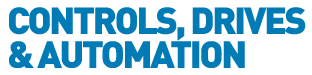
![]() |
Charlotte Stonestreet
Managing Editor |
Home> | AUTOMATION | >Handling & Logistics | >Enables easy mobile robot automisation |
Home> | AUTOMATION | >Robots | >Enables easy mobile robot automisation |
Enables easy mobile robot automisation
22 April 2024
HAILED AS a disruptive technology, the new IDEC Safety Wheel Drive (SWD) allows the user to robotise a rolling machine, such as an AGV or AMR, with only three safety devices: Two SWD wheels and one safety laser scanner. The simplicity of integration spotlights this solution as disruptive technology in the development of such autonomous mobile robots.

Thanks to the simple and uncluttered nature of the mobile robot architecture, designers of robotic solutions gain more freedom to be creative The engineering effort to develop a safety compliant mobile robot is drastically reduced and can cut development costs by a factor of five; additionally the absence of bulky components offers complete freedom for the robot layout and shape.
Safety integrated and reliability requirements
Each SWD wheel is equipped with a certified safety controller that processes information from the robot's safety sensors to prevent unsafe movements. The built-in operational compliance to ISO 3691-4 (driverless truck standard) means safety features within the wheel include STO (Safety Torque Off), SLS (Safe Limited Speed), SMS (Safe Maximum Speed), SBC (Safe Brake Control) and SDI (Safe Direction Control) and direct compatibility with all SIL2/PLd safety laser scanners, such as the IDEC SE2L series. The drives can be easily chained together to provide multi-wheel or multi-axis systems capable of moving several tons. SWD drives feature standard CANopen CiA/DS 402 interfaces for motor control, and safety loops ready to connect to the safety sensors.
Integrator expectations
All the above safety features are pre-configured withing the SWD control and safety routines, which are usually complex and costly to develop, therefore the SWD solution provides much faster and cheaper development time to the user or integrator. Of course, individual adjustments to suit the specific application can be carried out through a number of SWD support and configuration tools. The SWD family are all configurable and provided with full drivers for both ROS and ROS2 (Robot Operating System) instruction sets, giving freedom to the developer.
Scalable technology
The minimum footprint of the series facilitates customised solutions. You can choose from the SWDCore (gear motor), the SWD125 (125mm diameter wheel) or the SWD150 (150mm diameter wheel). Each drive is sealed to IP66 (electronic housing) and available with various gear ratios, ensuring appropriate torque is available to move the required load. Applications for the SWD®Core include pallet shuttles, conveyors, lifts and mobile robots. Whereas the SWD125 and SWD150 can be deployed on applications such as logistic robots, mobile platforms, AGVs and AMRs with maximum speeds from 0.5 to 3 m/s, depending on the transferable load and the gearing used with the SWD)
Get development completed quickly
If you’re looking to get started and develop your proto-type even quicker with then consider the SWD Starter Kit. The Starter Kit is designed to facilitate and accelerate the development of AGVs and AMRs using IDEC’s exclusive SWD Safety Wheel Drive technology. Pre-assembled (out of the box) with a safety laser scanner, an on-board computer and a 24V rechargeable battery, the Starter Kit platform is ready to use – start developing your mobile robot right away! The on-board computer comes with a Linux OS, as well as the open-source ROS middleware and the drivers needed to control the platform in differential mode. The SWD Starter Kit offers all the exclusive safety features of the SWD Safety Wheel Drive range such as SIL2 / PLd certified motion control, ensuring development in accordance with the ISO 3691-4 driverless truck standard.
- Space to innovate
- Strategic nuclear robotics partnership
- Plan to accelerate growth of UK drone industry
- Professor Robert Richardson elected new Chair of ESPRC UK-Robotics & Autonomous Systems Network
- Rail Europe
- In the frame
- AI-driven waste robotics company secures funding
- 'Flying fish' robot
- Improving supply chain management with blockchain
- Beyond the manufacturing plant
- Balls to Gravity
- ROBOTS GIVE FASTER CELL TOOL CHANGE TIMES
- ROBOT FOR DELICATE ASSEMBLY
- FIRST FASTBOX
- NUMBER OF ROBOTS IN UK ON THE RISE
- Tailor Made For Automated Warehouses
- Number of Operators Reduced
- Prevents Potential Material Release
- Integrated or Standalone
- The future is bright - The future is automation!