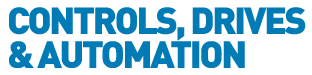
![]() |
Charlotte Stonestreet
Managing Editor |
Hybrid stepper motor actuators
07 August 2019
Recently introduced by Thomson Industries and available with full support from its UK distribution partner Heason Technology, the new MLA series stepper motor driven lead screw actuator features integral anti- rotation guidance and has been designed as a compelling solution for shorter stroke linear positioning tasks.

The rod-style, fully housed MLA series can save the time and cost of design and build for support bearings, lead screws and coupling mechanics, where the torsional force free actuator fulfils all of the componentry required for precision motion.
Typical stepper motor driven positioning mechanics, including stepper actuators, drive a lead screw that translates the motor’s rotary motion into linear motion and force by way of a captive nut. This requires additional support components and an external anti-rotational device for the nut. Whilst some machine designers might choose complete position stages that have these features built-in, or design their own anti-rotational mechanics, space restricted and especially shorter travel linear axes often require custom made mechanics which add unwanted length through bearing blocks and couplings.
As an all-in-one positioning component, the MLA can be easily integrated into such automation tasks, reducing space and minimising the design and assembly requirements. This way Heason Technology’s customers can simply specify load, stroke length and end mounting details for each axis from a comprehensive range of options, then the complete actuator set is delivered and ready for installation.
The MLA design includes an aluminium cover tube with moulded splines in which the nut is locked through integrated low-friction bushings that additionally enable the actuator rod to withstand small radial and moment loads.
The range is available with NEMA type micro-stepping motors, with frame sizes from 8 through 23 in single and double stack power ratings. The range covers maximum stroke lengths of up to approximately 38 mm for the smaller motors and 63.5 mm for the larger motors. Both precision and standard grade lead screws can be ordered with positioning accuracy of 250 microns/300mm and 125 microns/300 mm respectively. Through the range, the maximum linear force, which is speed dependant, is around 100 Newtons for the NEMA 8 frame motor and 600 Newtons for the size 23 (at lower speeds). The MLA series is designed for lower-speed positioning in the range of 25 to 250 mm/sec and best suited to space constrained low-force positioning tasks that require high repeatability. Heason Technology can guide customers through the selection process to optimise the choice and size of actuator for the task.
The MLA series complements Thomson’s MLS and MLN series stepper motor driven leadscrew assemblies that feature rotating screw and rotating nut designs respectively and are equally aimed at space restricted applications with similar force and positioning accuracy characteristics. The choice of three stepper motor driven actuator styles brings flexibility for small scale machine design.
Heason Technology supplies Thomson’s ML series actuators as separate components along with compatible micro-stepping drives and motion controls, or as integrated components as part of the motion specialist’s in-house design-and-build systems integration service. The West Sussex based motion specialist offers complete sales, technical support and service across Thomson’s linear motion and power transmission component range in addition to working with other leading motion control equipment manufacturers to automation and positioning system solutions for challenging applications in a diversity of industries including aerospace, automotive, defence, research, robotics, process control, packaging, motorsports and many more.
- No related articles listed