typically used to manage the transition from continuous flow processes, collating variable numbers of carriers and synchronising their motion with stations such as filling heads, insert, cap or seal.
These capabilities are highly transferable to volume battery production. Applications for the MCS span the entire assembly process – from handling active material foils to cell stacking, from packaging through to complete cell arrangements and module handling.
Positive outcomes
Festo and Siemens have therefore worked together to increase the applications range and performance of the MCS so that battery manufacturers can derive optimum benefits from its implementation.
Higher speeds are now possible because the motor track performance has been increased by up to 30% by replacing the fan-driven air cooling with a liquid cooling option. This enables more power to be wrung from the servo motors without affecting life expectancy. This is complemented by an increased feed force, resulting from a greater number of high energy Neodymium magnets (NdFeB) installed on the underside of the carriers. Clamping or holding components on the carrier was another challenge. The team has created custom carriers with onboard solutions for both vacuum and pressure-driven air clamps.
Precision improvements have been achieved by replacing the standard Hall effect encoders with optical encoders, lifting the resolution from ±.01mm to ±25µm. The improved MCS also features Individual RFID carrier identification and data transfer for complete traceability.
Improved flexibility has resulted from expanding the range of track lengths (now 51, 102, 204 and 306mm). There is also a wider choice of conveyor tracks, bearing systems and carrier widths. The open, modular MCS system is designed to offer a seamless handover of carriers to and from leading conveyor manufacturers' systems, including Elcom (TLF 1500, TLM 2000), Flexlink (X85P, XH), and Bosch (TS 2plus).
Guide systems for carrier masses ranging from under 1kg to over 50kg can be accommodated. Where the application requires very wide carriers and higher feed forces, twin-track systems can be selected, mechanically aligned and synchronised through the control system.
Optimised delivery
Movements of individual carriers on the MCS motor section are entirely flexible. To enable fully optimised battery production, the MCS features kinematic controls that aid rapid reconfiguration and integration with other equipment. The SIMATIC motion control system from Siemens can control other servo drives in the system, such as synchronising external conveyor drives or providing advanced camming functionality. It can handle the carriers individually or as groups, flexibly grouping and regrouping them as required.
The Siemens SINAMICS S120 modular system with additional RAILCTRL Technology Extension manages the transition between encoders and MCS track sections. There is a free choice between several SIMATIC hardware and software solutions using Step7 Professional in the TIA Portal at the controller level. Drag and drop programming speeds up the task, and it is possible to visualise every carrier as a separate technology object within the TIA portal.
A powerful toolkit of software tools makes the programming of such a flexible system more straightforward. SIMIT, NX MCD (Mechatronic Concept Designer), S7-PLCSIM Advanced and the MCS VC Toolbox enable the generation of complete digital twins for each section, quickly and easily. Complete MSC systems can be simulated and thoroughly assessed before cutting any metal. Only after testing on the virtual model is the program transferred to the live system. Considering the global nature of many applications, this also enables later modifications to be simulated and tested before committing to flights and line stoppages.
The specialist MCS applications team can support each battery manufacturer through the engineering process from feasibility to commissioning and after-sales support. Some customers prefer to handle the whole process, taking the parts and managing the integration themselves. Most choose to partner with Festo and Siemens in adapting the modular system to meet their particular needs.
The improvements made to the Multi-Carrier System by Festo and Siemens can make a real contribution to achieving the increased speed, precision and flexibility that will help deliver more advanced battery solutions. It is an exciting time to see the technology developing so quickly and in support of such a pressing imperative to improve the availability and competitiveness of alternative transport and energy sources.
Warren Harvard is product marketing manager, electric automation sales at Festo UK & Ireland
Key Points
- Networking made easy
- Air Flow & Pressure Switching Point Adjustment
- Engineering the path to sustainability
- Compact and precise electric parallel gripper
- Re-breather function
- Flow & pressure sensors with IO-Link
- Fast & reliable configuration of process valves
- Swimming robot inspired by nature
- Flexible counting capability
- Save costs when selecting process valve solutions