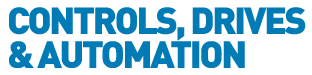
![]() |
Charlotte Stonestreet
Managing Editor |
Home> | POWER TRANSMISSION | >Actuators | >Magnify ROI on pneumatic cylinders |
Home> | POWER TRANSMISSION | >Pneumatics & Hydraulics | >Magnify ROI on pneumatic cylinders |
Magnify ROI on pneumatic cylinders
17 November 2015
Franck Roussillon, product manager for actuators at Parker Hannifin, has some best practice advice on how engineers and specifiers can convert necessary outlays into returned investments
As the range of pneumatic cylinders available on the market today becomes more extensive and sophisticated, it can be challenging to ensure you’re maximising the ROI available from your application.
One of the first recommendations that can help magnify ROI is to avoid side-load mounting. Cylinders are designed to deliver push-pull stroke action, so side-load mounting can result in a number of performance problems, including misalignment, off-centre loads, rod deflections, imprecise tie-rod torque or long stroke action. Upon installation, the cylinder piston rod should be aligned with the mating machine component and then inspected in both the extended and retracted positions. Improper alignment can lead to excessive rod gland and cylinder bore wear, resulting in a shortened lifespan for the cylinder and lower productivity.
Prevent contamination
Also, consider how contamination can be prevented as this will further maximise the life of the cylinder. Particulates, pipe rust, scale and thread sealant debris can all curtail the life of the seal and plug openings, and damage surface finishes. So until the system is fitted with piping, keep the port plugs supplied with the cylinder in place and be sure to clean the piping thoroughly before making connections.
Moisture is another key factor to consider when trying to stop contamination, as when moisture collects in components in all compressed air systems it blocks the outlet flow-through. This can be potentially damaging to the performance of the cylinder as it can lead to diluted pre-lubrication grease, contaminated airline lubricants, a damaged barrel or rod finish, and the potential to freeze in cold weather.
To avoid this happening, consider using stainless steel cylinders, which feature a smooth, hygienic exterior design to prevent contamination. These are particularly useful for food industry applications as cleanliness is assured via the use of stainless steel piston rods, cylinder tube and end covers.
It is also important to pay close attention to both the wiper seals specified and the cushioning that is needed. The end application drives the selection of wiper seals. For example, applications that are extremely dusty or feature very high operating temperatures will require appropriate seals to match the installed environment. Poor selection of seals can cause degradation, leading to the ingress of particles and dirt, which ultimately risks cylinder failure.
Optimal cushioning
Cushioning is required to decelerate a cylinders piston before it strikes the end plate. Reducing the piston velocity lowers the stress on cylinder components, increasing the usable lifespan and ROI. Whilst cylinders that feature automatic adjustment exist, a best practice recommendation is to use manual variants to achieve optimal cushioning, as you are able to match the weight of the work piece to the dynamics of the movement. This method has been found to be much more accurate and efficient.
A final consideration when thinking about preventing contamination is to watch out for oils that result from air compressor lubrication carryover or synthetic oils which are typically incompatible with air-line components. Such oils can swell the seal and plug openings. Instead, consider using oil-compatible seals.
It’s well documented that cylinders operating at high or fast cycle rates will typically generate significant shock loads at end of stroke. Furthermore, the heat generated by the system can exceed the component’s temperature limits and affect the lubrication. With this in mind, consider selecting a pre-lubricated or air-cushioned cylinder. Other options include adding a shock absorber or lowering system pressure via a regulator on the return (non-working) side of the cycle. Finally, adding flow control to the cylinder can also help, as long as high speed is not required.
Key Points
- Side-load mounting can result in performance problems including misalignment, off-centre loads, rod deflections and imprecise tie-rod torque
- Particulates, pipe rust, scale and thread sealant debris can all curtail the life of the seal and plug openings, and damage surface finishes
- When moisture collects in components it blocks the outlet flow-through, potentially damaging to the performance of the cylinder