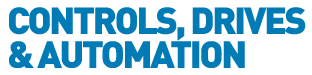
![]() |
Charlotte Stonestreet
Managing Editor |
Conveying the benefits
05 April 2019
Charlotte Stonestreet takes a look at the advantages automation can bring to the handling and storage sector and the technologies behind the applications
The use of automation for handling and storage tasks has long been recognised as having the potential to provide easily measurable benefits in terms of increased throughput and decreased operating costs. Where appropriate, increased use of automation means staff can be re-deployed to higher-value, more complex roles, often leading to a more satisfied workforce. Health and safety is also enhanced as levels of manual handling are kept to a minimum.
Despite the benefits, the decision to automate is not always a straightforward one and, according to RARUK Automation, in some cases decision-makers have made expensive investments in automated guided vehicles (AGVs), which don’t provide the flexibility needed in today’s agile manufacturing processes. However, asserts the company, new sensor and software technologies make autonomous mobile robots (AMRs) ideal for unpredictable or changing production layouts and dynamic work environments.
Agile manufacturing is allowing companies to adapt to fast-changing market demands and maintain their competitiveness, but on-time delivery of materials and assemblies within those facilities continues to be a challenge. Manual transportation requires workers to leave their stations to push carts loaded with materials between manufacturing processes and the stockroom, and can result in production backlogs and idle workers as they wait for assemblies and parts to be delivered. Automating this process has been a challenge.
Plant set-up is often dynamic, with new production cells and processes that must be supported and people, equipment, pallets, and other obstacles can appear in what used to be open passageways. Any automated material transportation approach must be flexible and easily adaptable without additional cost or disruption to processes, not to mention safe for operation around employees. That flexibility also means that automated material handling must be easy to learn, program, deploy, and redeploy in-house to ensure that the chosen approach can cost-effectively keep up-to-date with requirements.
Traditional automated guided vehicles (AGVs) move materials using fixed routes that are guided by permanent wires, magnetic strips, or sensors embedded in the plant floor. However, those systems are inflexible, expensive, and disruptive for dynamic manufacturing floors. If manufacturing processes change, the facility must be updated again—and if people or material temporarily blocks the AGV’s route, it simply stops until the way is cleared. In contrast, today’s autonomous mobile robots (AMRs) are designed for dynamic environments. They offer the flexibility, safety, and cost-effectiveness that allows companies of nearly any size to automate and optimise material handling.
An AMR navigates via sensors, cameras, and sophisticated software that is built into the robot itself, without the need for external sensors or guides. Once the robot has learned its surroundings (either by uploading a facility blueprint or by piloting the robot around the plant to develop its own map), the robot recognises its surroundings and can take the most efficient route to its destination autonomously, safely avoiding obstacles and people. Because companies do not need to alter their facility with wires or sensors, the robot can be integrated within hours with no disruption to production.
Pallet conveyance
Reliable and efficient pallet handling is becoming increasingly important in modern goods flows. In many cases, this hinges primarily on keeping the transport times between goods receipt and goods dispatch, or between storage, production and commissioning facilities in a business to a minimum and ensuring that these transport processes are highly efficient by means of automation – and keeping planning processes streamlined, assembly requirements low and expansion options flexible.
Interroll's new Modular Pallet Conveyor Platform (MPP) is versatile pallet conveyor system which features a highly flexible modular design.
In conjunction with Interroll's tried-and-tested Pallet & Carton Flow flow storage system, the new pallet conveying platform is reported to be an ideal foundation on which to build comprehensive pallet storage and conveying solutions of any type and for any application. Unlike the flow storage system, in which pallets are buffered in intermediate storage areas on inclined belts due to the force of gravity, the MPP is a driven conveying system for pallets. Depending on the application scenario, the drive is powered by gear or drum motors, which even enables the creation of zero-pressure-accumulation conveyors.
The fully modular system can be planned and arranged extremely simply and conveniently using Interroll's popular Layouter tool. The MPP consists of chain or roller conveyors, as well as additional modules such as transfers and turntables. Unique modules for special functions are also available on request.
The modules are optimally coordinated and fully preassembled on delivery in order to make installation as easy as possible. Additionally, the system can be modified or expanded easily and cost-effectively at a later date.
Fully automated parcel loading
Dematic’s PackMyRide automation system is said to be the world's first fully automated solution concept for parcel loading. Currently, the Subsystem is being tested in a pilot project at one of the newest distribution centres of project partner DPD in Nagold. There, the system picks up packages from an existing intralogistics system and moves them to mobile racks via a rack feeder device. The racks are designed in a way that allows Dematic’s Automated Guided Vehicles (AGVs) to fully automatically transport them into the delivery vehicle. This will not only reduce the physical work of the delivery drivers, but will also add value by significantly reducing the time required for loading vehicles. It is expected that up to 80 percent of the package range can be handled by the system.
