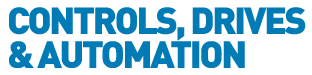
![]() |
Charlotte Stonestreet
Managing Editor |
Embracing a partnership approach to productivity
27 June 2016
Simon Keogh, General Manager at Siemens Factory Automation and Control Products, explores why a partnership approach to automation technology procurement and deployment is key to supporting manufacturer efficiency and UK productivity
The UK’s industrial output is beginning to recover following a drop in productivity towards the end of last year, with industrial production rising by two per cent in March. Despite recent warnings from The British Chambers of Commerce that the UK manufacturing sector is approaching stagnation in 2016 and that UK industry is in a recession for the third time in eight years, businesses are now in a position to consolidate their gains. It is therefore clear that the UK could benefit from a further boost to bring its productivity levels in line with the standard displayed by a number of other G7 nations.
Notably, research from the ONS has highlighted that the UK is far less productive than countries more advanced in their use of automation technology, such as Germany (24 per cent more productive), France (18 per cent) and the USA (45 per cent). Further research has found that the investment of an additional £1.2bn into manufacturing processes to increase the levels of robotics and automation could add as much as £60.5bn to the UK economy over the next decade. Adoption of these technologies, particularly automation, will be key in working towards Industry 4.0.
Education in automation
Education is by far the greatest barrier currently facing UK manufacturers in meeting these challenges. All businesses aim to increase productivity and decrease running costs, and while many have heard of Industry 4.0 and automation, there are also numerous organisations unaware of the technology available to help bring them to the forefront of manufacturing, let alone how to best procure it.
This challenge cannot be met by industry alone, which is why we recently introduced the Siemens Partner 2020 programme to facilitate access to our network of solution partners and distributors. Working in partnership, manufacturers can gain access to specialist industry knowledge and technical expertise to help make the most efficient use of automation technology. Implementing a partnership approach to technology procurement and deployment, as well as tapping into local expertise and sector insight, has been shown to boost manufacturing productivity and reduce costs by up to 30% in factories across the UK.
In addition to manufacturers seeking advice on the most suitable technology to support their business objectives is the issue of human capital. One of the most important areas executives must consider is hiring workers with a grounding in traditional manufacturing processes, and a multi-disciplined understanding of automation, IT and data analytics. Investment in new technology provides no business benefit if the workforce is unable to extract maximum value from it. The key to improved growth and productivity will be determined by a combination of how manufacturers invest in technology and find the right people to use it, with education being the lynchpin between the two.
Data-led productivity
Automation technology is designed to provide consistent data management control, delivering plant visualisation and increasing work efficiency, and will be a key driver in boosting manufacturing productivity. The key to the long-term success of automation technology, however, is ensuring a maximum ROI for the businesses utilising it. One of the most important aspects of the Partner 2020 programme is advising on whether a business can benefit from automation technology in the first place, with the gathering and analysis of pertinent data a key aspect of this process.
The first step towards achieving a smart factory is assessing the current situation – this process begins with a digital health check. We set up a benchmark based on each individual business’ stage of automation readiness and use this information to set up a personalised app. This allows the right questions to be asked about the technology, such as whether inward / outward goods are monitored, or whether these processes are linked to purchasing systems. We then advise whether this company can in fact benefit from automation technology, and recommend next steps in meeting that goal.
For the UK&I to compete on the global manufacturing stage and solve the productivity puzzle, more investment needs to be made in the right technology across its entire ecosystem, including data analytics capabilities. The longer manufacturers persevere with unconnected legacy systems, the greater the risk to the long-term efficiency and competitiveness of a plant. No matter how long manufacturers try to ‘sweat an asset’, over time, legacy equipment becomes more susceptible to failure causing production shutdowns, with parts needing to be sourced and replaced.
A collaborative approach
To ensure optimal business benefit from the introduction of automation technology, executives and business leaders in the UK&I have an opportunity to engage with industry boosting initiatives such as Government-backed Catapult centres. These centres focus on business-led collaboration in a multitude of sectors, including manufacturing and pharmaceuticals. We have collaborated with a High Value Manufacturing Catapult, the Manufacturing Technology Centre in Coventry, which assists with bringing new concepts into reality, increasing focus on innovative products for reconfigurable manufacturing and helping to provide the next generation of skilled workers.
One leading example of the automation technology on offer is Siemens’ Product Lifecycle Management (PLM). We call this system Team Centre, and it is currently the world’s most widely utilised PLM software. Within global businesses, there can often be hundreds of engineers designing a multitude of different products. In the past, when the design of one of these products is modified, it would cause notable disruption in the manufacturing process. With this technology, however, when a product’s design is changed or updated, the intelligent software automatically updates other products within the network to ensure compatibility, vastly increasing efficiencies.
Tapping into local expertise
The UK&I prides itself on running systems on a tight budget, the downside is a long term productivity loss. A partnership approach to procuring proven technology that will boost manufacturing productivity and reduce costs is therefore key. The growing adoption of innovative technology adds a new dynamic and makes the need to understand its complexities more important than ever. Through building a business relationship with the right partners and suppliers, manufacturers can fully utilise local and technological expertise – helping both their industry and the productivity of the UK as a whole.
This automation revolution is being felt across the industry. We have also seen an increased uptake of automation technology within the consumer market, resulting in more agile manufacturing and enabling faster delivery of products to market. The trend towards customisation is evident across manufacturing sectors from automotive to electronics. This can be seen within food and beverage organisations that are allowing customers to specify and adapt ingredients in their food to their specific tastes. Another example is in the customisation and design of bespoke garments, with customers able to select the designs and overlay them onto clothing.
Mitigating risk; improving productivity
With so much at stake, employing a partnership approach to infrastructure improvements will be key to mitigating risk. Understanding the benefits of deploying the latest technologies as well as utilising the available data in key decisions will deliver significant improvements to productivity. Procuring the latest technology through authorised routes will ensure specialist sector expertise is delivered to the industry, so manufacturers are protected from downtime and a drop in revenue. The primary issue is that manufacturers are unaware of the efficiencies they could be making because they often don’t have an end-to-end automation strategy in place, this often results in a disparate manufacturing facility without a total view of critical production data that often is required by customers and drives investment decisions.
The benefit of automation and digitisation technology is evident once in place, although a lack of education still hinders widespread adoption. Without investing in our manufacturing sector and fully utilising automation technology we run the risk of losing our global competitive position and may see contracts lost to overseas manufacturers able to provide a faster and cheaper service. Used correctly, these technologies have the potential to boost ROI for individual manufacturers across all industries, while also contributing to the UK’s broader economic output and success.
Key Points
- Research finds investment of £1.2bn to increase the levels of robotics and automation in manufacturing could add as much as £60.5bn to UK economy over the next decade
- For the UK&I to compete on global manufacturing stage, more investment needs to be made in the right technology across its entire ecosystem, including data analytics capabilities
- Increased uptake of automation technology within consumer market, results in more agile manufacturing and enabling faster delivery of products to market
- Siemens & DAI launch technology hub
- Siemens launches 'Partner 2020' plan to tackle productivity shortfall
- Siemens boosts food & beverage team
- Multi-touch & gesture operation
- Education, investment & innovation
- Siemens strengthens Large Drives network through strategic partnership with Indrico
- Defend in depth
- Siemens & OCR launch UK engineering skills partnership
- Business leaders outline digital roadmap for industry
- FZG Gear Unit Partnership
- No related articles listed