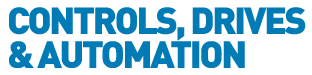
![]() |
Charlotte Stonestreet
Managing Editor |
Home> | AUTOMATION | >Handling & Logistics | >Evolution In the Warehouse |
MORE FROM THIS COMPANY
- Enables easy mobile robot automisation
- Brexit threat to research & innovation
- Are you ready for the changes to EU Authorised Representatives?
- Bosch Rexroth confirms event partnership for Maintec 2018
- Real-time assistance app
- Manufacturers leading the charge in AI adoption
- SAFETY & SECURITY - STRANGE BEDFELLOWS
- SPS – bringing automation to life
- Call for accelerated robotics adoption
- ForwardX Robotics announces strategic partnership with Lynx Automation
RELATED ARTICLES
OTHER ARTICLES IN THIS SECTION