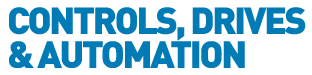
![]() |
Charlotte Stonestreet
Managing Editor |
Home> | MACHINE BUILDING & ENGINEERING | >Enclosures | >How automation became a reality |
How automation became a reality
17 August 2015
Full-scale automation of control panel production has become far more accessible thanks to Rittal's acquisition of Kiesling a few years ago
Kiesling is well-known as a specialist supplier of automation systems for switchgear manufacture. Its core products include machining centres for the preparation of switchgear enclosures, cutting centres, assembly machines for terminal blocks, assembly workplaces and an enclosure testing system.
The company started more than forty years ago and since then has specialised in drive technology. Around twenty years ago, it created a mechanical engineering division, along with what believed to be the first-ever processing centre for enclosure engineering. This meant that all mechanical processing steps in the assembly of enclosures – including drilling, thread cutting, and milling of cut-outs – could be accomplished in a single work step.
Since the acquisition of Kiesling the combination of its machines, Rittal’s well-established enclosure engineering capabilities, and the involvement of Rittal’s sister companies, Eplan and Cideon, has enabled total automation of the production of control panels for Rittal's global customer base.
The two companies, Eplan and Cideon, combine to streamline the complex processes of product design and order processing. They bring in their joint electronic and mechanical CAD capabilities along with links to the enterprise software system, SAP, and market-leading product lifecycle management systems.
All this means that Rittal can now provide panel builders with a superb end-to-end service, optimising work-flow from the conceptual design stage and full product integration - including parts machining and automated panel wiring – through to the testing of the finished panel.
Robotic wiring centre
But Kiesling hasn’t finished innovating. In 2014, following five years of development, Kiesling launched its Averex robotic wiring centre – another world-first.
Averex automatically makes connections between devices while at the same time ensuring standards and safety requirements are met. It’s a huge time-saving advance - indeed Kiesling estimates Averex reduces the number of working hours per enclosure by an astonishing 15 hours.
Additional features, such as push-in connections and automatic wire-changing and labelling further increase the degree of automation that can be achieved.
The Averex wiring centre will be of particular help to manufacturers using production processes where the same wiring configurations are used over and over again, and on a scale close to mass production.
Essentially, Averex has a huge role to play in wiring enclosure mounting plates. The system cuts the wires to the correct length before stripping and crimping them with wire ferrules. Then, it feeds the wires through the cable duct and attaches them to components such as terminal blocks, contactors and motor circuit breakers.
On average, it takes around 180 seconds to complete this wiring process manually – but Averex finishes the same task in approximately 40 seconds. What’s more, the system is exceptionally reliable, using laser technology to identify the parts and to check their dimensions against the assembly tolerances.
Its patented machine head can be rotated 270 degrees and includes cable routing, cutting, stripping and crimping units, torque-controlled screwing and a tool changer that can hold up to six tools. In addition to screw connections, terminal blocks with push-in connections can also be used with this system.
Data from Eplan along with information on components and their respective locations on the mounting plate, are used to check the manually assembled mounting plate before the components are wired up automatically and autonomously. The result is a significantly faster system of wiring that would otherwise be performed by hand.
3D Laser Centre
And Kiesling has just announced the launch of a 3D laser centre, the Perforex LC 3015, a new addition to its enclosure machining centres.
As well as machining panels, manufacturers of controllers and switchgear can now quickly process complete housings. Fully welded enclosures can be machined from a number of sides and in one operation without re-clamping being required, speeding up the process further.
Key Points
- Around twenty years ago, Kiesling created what is believed to be the first-ever processing centre for enclosure engineering
- Rittal's acquisition of Kiesling has enabled total automation of the production of control panels for Rittal's global customer base
- Kiesling's Averex robotic wiring centre automatically makes connections between devices while ensuring standards and safety requirements are met
- New generation cooling technology
- EPLAN PLATFORM 2.1 IS RELEASED
- Up to 15% more space
- Climate Control Need Identified
- Housings for TFT monitors
- Lower overheads & operational costs
- Key trends & challenges in the global IT market
- Electrical safety assured
- Create space in enclosures
- Industry 4.0 whitepaper