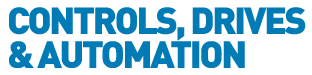
![]() |
Charlotte Stonestreet
Managing Editor |
Digital skills gap grows
04 February 2021
The disruption caused by the global pandemic means that the perennial issue of a shortage of engineers in the UK doesn’t seem to have been at the forefront of anyone’s mind recently.
Indeed, with unemployment rates higher than they have been for many years, looking at a shortfall of staff in any particular area might seem counterintuitive, and indeed insensitive. However, once the situation eventually returns to a more even keel, the challenge of recruiting appropriately-skilled in the industrial sector will not have magically disappeared.
The last several years have seen a concerted effort on the part of bodies, associations, education facilities and even companies to boost the image of engineering and attract young people into STEM careers, and anecdotally this does seem to be having the the desired effect.
As technology develops, this is inevitably influencing the types of engineers needed. Recent research from UK national industrial digitalisation movement, Made Smarter, shows that SME manufacturers increasingly adopting Industry 4.0 and digitalisation are driving up the demand for people with data science and software engineering skills.
Half of the 126 businesses adopting technology with the support of the Made Smarter North West pilot have put data and systems integration at the heart of their productivity and growth plans.
By embracing technologies which connect disparate systems and unify data residing in different sources, companies are spotting trends in production, labour, maintenance and quality issues. They are also able to minimise safety risks, business risk and operational downtime throughout their production.
But while this technology is solving business challenges and driving growth, according to Made Smarter it is also highlighting a digital skills gap across industry and emphasising the need for existing workforces to be upskilled.
Ruth Hailwood, Made Smarter's specialist organisational and workforce development adviser, has worked with many of the 1140 businesses engaged with Made Smarter’s pilot to map the skills they need to introduce new digital tools and technologies.
“The fact that 126 SME manufacturers have committed to investing in new technology projects in the two years since the pilot started, demonstrates the significant appetite for digital tools and solutions,” she said. “And the impact of COVID-19 has only accelerated the desire to speed up digital transformation.
“Data and systems integration projects have emerged as the enabler for businesses to embrace other technologies such as AI, IIOT, Simulation and analytics, taking in more than half of all funded projects
“But what has also become clear is that SME manufacturers lack the key data analytics skills to be able to make best use of what their data is telling them.
“With so many businesses using data and system integration technologies it is vital that companies invest in data science skills and software engineering to capitalise on all the new information. They need in-house skills to champion and drive projects forward.”
Made Smarter is helping to bridge that gap is through a digital technology internship programme which has so far connected 31 university students and graduates with SME manufacturers to work on live digital transformation projects. SME manufacturers benefit from the fresh insight of a digital native to help them adopt technological tools that result in a raft of benefits, including increased revenue growth, reduced production time, and produce the data and insight for new product and market development. Visit www.madesmarter.uk for more information.
- No related articles listed