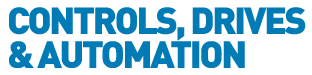
![]() |
Charlotte Stonestreet
Managing Editor |
Home> | CONTROLS | >Motion Controls | >Custom Motion System For CT Scanner |
MORE FROM THIS COMPANY
- Hybrid stepper motor actuators
- Single-cable interconnection
- Frameless brushless motors offer advantages for machine automation
- Motion control improves recycling efficiency
- LOW COST ACTUATORS
- Dynamic performance increase
- Lower installation costs & higher performance
- High-precision gear units
- Gold partner
- Ceramic Technology Advantages
RELATED ARTICLES
- HARMONIC CANCELLATION
- Integrated Motion Control
- New 4th Generation PH Series Servo Planetary Gears are Largest in Class and offer Engineers even more benefits
- Driving Trends & Developments
- EtherCAT I/O is Tightly Integrated into Aerotech's A3200 Automation Machine Controller
- Galvo and Controller Combination Offers Infinite Field of View and 24-Bit Resolution
- Control systems
- Rail Coupling Minimises Downtime
- Full Servo Motion Advantages At A Fraction Of The Cost
- KEB COMBICONTROL C6
OTHER ARTICLES IN THIS SECTION