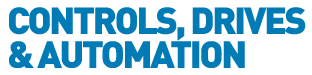
![]() |
Charlotte Stonestreet
Managing Editor |
Home> | MACHINE BUILDING & ENGINEERING | >I/O Systems | >DISTRIBUTED MODULAR I/O - ANSWERS & QUESTIONS |
DISTRIBUTED MODULAR I/O - ANSWERS & QUESTIONS
06 November 2012
Distributed I/O systems connected to an industrial network allow I/O data to be spread across the machine and outside the cabinet, reducing the total component and hardware costs of the system. Will Healy III, a network and connectivity market manager for Balluff North America, is your guide..
Businesses are turning to Distributed Modular I/O for improving throughput and increasing flexibility while cutting costs. The I/O ‘slices’ are separated from the network communication and are mounted on the machine in small pockets of distributed I/O.
Different from block I/O, Distributed Modular I/O is more flexible in the types of data it can collect. While both are setup in a distributed fashion, in block I/O, the individual nodes are dedicated to one specific data type: discrete I/O, valve manifolds, identification data, smart sensor configuration.
Each data type then requires a node or IP address on the network and requires further network and auxiliary power cabling to be installed. A network utilising distributed I/O alone can expose the network cabling to harsh environments and network failures due to damage. Distributed Modular I/O can maintain the industrial network integrity better by keeping the network connections out of the harshest parts of the manufacturing environment.
With centralised I/O or typical remote I/O, there are large volumes of cable runs to manage in a centralised location, usually inside a large enclosure.
Centralised I/O requires many installation and development hours. Since it uses standard connectors and familiar devices, Distributed Modular I/O allows installers to setup and test the I/O hardware quickly. Furthermore, Distributed Modular I/O allows the user to put the exact input/output device precisely where it is needed on the machine, reducing the number of cable runs back to the control cabinet.
8 QUESTIONS TO ASK YOUR CONTROLS SUPPLIER ABOUT DISTRIBUTED MODULAR I/O
When discussing your next Distributed Modular I/O project with potential suppliers, be sure to consider the below factors:
- What variety of I/O devices can you integrate?
- Are these devices IP67?
- What are your company’s plans to support this product line?
- What industrial networks does this solution support?
- Is this a truly distributed and decentralised solution?
- Can the I/O devices be ‘hot swapped’?
- How does your company technically support this product?
- How easily does this solution integrate into my controller?
5 REASONS TO SWITCH TO A DISTRIBUTED MODULAR I/O SOLUTION
A number of important benefits become evident when a Distributed Modular I/O system is implemented into a controls design.
- Simplifies the Controls Quotation Process. The same components for I/O regardless of the PLC brand or industrial network selected. Pricing for controls equipment is standardised from machine to machine.
- Building control cabinets is skilled work and they are time consuming to assemble, wire, and test properly. IP67 Distributed Modular I/O can be mounted on the machine quickly with less labour. Everything is then wired with standard industrial connectors with less time needed for installation.
- Maximizes Spares. Most initial designs include a set of spare I/O points for later development or modifications. With this approach, spare connections can be a flexible placeholder for any type of I/O until the need arises, without adding any controls cabinet space.
- Protects the Network Integrity. Distributed Modular I/O keeps the network cabling out of harm’s way and only the individual I/O device cables run into aggressive environments.
- Reduces Total Cost per Point. The labour involved in parallel wiring a valve manifold or terminating a set of discrete sensors is labour intensive. Analogue devices can get expensive quickly with shielded cable runs and costly four channel analogue input cards, especially when there is only a need for one analogue channel.
- Highly accurate angle detection
- NFPC & Balluff join forces
- Real-time Ethernet interfaces
- Push-pull IO-Link master modules
- Taking a position on measuring systems
- Brose names Balluff Key Supplier
- Cameras with fast interfaces
- Sensor Data – anytime and anywhere
- Balluff goes digital with new app
- Infrared Fluid Detection Sensor
- IMPROVED RESPONSE TIMES
- NO COMPRESSOR TO MAINTAIN
- All-in-one safety solution
- Modular I/O For Real-Time Machine Control
- EtherCAT I/O is Tightly Integrated into Aerotech's A3200 Automation Machine Controller
- Efficient heat dissipation
- Measuring systems with IO-Link
- Slimline I/O system
- Accurately picks up analogue signals
- Narrow IO modules