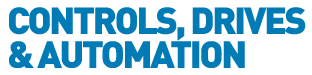
![]() |
Charlotte Stonestreet
Managing Editor |
Renewables - are investment plans just hot air?
22 October 2015
How much needs to be spent on renewable energy projects each year in order to enable the rapid transition to a clean energy economy? Andy Pye looks at the issues
Spending on renewable energy projects in 2014 gives a good clue to the answer. According to a study by the UN and Bloomberg New Energy Finance, public and private investors spent approximately $270 billion on renewable energy projects in 2014. According to the study, this spending only increased renewable energy’s share of global generation by about 0.6 percent.
This rate of spending needs to be doubled by 2020 and quadrupled by 2030 if we are successfully to keep carbon dioxide levels in the atmosphere below the 450 parts-per-million (PPM) level that many scientists believe would keep temperature increases resulting from greenhouse gas emissions below 2 degrees Celsius. We cannot transition to a clean energy economy without generating extremely large investments in renewables.
The UK renewable energy sector continues to grow with £5.2 billion worth of contracts in 2014, which includes a record amount of solar power projects worth over £1.7 billion. But whilst the renewable sector did benefit from high levels of investment in 2014, 45 per cent (409 projects) of renewable wind projects submitted for detail planning were refused at the planning stage, considerably higher than the average refusal rate of 12 per cent across the construction sector.
Cuts to UK renewable energy subsidies are sending a worrying signal to investors. At the very least, say industry analysts, barriers to the deployment of renewable energy must be removed.
According to researchers at Chalmers University of Technology, after conducting several years of research into carbon-intensive industry in Europe, the targets for lower emissions of carbon dioxide from Europe's basic industries are out of reach, without urgent introduction of innovative carbon dioxide mitigation technologies.
"There is an urgent need to demonstrate and implement carbon capture and storage, CCS, and other carbon dioxide mitigation technologies," says Johan Rootzén, who recently presented his doctoral thesis. "While this will involve major investments in primary production, our results suggest that there will only be marginal impacts on costs and prices in the end-use sectors.”
"The clock is ticking," says Rootzén. "Plants have very long lifespans, so implementation of new technology takes a long time. If the EU is serious about reducing emissions by 80-90 percent by 2050, then the issue of how to finance the development and implementation of innovative process technology must be brought to the table now.”
Wind turbine design
As the size of wind turbines increases, the design of blades, control systems, and supporting structures becomes more complex. New designs need to be quickly tested for fatigue and twisting under expected operating conditions.
It is not economical or practical to build and test many (if any) physical prototypes. Virtual testing of blade components reduces the need for expensive prototypes and minimises development time and cost. Finite element analysis is conducted, along with virtual and physical wind tunnel testing. Tests in virtual operating situations on foundations and the entire fabrication are performed.
StrucTeam is a UK engineering services company for advanced composite structures. Technical Director Radek Michalik, described some of the complexities of designing with carbon fibre and advanced composite materials, as opposed to designing with light alloys such as aluminium. "At present, there are few standards for designing composite materials. This is because they are relatively new and, unlike metals, their physical properties can vary almost infinitely. We need to optimise three interdependent and often contradictory requirements - design, engineering and production - in order to simplify and improve the development process.”

StrucTeam uses Dassault Systemes’ 3DExperience Platform. Designs of composite blades are optimised by varying the number, direction and rotation of the carbon fibre layers with their characteristic ply, warp and weft. This reduces weight and introduces strength where it is needed with extra layers or application-specific designs. Software calculations - of vibrations, nonlinear deformation and stress, fracture and failure, and other multiphysics effects, including fluid-structure interactions and hail storms - can greatly improve turbine performance and reliability. These measures reduce the risk of catastrophic in-field failure, while simultaneously making blades less expensive to manufacture, due to less material being used.

"The material’s almost limitless possibilities of the fibre type, weave pattern, resin composition and final design can lead to errors if not fully understood. We can visualise and tailor laminate patterns to add strength and/or stiffness to finished products, at the digital visualisation stage," says Michalik.
Silent flights
A newly-designed material, which mimics the wing structure of owls, could help make wind turbines, computer fans and other types of fan blades much quieter. Early wind tunnel tests of the coating have shown a substantial reduction in noise without any noticeable effect on aerodynamics.
Since wind turbines are heavily braked in order to minimise noise, the addition of this new surface would mean that they could be run at much higher speeds – producing more energy while making less noise. For an average-sized wind farm, this could mean several additional megawatts of electricity.
The surface has been developed by researchers at the University of Cambridge, in collaboration with researchers at three institutions in the USA. Professor Nigel Peake of Cambridge’s Department of Applied Mathematics and Theoretical Physics has used high resolution microscopy to examine owl feathers in fine detail. It was observed that the flight feathers on an owl’s wing have a downy covering, which resembles a forest canopy when viewed from above. In addition to this fluffy canopy, owl wings also have a flexible comb of evenly-spaced bristles along their leading edge, and a porous and elastic fringe on the trailing edge.

