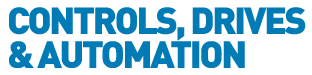
![]() |
Charlotte Stonestreet
Managing Editor |
Are PID controllers still good enough?
17 January 2022
JOHANN LAINER from industrial temperature controller manufacturer, Watlow, examines why PID controllers are still a valuable tool in today’s industry.
PID controllers are used in most automatic process control applications to regulate flow, temperature, pressure, level, and many other industrial process variables.
PID technology has been around for nearly a century. Russian-American engineer Nicolas Minorsky developed the formal control law in 1922, now known as PID. It was a popular solution for many years because a PID controller can be implemented with analog circuits. Then, in the 1980s as computational capabilities increased, its popularity grew even more as the solution did not need multiple resources to run.
A common example of a PID controller is vehicle cruise control. The driver selects the speed they want to maintain, which is the desired set point. The input is the speed of the car and the output is the accelerator. As the vehicle travels up a hill and loses speed, the PID controller calculates the current state to determine what is needed to maintain the set point. The car speeds up as more fuel is delivered to the engine. As the vehicle descends the hill, the PID controller reduces the flow of fuel to reduce the speed to the set point.
Where to use PID controllers
If your application requires maintaining temperature or pressure, a PID loop is an appropriate solution. However, use cases for PID controllers are circumstantial. Consider a minivan and a sports car. Both vehicles will transport people, but the sports car is not going to help a family of seven. Similarly, PID controllers do not fit every situation, but they still have a place in various situations.
If your application requires maintaining temperature or pressure, a PID loop is likely an appropriate solution. However, the PID controller may not be suitable for the start-up and shut down stages of the process. Understanding the full scope of the system is crucial to knowing if a PID controller is right for your setup.
PID gets an upgrade
PID controllers have a loyal following for a variety of reasons. The technology is simple to understand, and for many applications, it is effective. However, advancements in controllers can provide several benefits. Modernized controllers may save time by reducing downtime, which increases production, reducing fuel consumption that saves money or any number of benefits.
Emerging technologies are designed to return the setup to the ideal set point faster while minimizing overshooting the set point. Ultimately, with even marginal improvements in the efficiency of a process, companies can save time and money.
In some instances, using add-ons or multiple PIDs can achieve new results. For instance, feed-forward controllers act as an add-on to a PID controller by assisting the PID in reaching the set point faster and more reliably. While implementing a feed-forward controller is more costly, and can take more time, the benefits include improved accuracy, reduced energy use and lower maintenance costs.
Model Predictive Controllers (MPC) coordinate inputs and outputs to the system to make highly effective control decisions. In addition, MPCs have a prediction horizon, in which they anticipate what will happen within the system based on inputs. While traditional PID controllers are one-size-fits-all solutions, an MPC is tailored to the system in which it operates.
Override Controllers use two PID controllers to calculate separate process variables and a switch to select the controller output. The switch determines which PID controller to follow based on a set condition, such as the smallest or largest output.
While these setups are a little more complex than using a single PID, they can lead to marginal improvements that give your company an advantage over the competition.
Making the right choice
Understanding what solution is right for your industrial application can be difficult when there are so many on the market. It’s companies like Watlow, which has manufactured thermal equipment since 1922, which can make this decision easier. Watlow has experts on hand to provide support in optimizing your solutions to achieve the desired goals. This includes advising on a range of temperature and process controllers including PID models for different processes.
While advancements in computational technologies originally made for a bleak future of PID controllers, they have proven to remain a vital piece of equipment in many modern applications. These versatile controllers can be combined with add-ons to provide flexible solutions, with accurate outcomes. But first, it’s understanding the specifics and what’s right for a system that will ensure the desired results.
- Watlow to present at Net-Zero Food and Beverage Forum in Berlin
- ATS: the heating, sensing and controlling suite of tomorrow
- Thermal loop solutions
- Complying with life science sterilisation control mandates
- Getting familiar with electric process heaters
- Watlow to exhibit at SPS Italia 2023
- Digitalisation and food safety
- The hot topic of data
- Taking a systems approach to solve electrification challenges
- Watlow launches Prime Distributor Programme across Europe