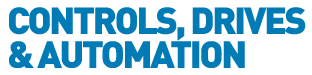
![]() |
Charlotte Stonestreet
Managing Editor |
Automation without cabinets
07 September 2020
Bradley McEwan explains how new servo drive and connectivity technologies can help manufacturers do a lot more with less.
Modular units are becoming more established as a solution to modern production demands. They are faster to implement in new spaces, or integrate into existing production lines, with scope for manufacturers to be more responsive to changing conditions and demands to offer greater flexibility to their customers.
A less-considered advantage of modular units is how these can support in reclaiming valuable floor space in the industrial plant. Concerns surrounding machine real estate — or, of how square metres of plant space contribute towards revenue — are growing among manufacturers. These considerations go beyond the bottom line, with factors like throughput and environmental impact also being among the key considerations.
Aside for the obvious point that smaller machines occupy less space, if implemented correctly, such equipment makes it possible to increase manufacturing output without expanding a facility.
Yet, alongside the advantages of modular units, there are also challenges. They include how best to connect, integrate and power these machines in the production line. For such demands, we must turn to new approaches to machine design and functionality.
Panel-less system
One such approach relates to the control panels of machinery. Control panels can sometimes take up several metres of space in a production line — machine real estate that could otherwise be devoted to production. Furthermore, it is often the case among manufacturers that goals to reconfigure or expand production lines lead to an increasing number of mounted devices.
Saving space in control panels with downsized components is, therefore, the way forward in cases like these. This is a challenge when the number of devices used in control panels is increasing, due to more advanced and more composite machine functionality. Nevertheless, it’s a challenge that Beckhoff met, with a view to benefitting original equipment manufacturers (OEMs) and end users.
In one instance, Beckhoff worked closely with a well-known global packaging OEM. Beckhoff was enlisted to support with reducing costs throughout the complete lifecycle of the machine — from design, procurement and manufacturing to commissioning, shipping and onsite installation. Ultimately, the client wanted to reduce the footprint size of its equipment.
The resulting solution was to remove the control cabinets and build the automation components into the structure of the machine itself. The idea of a panel-less machine complements Beckhoff’s concept of “automation without cabinets”, whereby the size of the control cabinet is minimised. Whereas, previously, there were space requirements in the cabinet for the controller, servo drives and inputs/outputs (I/Os), this can now be drastically reduced by the automation without cabinets concept.
Side-by-side mounting
With the AMP8000 servo drive, the machine’s power electronics have been moved directly to the machine. This reduces the required space in the control cabinet to essential functions like incoming power, power distribution, isolators and fusing.
More specifically, the system integrates a safety rated servo drive in a very compact design, directly into the servomotor. This unique technology takes away the need to increase the motor’s frame size for a given power, which sets the system apart from Beckhoff’s competitors and is beneficial for modular machine concepts. The AMP8000 system allows full integration of the drive technology into the most individual machine concepts. In other words, the system can be flexibly adapted to a customer’s individual requirements, with a design flexibility that can minimise the space requirements in the control cabinet.
One cable automation
Beckhoff’s “one cable solution” complements the AMP8000. The idea is that a single cable can run through the machine in order to connect multiple distributed servo drives and I/O systems through a distribution module. Reducing the cabling to plug and sockets drastically also reduces wiring time and errors.
The key technology here is EtherCAT P, a new development in EtherCAT technology on the cabling level. The “P” stands for power and allows the use of standard four-wire Ethernet cable, not only for data, but also for two electrically isolated, individually switchable 24 Volt (3 Amp) power supplies.
With EtherCAT P, multiple EtherCAT devices can be connected, and complex machines or machine lines can be implemented with simple topologies. As a result, only one cable is required to connect and power inputs/outputs (I/Os) and other field devices, including servo drives.
The Beckhoff EtherCAT P I/O portfolio is comprehensive. Instead of having to use multiple connection cables between a control cabinet and a machine, a single cable to the AMP8805 distribution module is all it takes because each of the AMP8000 distribution servo drives is, in turn, connected to the distribution module with just a short cable. With EtherCAT P, the cable routes to the motor can be laid out much more clearly, and space requirements in the control cabinet are reduced to a minimum.
Furthermore, only one cable type is required for the entire system cabling. Also, preassembled system cables significantly reduce the time and cost required for logistics, cabling and commissioning, and minimise the risk of error.
Bringing it all together
With these technologies, it is now possible to develop systems that pack high performance and functionality into smaller footprints for automation engineers and plant managers. These systems no longer require complex, bulky control cabinets. Instead, machines require as little as a single compact distribution module.
An example might be a packaging machine with an in-built panel IPC, such as Beckhoff’s CP37 range, to control various functions in the machine — PLC, motion or robotics, for instance. The machine can contain an AMP8000 servo system that includes a servomotor with a rear-mounted servo drive, which occupies a footprint only slightly longer than a conventional servomotor. This connects to a power supply module that, due to its IP65 protection rating, can be housed inside the machine. This module draws power from the mains network to power up to five servosystems and input/output (I/O) units, such as Beckhoff’s EPP modules. The machine then operates as a self-contained system.
If a machine is using multiple servosystems, these can be connected to a small number of compact coupling modules. Because each module connects and powers up to five servosystems and only requires one input cable, any external cabinets that are required become significantly smaller. These cabinets, due to their smaller size and the shorter single cable runs required, can be positioned closer to the machine, further conserving floor space.
The end result is clear: a sophisticated machine with a smaller footprint, which means lower cost shipping and quicker installation for machine builders and higher output per square metre of production space for end-users.
For many, subtraction doesn’t come naturally. But, with the right equipment, it’s certainly possible for manufacturers to achieve a lot more with less.
Bradley McEwan is business development manager at Beckhoff Automation UK
- Experience 'Integrated Industry' now: With ready-to-use products for IoT and Industrie 4.0 from Beckhoff
- Small batch, big impact
- ‘Plug & Work’ bus terminals
- The crucial role of I/O communication
- Protecting while connecting
- Hazardous area control panels
- New automation technologies
- Beckhoff joins AMHSA
- Many-core machine control
- Making, not taking jobs