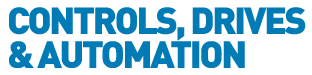
![]() |
Charlotte Stonestreet
Managing Editor |
Still got the power
14 January 2016
Close knowledge of power transmission products and their capabilities can help production and maintenance engineers improve uptime and cut long-term operating costs, says Phil Burge, country communication manager at SKF
Power transmission products such as belts, pulleys and couplings have long been a mainstay of the manufacturing sector. Their performance – which has a significant effect on the efficiency and reliability of production systems – can be affected by everything from their initial design and selection, right through to the way they are installed and maintained.
As an example, drive belts that are just a few degrees out of alignment will wear irregularly – reducing operating life and increasing energy consumption. At the same time, low-cost chains and sprockets may save cost initially but will lead to far higher repair and maintenance costs when they inevitably fail prematurely – especially if they have been incorrectly specified.
In answer to the question ‘How do I get more from my power transmission system?’ it is tempting just to say: ‘Spend more.’ However, things are not that straightforward, because simply spending more is not a guarantee of success. Instead, by understanding their power transmission systems more deeply – and following some general rules – maintenance and production engineers can improve uptime while cutting long-term operating costs.
Coupling importance
Couplings are available in a sometimes bewildering array of variants – including grid, gear, flex, chain and jaw couplings. Each has its own niche, and is appropriate for different applications, and design modifications are helping to extend their applicability.
As an example, SKF recently launched a range of disc couplings that enhance performance in medium to high torque applications that require torsional rigidity. They have a capacity range up to 178kNm in a variety of configurations, including single disc, double disc and spacer for both horizontal and vertical mounting.
The couplings have two hubs and a laminated stainless steel disc pack secured by a series of fitted bolts retained by nylon insert lock nuts. They cut the need for maintenance because they allow for slight misalignment – and do not require lubrication. Single disc couplings accommodate angular offset, while double disc pack units with a spacer will allow for angular, parallel or combined offset. The disc pack, or spacer, can be removed and re-installed radially, so the prime mover and driven machine need not be moved at all.
Belting ideas
Drive belts and chains are commonly used power transmission products, whose performance can be boosted through careful design and commissioning.
Online calculation tools, such as those offered by SKF, help system designers to optimise both belt and chain designs. The program selects the most efficient combination of products for a particular power transmission application. Users begin by choosing either single or multiple solution calculations. The single solution calculation is usually used to check existing belt drives; for multiple solutions, users can select belts by themselves, or choose from a range of possibilities.
After filling in basic application data, such as power and drive conditions, speeds, maximum pulley diameters and shaft diameters, the system provides a list of recommended solutions – including a full report that can be saved and printed. The solutions can be ranked by weight or price index.
Once designed and commissioned, belts (and chains) must be properly installed – which means setting the correct alignment and tension. Belt tensioning and alignment can easily be set using instrumentation: laser alignment devices can identify problems such as angular misalignment, while belt tension can be checked and adjusted using an electronic tension meter.
Despite this easy fix – and the fact that some belts can correct for small amounts of misalignment – these problems are common reasons for underperformance.
Improper alignment can lead to noise and vibration, and excess wear on the belt. It also drags down the energy efficiency of the whole system. Correct belt tension is vital for system efficiency. If it is too high, the belt is over-stretched and will fail prematurely. If set too low, it can slip – which leads to failure through excess temperature.
Before installing either a V-belt or synchronous belt, pulleys should be properly aligned – otherwise problems such as edge wear will occur. For V-belts, all pulley grooves should be the same size. Mixing different brands or belt types on the same drive is not recommended, and nor is the combination of old and new belts – as this may result in uneven load distribution.
For a synchronous belt, pulleys and alignment should be inspected before installing the new belt over the pulleys. The maximum allowable misalignment is 1/3 degree (any higher and there is likely to be tooth wear and reduced belt life). For either type of belt, pulleys should be checked every time a new belt is installed – and should be closely inspected (and possibly changed) on every third belt change.
Milk savings
Keeping on top of misalignment can be very financially rewarding. Fonterra Te Rapa, a multinational dairy company, recently saved more than £400,000 over the course of a year – after SKF identified and fixed misalignment problems on one of its milk powder lines. Fonterra had found that the drive belts on the line were lasting no more than five weeks. Belt failures had caused two costly shutdowns, costing more than £50,000 per hour in lost production.
SKF inspected the failed belts and saw that running temperatures of around 60 degree Celsius had led the rubber to cure and harden, causing the belts to crack and break. The belt tension was also set far too high and the motor was incorrectly aligned – which had caused the high temperature.
The answer was a system redesign, for which SKF trialled two solutions: the first used SKF Xtra Power Belts, while the second used SKF 8M timing belt drives. These were run against a ‘control’ using the original belts. After 28 days, the two SKF systems were working within the specified tension – and running at temperatures about 10 degree Celsius lower – while the control set had hardened and cracked as before. As well as banishing downtime, the new system also led to extra energy savings due to the belt drives running more efficiently.
Looking for trouble
In this case, expert help from SKF helped the customer to solve the problem. However, customers can solve their own problems using troubleshooting guides – which are available for both types of belt, for example.
In each case, the root cause can lead to a very different symptom. Misalignment, for instance – whether of the drive or pulley – can lead to mismatching, make belts turn over, or cause rapid wear in V-belts. In synchronous belts, the same problem can cause excessive edge or tooth wear, high drive noise or excessive tracking.
These symptoms, in turn, suggest solutions: a synchronous belt with excessive wear – due to a misaligned drive – can be solved by checking pulley alignment; if the wear is down to a bent or rough flange, the pulley needs repairing or replacing. A similar approach is used for V-belts. If they are wearing rapidly, there are several possible causes: excessive starting torque, or an overloaded drive (in which case the drive needs to be redesigned); poor pulley alignment (meaning the drive must be realigned); or, in the case of excessive pulley groove wear, new or reworked grooves are needed.
Similar step-by-step troubleshooting steps are available for just about every problem encountered in a belt drive, helping maintenance staff to identify and solve problems quickly.
Key Points
- By understanding power transmission systems more deeply maintenance and production engineers can improve uptime and cut operating costs
- Drive belts and chain performance can be boosted through careful design and commissioning, with correct alignment and tension
- Correct belt tension is vital for system efficiency; if it is too high, the belt is over-stretched and will fail prematurely; if set too low, it can slip
- When is a hybrid bearing the best choice?
- Bearings for pump & compressor applications
- SKF seizes counterfeit bearings
- When the going gets tough
- Condition monitoring to prevent bearing damage
- Super-precision series
- Tool up & team up for digitalisation
- SKF Commences Civil Action Over Counterfeit Bearings
- SKF power transmission products help simplify the supply chain
- Affordable machine health monitoring
- No related articles listed