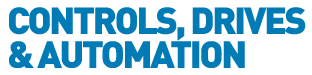
![]() |
Charlotte Stonestreet
Managing Editor |
Home> | POWER TRANSMISSION | >BearingsĀ | >When is a hybrid bearing the best choice? |
Editor's Pick
When is a hybrid bearing the best choice?
20 April 2020
How can you tell in advance whether a hybrid bearing will outperform a steel one in your application and whether its extra cost can be justified? This difficult, recurring question can now be answered by a newly developed bearing life model, as Guillermo Morales-Espejel explains
The use of hybrid bearings, combining ceramic rolling elements with steel raceways, continues to expand. Ceramic material properties have long been appreciated in high-speed machine tool spindles, for example, and are giving hybrid bearings advantages over all-steel units in an increasing variety of other applications.
In particular, their lower boundary-lubrication coefficient of friction enables greater efficiency under poor lubrication conditions, and they are more resistant to surface damage from particulate contaminants. In addition, they tend to exhibit lower operating temperatures and, of course, they avoid the risk of steel-to-steel welding.
These benefits all contribute to extending rating life - a key factor when selecting bearings, although not the only consideration. Ceramics also offer high electrical resistance and low weight, for instance.
Flaws in conventional bearing life modelling
Using the conventional bearing life model, engineers enter their application’s expected loads into an equation which determines the bearing design’s dynamic load rating C. This is based on sub-surface fatigue, which accumulates over millions of loading and unloading cycles, and ultimately results in bearing failure.
In the real world, however, surface fatigue rather than sub-surface fatigue is what causes most bearings to fail, and at its root is damage due to poor lubrication or contamination. Although modern standards such as ISO 281 try to address this with correction factors, they are unable to give a true reflection of real-life bearing behaviour.
In such modelling, the superiority of hybrid bearings in resisting surface fatigue under demanding lubrication and contamination conditions is overlooked. Instead, it can show them in a poor light because their less deformable nature concentrates loading over a smaller area - thus increasing stress and accelerating sub-surface fatigue. In short, the bearing life calculated is often inconsistent with performance measured in the field.
New Generalised Bearing Life Model (GLBM) for hybrid bearings
Over the course of several years, an SKF research team has developed a new model to address these deficiencies in calculating bearing life. It builds on the existing sub-surface fatigue model but adds modelling for surface failure and draws in endurance test data.
The researchers have studied every facet of bearing surfaces’ behaviour in detail, from their friction characteristics to the way dirt particles indent them under load. Hundreds of hybrid and all-steel bearings have been tested to calibrate and validate the resulting Generalised Bearing Life Model (GLBM) for hybrid bearings. The model has also been approved by a distinguished group of application engineers, after testing it against conventional estimation methods and their own real-world experience.
So what does this mean for engineers and designers? In applications where loading is heavy, but lubrication and cleanliness are favourable, the resistance of all-steel bearings to sub-surface fatigue may make them a better option. Where loads are lighter and bearings are more likely to be affected by poor lubrication or contamination, surface fatigue becomes more important. The new model not only confirms which bearing will give longer life in each situation but quantifies the difference.
The insights made possible by this model were recently highlighted by applying its calculations to four typical scenarios and comparing rating life between hybrid and all-steel bearings. Hybrid bearing life was eight times longer in a pump with diluted oil, and a hundred times longer in a screw compressor with contaminated lubricant. For two electric motors, under varying loads and with clean, well-lubricated conditions, there was little difference between hybrid and steel. In those cases, however, factors such as electrical resistance and extended grease life might still justify a hybrid bearing’s higher price.
With the advancements in modelling it is now possible to tell in advance whether a hybrid bearing will outperform a steel bearing, enabling engineers in many fields to have more confidence in their application/cost justification arguments.
Guillermo Morales-Espejel is Principal Scientist, Research and Technology Development at SKF
Key Points
- Electric Cylinders
- Food-grade bearing
- More motor efficiency
- SKF Commences Civil Action Over Counterfeit Bearings
- Bearing with food safety features
- Seamless engineering
- SKF & Imperial College London extend relationship
- Still got the power
- Enabling more sustainable compressed air production
- SKF to acquire Kaydon Corporation