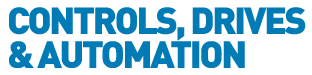
![]() |
Charlotte Stonestreet
Managing Editor |
Home> | INDUSTRY FOCUSES | >Medical & Pharmaceutical | >Prescription for production |
Prescription for production
05 September 2013
Counterfeiting, hygiene standards and the ever increasing need to improve quality, process reliability and manufacturing efficiency are all issues that have to be addressed by the pharmaceuticals manufacturing sector
Although the pharmaceuticals manufacturing sector is characterised by a relatively small number of large, capital-intensive enterprises – think Pfizer, GlaxoSmithKline or Bayer – this does not give the complete picture. In 2010 there were more than 4000 companies operating in the sector in the EU alone, employing over half a million people and generating huge income.
Like any industry, the pharmaceuticals sector has its own particular challenges, both in manufacturing and the wider industry as a whole. For example, the World Health Organization estimates that 10% to 15% of the world’s drug supply is counterfeit. Substances such as cement, talcum powder, sawdust, industrial solvents and paint have been substituted for the active ingredients of dozens of drugs.
It is concern over the proliferation of counterfeit pharmaceuticals that is prompting manufacturers to implement serialised packaging that supports full traceability, product integrity, supply chain security and patient safety.
Conventional serialisation solutions multiplex industrial cameras from an industrial computer (PC) to distribute vision at multiple points on the production line. Maintenance and validation of these systems can be expensive because of the need to deal with a complex operating system and custom software. Another challenge with existing systems is the cost and footprint required to serialise round, un-oriented bottles that frequently require labellers to position many cameras around the bottle in order to read the label.
Körber Medipak's Seidenader subsidiary, a leading supplier of pharmaceutical serialisation solutions, has addressed these challenges by developing a serialisation solution based on the use of smart cameras. Seidenader’s Process Manager line-level serialisation software is designed to configure and manage the Cognex smart camera technology, substantially reducing administration and validation expenses of the vision technology. Just a single industrial computer at the line-level provides the necessary recipe management, security and audit trailing for all camera stations on the packaging line.
2D inspection
Körber Medipak has also addressed the aggregation challenge of inspecting 2D codes on round bottles. With Process Manager 360, bottles can be read on-the-fly, capturing a 360 degree view of an un-oriented bottle. Due to the small footprint of this solution, the inspection station can be integrated anywhere on the packaging line; including the out-feed of a labeller, or in-feed of a bundler or case packer at speeds up to 400 bottles per minute.
The company's original serialisation solutions utilised vision systems consisting of a camera, an image processing card and image processing software running on an industrial PC. Industrial PC-based vision systems require IT department oversight, service pack updates, and other items like virus protection software. In addition, PC technology changes rapidly so that in as little as one year after installation, it can be difficult to source and configure a new PC with the same specifications as those currently used on the line.
The PC based vision system used in the past took considerable time and effort to integrate because they required considerable vision expertise and possibly, knowledge of low-level programming languages. This can be very expensive in today’s regulatory environment because the path to serialisation compliance remains unclear with current data formats and marking standards varying from country to country and region to region. Furthermore, production changes require possible code rewrites to the technology, and costly equipment upgrades to the packaging lines. The overall application software, hardware, and operating system for each vision system always have to be validated to meet FDA requirements, which is an expensive process in itself.
Seidenader worked with Cognex to develop a new serialisation software solution taking advantage of In-Sight smart camera technology. The new line-level software requires only one industrial computer per line to manage the security and recipes for the smart cameras as well as audit trail all tool-set and threshold changes within the software itself. This smart camera based solution provides pharmaceutical manufacturers with a lower cost of ownership because the vision operates independently of the computer operating system, is inherently much more stable over time and is not subject to yearly computer obsolescence issues. This approach makes it easy for the end-users to find "like for like” camera replacements for many years after initial installation, and to maintain consistent vision performance across multiple inspection points and packaging lines.