"With Dematic PackMyRide, we're revolutionising parcel loading for the last mile by introducing the world's first automated solution concept in this segment," says Dr. Daniel Jarr, Project Lead for Dematic PackMyRide. With the automation system, several delivery tours can be loaded simultaneously, offering significantly higher productivity and efficiency in parcel handling. "Our innovative solution concept not only provides ergonomic relief for the drivers, but also saves a great deal of time, which benefits the parcel delivery company along the value chain," says Jarr. The manual loading of the vehicles is a time-consuming step for the parcel delivery companies, which can be completely taken over by the automation system in the future.
PackMyRide is not only suitable for parcel delivery companies, but can also be used in other industry sectors. "The automation system is an innovation in productivity-enhancing optimisation for the last mile in a variety of segments," says Jarr. Dematic can develop an individual solution based on specific requirements. "We offer the system as an innovative solution concept and are open to further cooperation." says Jarr.
Tyre line productivity boost
A custom designed and engineered conveyor system, from Autarky Automation, is playing a key role in helping Tyre-Line, a leading supplier of wheel and tyre assemblies, boost productivity and quality. Installed as part of major production line upgrade, along with a Hofmann high speed inflating machine, the new system has reduced assembly and inflation time by a factor of ten, from around seventy to just seven seconds.
The Hofmann tyre inflation machine forms the heart of the new system. Capable of inflating each tyre in just seven seconds, the machine has infeed and outfeed conveyors, with the latter comprising two separate spurs: one for automotive wheels that need balancing and one for all other wheels.
Wheel rims and tyres are assembled and labelled with a unique bar code at the start of the infeed conveyor, with an extended track and additional loading and queuing zones leading up an inclined track to match the height of the tyre inflation machine.
Immediately prior to the inflation machine is a bar code reading station. This comprises an array of three camera units, with integrated lighting; these are positioned so that they can read barcode labels placed at any angle or position on the wheel rims. The information from each bar code is automatically transferred to the tyre inflation machine, to control the inflation pressure; it also allows a dimensional check to be carried out, confirming that the correct combination of tyre and wheel rim has been fitted.
The entire system has been designed to minimise the risk of damage to each assembly. For example, transfer units automatically align each assembly on the centre line of the conveyor, to prevent contact with side rollers, with all rollers being fitted with soft PVC sleeves. The downward sloping outfeed unit features inertia braking to control the speed with which the finished assembly is presented to the operator, while loading points use specially developed plastic raise/lower beds to make it easier for operators to load and unload wheel assemblies. Additionally, each wheel assembly is automatically kept within an independent zone, to prevent contact between wheels in the event of backup before the inflation machine.
The solution developed by Autarky Automation uses 24V DC motorised drive rollers throughout, with Siemens PLC and HMI to control the conveyors, transfer units and barcode readers; data is communicated to the Hofmann controller via a standard Profinet industrial network.
Truck-based robotics
Industrial truck manufacturer, Hyster Europe is working with French robotics specialist Balyo and recently demonstrated its intelligent robotics solutions with the Hyster LO7.0T tow tractor.
"Our robotic trucks use geonavigation technology developed by Balyo, which does not require complex infrastructure changes to automate logistical processes," said Timo Antony, Area Business Director Central Europe, Hyster. "Instead, the trucks work utilising the structural features within the building."
Hyster relies mainly on the geoguidance system for navigating the industrial trucks. Based on LIDAR technology, this system determines the position of the truck by orienting it at fixed points, such as walls, shelves or the building structure. Reflectors or other physical navigation aids are not necessary.
“These robotics solutions are based on our lift trucks from series production, and the trucks can still be operated manually," says Antony. "This great dual advantage means robot technology can be switched off at any time, and the driver can control the machines in manual mode if necessary. The lift trucks can therefore also be used spontaneously for other tasks. This makes Hyster robotic truck solutions significantly different from automated guided vehicle systems. This is because AGVs originally used for the transport of small parts automatically follow their specified routes and cannot be operated manually.”
In addition, some AGVs are restricted in navigation and cannot always avoid obstacles. The Hyster robotic trucks driven by Balyo, equipped with geonavigation technology, simply take a different route when needed. When a lift truck equipped with the geoguidance system encounters an obstacle, in most cases the software will detect an alternative route and the "robot" will be able to continue its journey automatically.
Key Points
- New sensor and software technologies make autonomous mobile robots (AMRs) ideal for unpredictable or changing production layouts
- Dematic’s PackMyRide automation system is said to be the world's first fully automated solution concept for parcel loading
- Hyster Europe is working with French robotics specialist Balyo and recently demonstrated its intelligent robotics solutions with the Hyster LO7.0T tow tractor
- Still work to be done on the Industry 4.0 journey
- MARCH awarded place on £50m United Utilities Monitoring and Control Systems Integration framework
- Feasibility funding for autonomous vehicle cyber security
- How digital advancements can boost manufacturing
- Motor Driven Systems Conference
- Collaboration key for car production
- Businesses urged to take control of connectivity amidst 5G challenges
- New technology lets humans & autonomous robots understand each other
- 3D Hubs launches manufacturing fund in fight against Covid-19
- Full-bore ball control valve
- No related articles listed