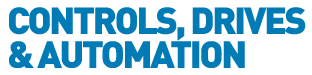
![]() |
Charlotte Stonestreet
Managing Editor |
The impact of digital technologies in manufacturing
02 March 2017
Following the conclusion of the Digitising Manufacturing Conference at the Manufacturing Technology Centre (MTC) in Coventry on last November, 16 experts in digital manufacturing sat round a table for an hour or so to discuss some of the key opportunities and threats
The discussion was opened by Dr David Bott of the Warwick Manufacturing Group (WMG) and moderated by CDA’s Consulting Editor, Andy Pye.
David Bott: “Manufacturing is a physical thing. However, over the past decade, as computers have become more common and more powerful, we have created a parallel industry where people turn raw data into useful information. This has radically changed the business model.
“When I started my career in the chemical industry chemical plants involved a lot of pipes and lots of people changing valves. When it went wrong somebody knew how to fix it, but also there was the beginning of modelling chemical processes.
“Since then, computers have doubled in processing power every 18 months, and modelling rapidly became a real-time process. In reality, this is running a computer game – a simulation - which models all the possible outcomes based on the control parameters. And so chemical plants are now managed by just two or three people sitting in a room with a coffee machine and the occasional person who goes out to maintain things.
The impact on the SME
Andy Pye: Are we generally more comfortable with digital factories or more fearful?
Paul Walker: “While this is fine for larger companies, it represents a huge challenge for an SME. One of my key raw materials suppliers does not even possess a single computer! Delivery notes are handwritten; accounts are done in pen and ink in ledgers. It is so ‘dark ages’ it’s hard to comprehend. When I introduced mandatory labelling for my products, I had to send them barcodes to photocopy and place on their raw material. That’s how far behind some SMEs are in this country. There are hundreds of them who would listen to this discussion and shake their heads wondering what we are talking about.”
Chris Greenough: “Digitisation has been pushed through the large OEMs and First Tier companies and that hasn’t filtered down to the SMEs. Yet, this is where the biggest potential improvement is.”
Andy Pye: Is it still not really recognised that the SME economy is so vitally important to the nation?
Adam Payne: “It is recognised – as Chris says, it is easy to roll it out to the OEMs, they have the investment and teams. But it is the manufacturing SMEs that can make the biggest difference – they can get so much out of it - energy savings, remote monitoring. Therefore, we need to see a proper manufacturing policy, which involves everyone, so we all get to the same end goal.”
Justin Leonard: “With SMEs, we need to approach Industry 4.0 in small steps. For example, we can introduce smart products that can indicate how long they are going to last (say, warning 50%, 75% of the way through the lifetime). Users of these products don’t have a lights-out factory, but they are already using Industry 4.0 technology, they just don’t realise it.”
Martin Strutt: I completely agree. People in the food and drink sector are using it to get closer to their customers and understand what their demand is.”
Paul O'Donnell: “I also agree with Justin. It is much easier for an SME to look at the technologies in a piecemeal way. An SME is not going to dedicate an Industry 4.0 change team and transfer processes overnight.”
Lena Huertas: “There is a group being formed called the Digital Engineering and Manufacturing Group, which has 20-30 industrial members. It is trying to bring together as many stakeholders as possible to outreach to the SME market. It is a key topic because 99% of our primary businesses are SMEs. The key thing is understanding where you are starting from and break down the journey into small steps, such as digitising CAD drawings.“
Chris Brown: “Technology has its place and its application. But I visited a company this morning which does anodising and NDT. They are not going to automate their process because they won’t replace their machinery anytime soon. What could such a company do to embrace this technology?
David Thomas: “There is a big responsibility for a company like Siemens to work with our SME community. Another problem is that the Lexicon of Industry 4.0 boggles people.
Alan Norbury: “To answer Chris, I’ll give you a good example – at Siemens, we engage with the supply chain to help our Congleton factory. One supplier used to come in and then replenish tote bins containing fasteners if they were empty. Now, they use a remotely-accessible weigh-scale and know whether or not they need to come in and replenish. What did it cost their business – nothing! The supply chain saves money and they own the stock, so everyone wins.”
Laura Jones: “We see similar challenges in the legal profession. Our business is all about people and bring them with us, we need to educate those who are reluctant to change and translate the lexicon into plain English.”
Jobs & skills
Adam Payne: “I believe we are on the cusp on one of the biggest issues we have jobwise. The number of people that will become unemployed due to autonomous vehicles is phenomenal. While in Japan, there are restaurants that even have robots as waiters.”
David Thomas: We need to address the problem of how we safeguard work. Where are our 400 people going to get jobs if we bring the robots in?”
Chris Greenhough: “We need to get into schools and teacher training colleges and train the people who are to fill the new jobs. Teachers now don't know what manufacturing is yet, they are teaching it to the next generation.”
Rachel Lawley: “IT is such a big part of it - more sub-level IT is needed – how to do coding and so on. Most colleges don’t touch on this but just focus on Microsoft Office skills!”
David Thomas: “Through the Siemens Junior Factory, our young engineers know a lot more about how the operational management side of the business runs than I did when I was a production engineer.”
Olivia Kelly: “I came out of education recently and am just 20 years old. I learned CAD at college. I know that in five years 50% of traditional jobs will be gone. But there will be a new set of people who will have Industry 4.0 skills, brought up with IPads and IPhones. So when we come into an engineering business we expect to see digitisation, and not handwritten ledgers.
“Younger people do have the skills, while older people are more fearful. I can put on an IPad on a machine and control it and they say ‘Why can't we just push buttons on the machine instead?’ A lot of it is trying to make them understand why we are doing it, then they realise that it’s not a bad thing and they will not lose their jobs.
"Our generation is really interested in it!”
- CASBOT unveils full-size biped humanoid robot
- Innovation & flexibility
- High-purity copper recycling breakthrough
- The multi-sector potential of 3D printing
- Mesh network of sensors guides vehicles autonomously
- New Trustworthy Autonomous Systems projects launched
- Skills shortage in aerospace & automotive industries
- Infosecurity: stop throwing rocks at each other
- Enables easy mobile robot automisation
- AI in the energy sector
- No related articles listed