The new Seidenader serialisation solution also requires much less effort on the part of the customer’s IT department when managing plant wide computer updates and virus protection. The Seidenader serialisation solution is also less expensive to implement because the Process Manager vision interface provides access to the Cognex high level tools that reduce the time and expertise required to develop the vision application and customise the solution to meet specific customer needs.
Process Manager standard verification inspections are designed to parse the data matrix serial number in real-time, automatically populating the human readable toolset and provide verification and match functionality. The vision I/O is managed via the Process Manager industrial computer platform, not a separate vision I/O board.
Hygiene priority
As you would expect from an industry with the size and financial clout of the pharmaceuticals sector, automated manufacturing processes are common throughout. However, unlike the many other areas of the manufacturing sector as a whole, hygiene and the ability to throughly clean all equipment is a top priority. It was partly the easy clean, stainless steel construction of Bürkert’s Element range of diaphragm valves, which resulted in their specification by Unither, a leader in the manufacture of formulations for the pharmaceutical industry, as part of a major modernisation of the company’s plant at Gannat, France. The product's AS-i communication bus facilities and remote visualisation capability were also contributing factors.
The Gannat facility is a specialised production site for the manufacture of soluble tablets, dry formulations and suppositories. Recently, Unither decided to modernise its production equipment at the plant, with the aims of increasing production efficiency, improving safety and meeting the strictest pharmaceutical standards. In addition, Unither also wanted to develop and install an AS-i communication bus, to make its production as flexible as possible.
With all these objectives in mind, the operators of the Gannat site approached Bürkert, specifically because of the company’s know-how and experience of pharmaceutical processes. In addition, Bürkert was the only manufacturer of components and solutions capable of responding to all of Unither's needs in terms of valves and instrumentation, as well as BBS pipework accessories such as viewing windows and filters. This was evidenced by Bürkert’s design and manufacture of special valve blocks for the ELEMENT diaphragm valves, which reduced, as far as possible, the retention volumes where bacteriological growth could occur.
The new installation is equipped with a number of intelligent ELEMENT diaphragm valves. These offer a high degree of modularity with embedded diagnostic tools, guaranteeing maximum reliability and safety. Limit switch devices with AS-i communication are installed on each pneumatic valve.
The installation consists of a tank bottom drain valve type 2105, a draw-off valve type 2014, 2-way manual and automatic valve types 3233 and 2103, as well as the multi-port ELEMENT valve block, type 2034. The tank bottom drain valve is designed for regulation of ultra-pure, sterile, aggressive or abrasive fluids. It guarantees total draining of the tank and offers optimum possibilities for refilling.
Among the advantages offered by this new installation are the stainless steel design of all valve types and the AS-i type 8691 device with high intensity, multi-colour position indicator for visualisation of valve state from a distance – a facility which particularly impressed the operators of the Gannat site.
The ELEMENT range of diaphragm valves has been designed by Bürkert to provide maximum reliability and safety for the most exacting users. The valves offer the advantages of being very easy to use, via simplified adjustment, excellent diagnostics and visualisation, ergonomics, safety of use, adaptability, and ease of electrical and pneumatic connections. In addition, start-up times are reduced by simple automatic regulation of the travel limits (auto-tune function); and reliability is also secured by an integrated filter on the pneumatic supply.
Additional major features include a small valve footprint, and a design where the lifespan of the actuator and control heads is increased through use of a self ventilated system (fresh air design). Also, crucially, the ELEMENT valves are easy to clean and also easy to maintain.
The ELEMENT 2-way diaphragm valves, type 2103; the 'zero deadleg' draw-off valves and the tank bottom drain valves, type 2105, used at Unither, are supplied in nominal diameters from 8 to 150 mm.
The FDA and USP class VI approved membrane they are supplied with is made from EPDM, PTFE/EPDM or advanced PTFE/EPDM. The valves can withstand a pressure of 10 bar and a fluid temperature between -10 and +150° C.
