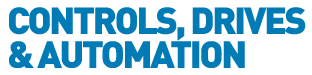
![]() |
Charlotte Stonestreet
Managing Editor |
Maximising ROI from enclosures
09 January 2017
Modular freestanding enclosures offer a number of key advantages when compared to traditional Unibody enclosures. Rittal consulting engineer Nathan Xavier explores the savings that can be realised over the lifespan of an enclosure after factoring in common use and operating costs
When specifications for control panels and other applications are written, the true costs and benefits of utilising one type of enclosure over another should be fully considered.
The strength of a modular enclosure lies with its frame. The frame consists of metal forms with a series of holes spaced at standardised units of dimensions, such that common accessories can be added to the interior without drilling or welding. Traditional Unibody enclosures are folded sheets of metal with welded seams designed for singular use. Changes are very difficult without costly fabrication techniques.
The flexibility provided by a modular enclosure system allows for easier modification. The design process is smoother with standard solutions available as off-the-shelf accessories. The overall design process is also much more forgiving - early mistakes can be corrected or late changes can be accommodated.
Mounting panel
The most commonly modified part on any enclosure, the mounting panel, differs in both construction and ease of use. Unibody panels are generally painted steel and constructed with an L-fold around the perimeter to stiffen them. Modular panels are generally zinc-plated steel allowing for an easier, more accessible ground that does not require the scraping of paint. They may also feature a C-fold for easier handling and greater strength.
The modular enclosure design allows for the addition of rails, making it possible to slide the panel into and out of the front, side, or rear enclosure openings. This saves time and increases safety when compared to the Unibody technique of laying the enclosure on its back and lifting the panel with a crane or forklift.
The construction of a modular enclosure allows for a greater opening and thus a larger mounting panel when compared to a Unibody cabinet. Also, because the modular enclosure can be ordered without a cable plinth, the overall size of the unit can be enlarged further increasing the panel size.
Misconceptions
A common misconception is that modular enclosures are not as strong as Unibody enclosures. This stems from the enclosure walls being thinner in a modular enclosure than in a Unibody enclosure. However, the strength of a modular enclosure comes from its frame, not the enclosure walls. The load being exerted on the enclosure due to the weight of the equipment installed is transferred to the vertical frame members.
Assembly work, while required, is minimal for a basic modular enclosure system. The more complex the configuration, the more assembly required. However, the system accessories can be added by someone without specialised training, unlike the more difficult fabrication techniques needed to modify a Unibody enclosure.
True Cost
True cost is calculated by simply summing the costs of an enclosure over the course of its lifecycle.
Acquisition Costs
The primary beneficiary of reduced acquisition costs will be the system designer. After the initial purchase decision is made, panel shops and integrators are more likely to be concerned with use costs, while a significant portion of the true cost for end users will come from operating costs.
With a traditional Unibody enclosure, system designers must be careful to accurately define the scope of work of a project, such that this information can be conveyed to an enclosure manufacturer.
Modular enclosures offer the ability for the designer to create special one-off configurations using standard catalogue items. These are pre-engineered such that direct communication with the enclosure manufacturer may not be necessary. Standard parts are likely to be in stock, significantly reducing lead times.
Use Costs
Use costs are mostly attributed to labour and the use of floor space during integration.
On a traditional Unibody cabinet with a continuous (piano) door hinge, removal and installation of the door can take up to 30 minutes. For this reason, most integrators choose to leave the door in place and perform cut-outs while the enclosure is on its back – taking up valuable floor space and in many cases, incurring additional labour costs involved in tilting the enclosure on its back including the possible use of cranes or forklifts. When cut-outs are done this way, it is very common for the metal shavings created by the cut-out to fall into the enclosure – requiring a thorough cleaning to remove and adding even more labour costs to the process.
Conversely, the doors of a modular enclosure are attached by multi-point, captive hinges and can be removed in as little as 30 seconds and taken to a separate location for modification. The costs associated with properly positioning a Unibody enclosure for door modifications are completely eliminated and as an added benefit, work can be performed inside the enclosure at the same time as the cut-outs are being made to the door resulting in increased productivity.
With a truly modular enclosure, all of the skins including the sidewalls and roof are removable as well. Since it is very common for enclosures to be modified to accommodate, among other things, some type of component cooling solution such as fans, heat exchangers or air conditioners, the ability to simply remove the mounting surface for modification is a tremendous advantage.
Mounting panel removal and replacement in a Unibody cabinet can require extensive labour and machine costs. A crane or forklift is needed to put the enclosure on its back, remove the panel for equipment installation, drop it back in over the studs and then raise the enclosure back to its upright position. With using a crane, there is a risk that the paint finish will be damaged.
Mounting panels customarily found in modular enclosures are larger in height and width, depth adjustable and easily slide in and out of the enclosure.
Because of their thick 10-12 gauge steel construction, Unibody cabinets weigh considerably more than their modular counterparts. Without sacrificing strength or protection, modular enclosures are lighter and thus easier to transport around the shop floor and cheaper to ship.
Last minute changes and/or re-designs can often happen. Modular enclosures offer the ability to reverse the door hinge, replace a rear wall with a door, swing a side panel, or add an accessory with little more than a few self-tapping screws. Unibody options are limited to expensive fabrication procedures and may not even be possible to implement in the field, leaving a special order from the enclosure manufacturer as the sole option.
Operating Costs
Operating costs generally include labour for maintenance, lost productivity due to downtime and costs incurred during expansion.
Scheduled maintenance on machines and control panels is necessary to keep operations running smoothly. Unscheduled maintenance, on the other hand, can cost a company millions in lost productivity. The flexibility of modular enclosures makes them easier to maintain and limits users’ exposure to unplanned downtime. Doors, walls and roofs can all be removed within minutes of an occurrence, allowing for easier access to installed equipment and simplifying what can be very labour intensive processes with Unibody enclosures.
If the control panel in a Unibody cabinet is full and additional equipment needs to be installed, a new, larger enclosure is usually required. With this comes the removal and reinstallation of existing components to the new panel. Conversely, if a similar need to expand the capacity of a control panel arises while using a modular enclosure, multiple options exist to quickly and easily install new equipment to complete the expansion.
Reference: Nathan Xavier (Rittal Corporation Consulting Engineer): Practical Benefits of Modular Industrial Enclosures (white paper)
Key Points
- Modular enclosures offer the ability for the designer to create special one-off configurations using standard catalogue items
- The modular design allows for the addition of rails, making it possible to slide the panel into and out of the front, side, or rear enclosure openings
- Doors, walls and roofs can all be removed within minutes of an occurrence, allowing for easier access to installed equipment
- No related articles listed