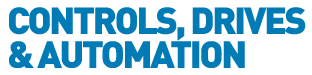
![]() |
Charlotte Stonestreet
Managing Editor |
Home> | INDUSTRY FOCUSES | >Food & Beverage | >Appetite for connection |
Appetite for connection
03 September 2019
The benefits to food and beverage producers of incorporating connected technology into their processes are well documented. And after a slow start, the food industry is catching up fast when it comes to applying automated systems, as Andy Pye reports
Smart technology can help organisations to make informed decisions that can turn a business into a predictor rather than a reactor. But digital fear is still prevalent in the food industry, particularly among SMEs. Indeed, as more food processing equipment gains coveted Industry 4.0 status, so the threat of data breaches grows.
The threat of a cybersecurity breach is ever-present in today’s connected world and food manufacturers of any size would be naïve to think their company is not at risk. Fortunately, there are steps that companies can take to protect their connected devices from hackers and other unwanted interference.
The most important line of defence is to keep networks separate. This could involve setting up a corporate network, for areas such as finance and HR functions, and an industrial network, which governs the operational side of the business that keeps the factory running.
To protect against unwanted threats either to the corporate network (such as accessing confidential personal or financial records) or to the industrial network (such as changing recipe mixes or overriding smart freezer temperatures), it is advisable that food producers apply the principal of least privilege.
“This means never giving a user more access than they need to perform their task,” explained Phil Brown, Managing Director of metal detection company Fortress. One way to do this is to create a third network. Known as a demilitarized zone (DMZ), this third network acts as a secure path between an organisation’s internal networks and the external network, while protecting the internal networks from outside interference. By only opening the particular ports needed to communicate on one network at a time, it ring-fences the rest of an organisation’s data and operational controls and alleviates much of the risk.
Fortress has responded by developing remote management technology, which allows multi-site food production plants to manage operations from anywhere in the world using smart phones, tablets and laptops.
An unlimited number of Fortress metal detectors can be connected wirelessly using a powerful back-end SQL to monitor activity and generate reports.
Despite fears of cybersecurity breaches, the risks of using paper records can actually be higher than digital data. Not only can manually collated information be incorrectly recorded, forgotten or lost, results can also be deliberately falsified. If a food producer cannot prove when and where inspection of their products took place, they may then be unable to demonstrate HACCP compliance and could be forced to re-inspect an entire batch.
Food sorting machinery
Bühler UK has won a Queen’s Award for Enterprise for its pioneering research into the camera technology used in its food sorting machines. The technological breakthrough is being used to drive up food safety controls in the nut and frozen vegetable sectors while also helping to increase plastic recycling rates.
Bühler’s cameras can recognise subtle colour and shading contrasts in materials and foods, which increases detection rates for foreign materials, potential choke hazards or contaminated foods. So-called hyperspectral imaging records vast amounts of wavelength data to generate highly accurate colour and shading contrasts for specific products. This data is then statistically analysed to create algorithms that inform the sorting camera exactly what colour and shading contrasts to look for when detecting contamination or a foreign object in a production process.
“The innovation here is our ability to gather such large amounts of data and then use that data to optimise a conventional narrow band digital camera so that it is capable of quickly and efficiently detecting very specific things, whether it be shells in nuts, foreign materials in a vegetable production line or even different grades of polymers in a recycling plant,” explains Senior Research Engineer Benedict Deefholts.
Bühler uses this technology to produce a range of specialist cameras for different markets, including peanuts, frozen vegetables and plastic recycling.
The Sortex range can efficiently remove defects with certain discolorations, in-shell, split, over/undersized or misshapen nuts as well as foreign material, including sticks and bone. Since the introduction of the Sortex E optical sorter, sales of Bühler sorting machines into the nut sector have doubled. Now, the most recent model, the Sortex F, is renowned for its stainless steel hygienic design. It offers a 4-in-1 detection, targeting colour, nut shells, shape and foreign material in all nut varieties (peanuts, cashews, hazelnuts, walnuts), whether in-shell nuts, natural, blanched or chopped.
Tricky sensing
Bottles and cans on food production lines present some challenges for sensors. Turck Banner's Q5X sensor reliably detects extremely dark targets, black targets against a black background, black targets against a shiny metal background, clear and reflective objects, multicolour packaging, and targets of all colours. In addition, it features stable detection to 2m - even at an angle — which enables greater mounting flexibility. The sensor is rated IP67 for reliable performance in wet environments.
When bottles are removed from a depalletiser, the bottles are swept from the pallet, layer by layer, by a sweeper arm. The bottles eventually start to move into a single file and continue downstream. It is important to monitor the bottles in the staging area to make sure that they have moved on before another layer is swept onto the conveyor. However, the unstable signal from the moving bottles and low contrast objects, can be challenging for sensors to detect reliably.
The Q5X background suppression feature detects when the staging area is clear of bottles, and the system is ready for the next layer of containers. The integral timing delay on the Q5X filters out any small gaps between objects as they move in a cluster. Background suppression is also important because the sensor can be set to only detect objects within a defined sensing field and ignore anything that is located beyond the sensing field cut-off point.
In dual teach mode — which measures both distance and light intensity — the Q5X can reliably detect the presence of clear bottles without the risk of double counting.
Natural light is made up of waves having a variety of polarizations. Photoelectric sensors with polarizing filters emit and detect only light waves of a specific polarization while rejecting unwanted light of other polarizations.
When unfinished cans pass between the sensor and the retroreflector, the light reflected off the cans has a different polarization than the light returned by the retroreflector. As a result, the beam will be blocked by the cans and the output will be triggered.