Process Analytical Technologies
Encouraged by regulators, there is considerable interest across the pharmaceutical industry in the adoption of Process Analytical Technologies (PAT) and closed-loop control strategies in order to improve quality, process reliability and manufacturing efficiency. The potential advantages of the approach include shorter cycle times, reduced reject rates and improvements in the way energy and materials are consumed.
Even more significantly, some companies are using PAT to enable the manufacture of pharmaceutical products using high speed, continuous processing techniques, instead of the batch methods currently used by many in the industry.
In one such case, Optimal Industrial Automation has undertaken the design, construction and installation of a complete Process Analytical Technologies based control system to manage a pharmaceutical customer’s continuous manufacturing line, delivering a huge increase in production efficiency and aiding regulatory compliance.
Production-level PAT implementations can require considerable computing power, and Optimal’s latest is no exception. The system runs on no less than six high-powered Dell servers. Three of these control the operation of high speed near-infrared (NIR) spectrometers, which collect data on the condition of the customer’s product in real time during manufacture. These instruments are just part of the system – there being several more on the process.
This data is processed and passed to a separate synTQ server, which compares the results to expectations and makes appropriate adjustment to process parameters to optimise the quality of the product. The final two servers are used for data collection, distribution and reporting, both on site and remotely via a secure web-based interface.
Shop floor interactions with the system are made using three food-grade human machine interfaces (HMIs), which allow production staff to control and monitor the system, and to make manual interventions as required. One of these HMIs, for example, is located in the dispensary of the customer’s facility, where staff will check the condition of raw materials using an automated probe. The synTQ system stores that data and makes use of it to adjust control parameters when that batch of material is introduced into the manufacturing process.
Like all synTQ applications, the new system has been built to be fully compliant with FDA guidelines on the traceability of manufacturing data. Complete records of the measurements taken during production, the configuration of the measurement equipment, the analysis models used and the process control parameters selected are retained within the system for audit purposes, or to facilitate ongoing continuous improvement of the production process.
"The idea is that you design your PAT process and methods within synTQ and then run the configured PAT system in real time when the process is operational. Each and every time you run that process, it uses exactly the same configuration, until you decide that you need to improve it. At which point, all those changes are audited and stored within the system,” explains Paul Gillham, Optimal’s technical lead on the project. "Everything is traceable, and furthermore synTQ’s real time ability to collect multiple spectra and run multiple process models per second makes it stand out as the leading real time PAT data management product.
"Continuous production is an important goal for many pharma companies these days,” concludes Gillham, "As we are both a systems integrator and the developer of the synTQ software, we can provide a unique range of services in projects like these. We can take our customers’ requirements, we can work with the machinery vendor, produce the required PAT hardware and we can provide the software to control the complete system.”
Key Points
- Seidenader has worked with Cognex to develop a new serialisation software solution using of In-Sight smart camera technology
- The design of Bürkert’s ELEMENT diaphragm valves has reduced, as far as possible, the retention volumes where bacteriological growth could occur
- There is considerable interest across the pharmaceutical industry in the adoption of Process Analytical Technologies (PAT) and closed-loop control strategies
- Raspberry Pi 3 goes Wi-Fi
- Aerospace sector set to soar again
- Realtime Robotics extends relationship with Mitsubishi Electric
- Collaboration to integrate 5G into industrial robot
- Virtual Engineering Centre awarded nuclear research contract
- New business models & applications; the potential of Industry 4.0
- ABB & IBM to bolster cybersecurity for industrial operations
- AI set to augment and democratise high-skilled work
- Fast Payback In High Power Applications
- Metso acquires Tedd Engineering
- ROBOT FOR DELICATE ASSEMBLY
- maxon motor Benefits Compounding Pharmaceuticals Market
- The new maxon motor magazine is here.
- Technological remedies
- Medical machine evolution
- Axis Modules DC 061 and DC 062
- Pharmaceutical focus
- Waterproof motor & drive solutions
- Does pharma have productivity cure?
- UK MedTech suffering from market uncertainty