"No other bird has this sort of intricate wing structure,” says Peake. "Much of the noise caused by a wing originates at the trailing edge where the air passing over the wing surface is turbulent. The structure of an owl’s wing serves to reduce noise by smoothing the passage of air as it passes over the wing – scattering the sound so their prey can’t hear them coming.”
In order to replicate the structure, the researchers then developed a prototype material made of 3D-printed plastic and tested it on a full-sized segment of a wind turbine blade. In wind tunnel tests, the treatment reduced the noise generated by a wind turbine blade by 10dB, without any appreciable impact on aerodynamics. The next step is to test the coating on a functioning wind turbine.
Solar
ABB has launched a high power 1500VDC solar inverter for multi-megawatt PV plants. Overall system costs are driven down by the increased DC input voltage up to 1500VDC and a high high power rating of up to 2000kVA.
One of the key features is its self-contained cooling system. Based on development from the ABB ACS800-38 low-harmonic drive’s innovative cooling system, the PVS980 uses phase transition and thermosiphon technology to avoid external air entering the critical compartments of the inverter. Given its IP65 rating, the high efficiency inverter can operate from below freezing to extreme heat in 100% humidity without jeopardizing functionality.
These components withstand the harshest environments, due to the simplicity of air cooling and with the power density of a liquid cooled inverter, there is low maintenance, as there are no fillable liquids, pumps, valves or inhibitors and, hence, no leaks.
The product also includes the standard grid support features of PVS series inverters - active and reactive power control, including night reactive power support. It supports a wide range of local utility requirements through adjustable grid support features.
ABB's new UNO solar inverter is a single-phase string inverter family, which includes four new models for residential applications. These transformer-less string inverters are targeted at the residential market and address the entry-level segment bringing additional value in terms of return-on-investment, ease-of-installation, reliability and enhanced communication via the newly released wireless card, VSN300.The new VAL-MB product family from Phoenix Contact provides powerful and compact protective devices for photovoltaic applications with generator voltages of up to 1500VDC. The protective devices are specially adapted to DC application requirements and certified by KEMA.

Longer inlet funnels and higher screw shafts provide additional protection against arcing. The product range includes protective devices for generator voltages of 600, 1000 and 1500 VDC, as type-1/2 lightning current arresters, as well as pure type 2 surge protection devices. Variants are available with or without remote signalling contact. All protective devices have a short-circuit protection of 2000A and can also be used in high-altitude plants up to 6000m in altitude.
Anaerobic digestion
Maximising the benefits of renewable energy continues to be the focus for an increasingly diverse range of companies continuing to invest in anaerobic digestion (AD). A new bio-energy plant at the Glendullan distillery is a good example.
Mixing is an essential part of the AD process and System Mix, which markets the Rotamix Dual Zone Mixing System, has supplied mixing equipment to both the Dailuaine and Glendullan distilleries. The mixing system installed at the Dailuaine Bioplant consists of a single Vaughan HE10R12-381 horizontal end suction chopper pump driven by a 37kW rated motor and four internally floor-mounted double nozzle assemblies to mix a 24.5m diameter digester tank. The success of this initial AD project was an important factor in the decision to upgrade the Bioplant at the Glendullan distillery, where another single pump mixing system is operating successfully.

Production residues such as spent grains and pot ale form the bulk of the materials which are fed into the bioplants which ultimately produce outputs of bio-gas of up to 500kWe CHP and are used to power the distilleries.
Waste water treatment
The European project DEMOSOFC coordinated by Politecnico di Torino will focus on the installation in the SMAT plant of Collegno of the first European industrial fuel cell system able to convert the sludge from the wastewater treatment process in clean and valuable energy, thanks to the high efficiency conversion of solid oxide fuel cells. As such this is the first industrial size plant in Europe able to produce high efficiency energy with solid oxide fuel cells (SOFC) using biogas from waste water treatment.
Three fuel cell modules are able to co-produce 175kW of electrical power and 90kW of thermal power. The system will be installed in the SMAT Collegno waste water treatment plant (Turin), where currently biogas is produced from anaerobic digestion of sewage sludge. The DEMOSOFC plant will cover around 30% of the site’s electrical needs and 100% of the thermal requirement.

The plant will employ the Solid Oxide Fuel Cell (SOFC) technology that can use directly natural gas or biogas. SOFCs are said to be the most efficient and fuel flexible devices among the different fuel cell types available.
Biogas – a renewable fuel – is first cleaned (sulphur contaminants are removed) and then sent to the fuel cell where high efficiency electrical energy is produced (with an electrical efficiency up to 50%, while traditional competitors like engines and turbines reach only 35-38 %). The system is also cogenerative since the heat recovery from the exhaust gases is also performed.
Key Points
- StrucTeam uses Dassault Systemes’ 3DExperience Platform for virtual testing of blade components, reducing the need for expensive prototypes
- A newly-designed material, which mimics the wing structure of owls, could help make wind turbines much quieter
- First industrial size plant in Europe able to produce high efficiency energy with solid oxide fuel cells (SOFC) using biogas from waste water treatment
- EEF survey shows slow Industry 4.0 progress
- The Rules of State
- Can ultra-capacity polymer supercapacitors displace auto batteries?
- Intensive care
- Technology too hot to handle?
- Sleepwalking
- Big data daunts the manufacturing sector
- The road to digitalisation
- SMEs urged to harness Industry 4.0 - or risk falling behind
- Appetite for connection
- No related articles listed