Turck Banner's Q20 Polarized Retroreflective Sensor is designed to detect only the light returned from the reflector, ignoring light returned from shiny objects. Shiny objects can act as reflectors themselves, returning enough light to the sensor to cause unreliable sensing. A solution is needed that will only see the light returned from the retroreflector, and not light returned from shiny targets.
Whisky galore
Muntons, one of the UK’s largest producers of malted barley, is protecting vital parts of its production process against unscheduled downtime by using the Smart Condition Monitoring (SCM) system from Mitsubishi Electric.
Used to make beer, spirits and a range of popular foodstuffs, malted barley is produced in large batches where environmental conditions are critical to a consistent product.
As in many food industries, the principles of the barley malting process are quite traditional, but Muntons relies heavily on automation, electro-mechanical equipment and sensors to provide fine control over air flow, heat and moisture. Fans and motors are critical: Muntons processes many tonnes of product at a time, with key operations relying on a steady supply of blown air. The chosen SCM installation provides condition monitoring for two large 315kW fan sets and a single 90kW fan set. Sensors monitor the electric motor, power transmission coupling and main fan shaft bearing on each fan set.
Plant Engineer Michael Plawecki says: “We now have a clear picture of the health of the fan sets and advance warning of any required maintenance. Remote monitoring and fast diagnosis of any issues has also made us very responsive should the limits on operating parameters that we have set be approached. As promised the system was easy to install and relatively simple to commission.”
The impetus for the SCM installation came from issues previously experienced with difficult-to-reach bearings inside a large fan housing. A bearing failure inside a fan assembly caught the Muntons engineering team unawares and proved significant in terms of downtime. “We only realised we had problems when it was too late, and we had to make an unscheduled stop on one of the lines to make repairs,” says Plawecki.
Determined to learn from that lesson, Muntons looked for a monitoring solution with predictive maintenance technology that could be linked into the company’s existing SCADA system. SCM comprises smart sensors that can be attached to bearing housings, gearboxes, pumps and motors to detect when equipment starts to operate outside its normal envelope due to wear. It provides a sophisticated early warning system for critical pieces of rotating plant equipment. Vibration frequencies and temperature readouts are monitored continuously and fed back to an L Series Mitsubishi Electric PLC via an industrial Ethernet network cable.
The sensors, developed by bearing expert FAG, monitor changes in complex vibration patterns specific to the type of equipment it is attached to. The software compares that data with highly developed data models from thousands of previous installations, providing an effective analysis and alert system for the user.
Mechanical harvesting of lettuce
Crops such as potatoes and wheat have been harvested mechanically at scale for decades, but many other crops have to date resisted automation. The iceberg lettuce is one such crop. Although it is the most common type of lettuce grown in the UK, iceberg is easily damaged and grows relatively flat to the ground, presenting a challenge for robotic harvesters.
The Vegebot, a vegetable-picking robot that uses machine learning to identify and harvest a commonplace, but challenging, agricultural crop has been developed by a team at the University of Cambridge. It was initially trained to recognise and harvest iceberg lettuce in a lab setting. It has now been successfully tested in a variety of field conditions in cooperation with G’s Growers, a local fruit and vegetable co-operative.
Although the prototype is nowhere near as fast or efficient as a human worker, it demonstrates how the use of robotics in agriculture might be expanded, even for crops like iceberg lettuce which are particularly challenging to harvest mechanically.
“At the moment, harvesting is the only part of the lettuce life cycle that is done manually, and it’s very physically demanding,” said Julia Cai, who worked on the computer vision components of the Vegebot while she was an undergraduate student.
The Vegebot first identifies the ‘target’ crop within its field of vision, then determines whether a particular lettuce is healthy and ready to be harvested, and finally cuts the lettuce from the rest of the plant without crushing it so that it is ‘supermarket ready’. “For a human, the entire process takes a couple of seconds, but it’s a really challenging problem for a robot,” said coresearcher Josie Hughes.
“Every field is different, every lettuce is different,” said Simon Birrell from Cambridge’s Department of Engineering. “But if we can make a robotic harvester work with iceberg lettuce, we could also make it work with many other crops.”
The Vegebot has two main components: a computer vision system and a cutting system. The overhead camera on the Vegebot takes an image of the lettuce field and first identifies all the lettuces in the image, and then for each lettuce, classifies whether it should be harvested or not. A lettuce might be rejected because it’s not yet mature, or it might have a disease that could spread to other lettuces in the harvest.
The researchers developed and trained a machine learning algorithm on example images of lettuces. Once the Vegebot could recognise healthy lettuces in the lab, it was then trained in the field, in a variety of weather conditions, on thousands of real lettuces.
A second camera on the Vegebot is positioned near the cutting blade, and helps ensure a smooth cut. The researchers were also able to adjust the pressure in the robot’s gripping arm so that it held the lettuce firmly enough not to drop it, but not so firm as to crush it. The force of the grip can be adjusted for other crops.
Key Points
- Fortress' remote management technology enables management of multi-site food production plants from anywhere in the world
- Bühler’s cameras recognise subtle colour and shading contrasts in materials and foods, increasing detection rates for foreign materials
- Turck Banner's Q20 Polarized Retroreflective Sensor is designed to detect only the light returned from the reflector
- DEEPER INTEGRATION IN THE FOOD INDUSTRY
- Offering benefits to the food & beverage industry
- Reliable Feeding
- Food & beverage sector benefits
- High hygiene
- Extra reach for high speed applications
- Cut the cost of bearing downtime
- The value of continuous development
- Keeping the milk flowing
- Food handling robots