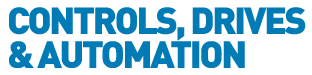
![]() |
Charlotte Stonestreet
Managing Editor |
Home> | INDUSTRY FOCUSES | >Printing & Packaging | >A QUIET REVOLUTION IN SERVO-MOTOR DESIGN |
Home> | DRIVES & MOTORS | >Servo Motors & Drives | >A QUIET REVOLUTION IN SERVO-MOTOR DESIGN |
A QUIET REVOLUTION IN SERVO-MOTOR DESIGN
06 November 2012
A quiet digital revolution in the control and application of brushless servo motors and drives is promising a step-change in technology which its developers believe will be accepted as a new industry standard.
According to Sick, the benefits of its Hiperface DSL (Digital-Servo-Link) motor feedback interface are already being adopted by motor and drive manufacturers worldwide, who are gradually introducing it into new motor and drive designs. Since its launch in mid-2011, four significant manufacturers – Beckhoff, Parker, Robox and Selema – have all launched enabled drives and motors and Sick anticipates further announcements during 2012.
The benefits of a new, completely, digital communications protocol for carrying servo data from the motor to the drive electronics are significant. They promise to save costs, improve speed regulation and enable a more compact motor design. These advances will benefit not only the motor and drive manufacturers themselves, but also machine builders and systems integrators who are demanding smaller and more efficient motors.
End-users are set to benefit from lower costs and improved operator safety.
At the centre of the advance is a fully digital encoder interface protocol which eliminates the problem of electro-magnetic interference encountered in previous analogue systems and therefore the risk of signal degradation.
DRIVE, PROMISES MAJOR COST REDUCTIONS
The new digital interface is so robust that cores inside the motor power cable can be used for the communication of feedback data to the drive – a first for the industry.
The twisted pair traditionally used for the temperature winding sensor in a standard motor power cable is used for the Hiperface DSL communication.
ONE-CABLE SOLUTION
The result is that the need for a separate dedicated feedback cable is completely eliminated. The elimination of a second cable, together with the loss of connectors to the motor and drive, promises major cost reductions.
The savings enable motor manufacturers to be more competitive in pricing as well as significantly reducing error possibilities for connector and cable faults. Commissioning times are also reduced significantly.
Hiperface DSL also offers significant benefits for operator safety, having been developed with safe drive systems in mind. It is currently the only motor feedback interface to incorporate the redundancy and error checking required to achieve both SIL2 (PLd) and SIL3 (PLe) levels for safe speed and safe position functions.The Sick Hiperface DSL interface comprises an enabled encoder on the motor and software to program the servo drive via the standard Field Programmable Gate Array. The encoders also provide opportunities for improved condition monitoring and preventative maintenance.
Temperature, speed and rotation information will be logged inside the encoder with all information accessible via Hiperface DSL.
Open accessibility to this information will enable plant operators and maintenance engineers to plan maintenance more effectively, enabling increased plant availability and reducing machine downtime.
Encoders supporting Hiperface DSL have an optional input for digitisation of the temperature signal and transmission to the drive together with encoder feedback data. With future applications in mind, Hiperface DSL will also allow the simple incorporation of additional sensor information to further enhance dynamic axis control, including torque, vibration and acceleration.
The robust protocol enables digital sensor data transmission over up to 100m based on two wires integrated with the motor power cable.
FUTURE-PROOFING
A development of Sick’s previous Hiperface technology which is already a standard in motor and drive manufacture worldwide, the new interface has been developed closely with Sick customers to ensure a robust step-change in technology with the reliability expected of a system set to become adopted a standard in the years to come.
Sick expects the innovative solution to be taken up most quickly in robotic and automated machinery applications as well as for integration into process and packaging equipment.
Key Points
• A fully digital encoder interface protocol eliminates the problem of electro-magnetic interference encountered in analogue systems
• The new digital interface is so robust that cores inside the motor power cable can be used for the communication of feedback data to the drive
• Hiperface DSL offers significant benefits for operator safety
- SICK goes flat out for performance with mini smart sensors
- Up For A Challenge
- Powerful and compact cube sensor
- Rapid changeover solution
- High-definition streaming camera
- Robots with vision: There’s an App for that!
- All-in-one muting sets
- Distance sensor sets precision standard
- Ultrasonic sensors
- Accurate measurement