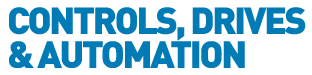
![]() |
Charlotte Stonestreet
Managing Editor |
Editor's Pick
IIoT ready
04 March 2019
Leading producer of integrated servo and stepper motors, JVL Industri Elektronik is announcing the CiA402 Drive profile and syncronisation for EtherCAT.

The JVL EtherCAT module is equipped with two Ethernet connectors and a built-in switch, enabling line, star, tree and ring topology without any extra expensive hardware. The JVL EtherCAT module has several LEDs, enabling technicians and operators to get a quick status overview.
There are also opto-isolated digital I/Os embedded in the module, enabling control of extra sensors etc. without external I/O modules, minimising the number of devices on the net and reduces cable costs.
All connectors are rugged M12 connectors suitable for the rough conditions in industrial environments. Furthermore, all registers in the JVL MAC motor are accessible via the EtherCAT connection, thereby enabling complete control of motor configuration and motion. The JVL EtherCAT module is very easy to use and configure via a predefined setup, and commissioning is easy using the JVL MacTalk application software.
The EtherCAT module with CiA402 drive profile for JVL servo and stepper motors support the synchronised position (CSP) and synchronised velocity (CSV) modes as well as the old modes profile position, profile velocity and many homing methods. The synchronized cycle times for MIS Integrated Stepper can be 1, 2, 3 and 4mS. MAC Integrated Servomotor have 1 and 2mS cycle times. Both have a maximum of ±1µs of jitter.
The JVL EtherCAT equipped motors are plug and play compatible with Beckhoff PLC’s, and also compatible with other manufacturers of EtherCAT masters such as Omron, Lenze, Trio and others.
Using the onboard Ethernet-switch you can daisy-chain cables from one EtherCAT motor to the next, enabling line and ring topology without any extra expensive hardware. On the motor-side, one of the big advantages of using integrated servo motors or stepper motors from JVL, is that you do not need to install a separate servo driver or controller in a control cabinet. This gives you many subsequent advantages: Space savings in your control cabinet, saving of expensive motor and encoder cables, saving time (and money) for cabling, noise is minimized due to internal cabling, and installation errors between driver and motor are eliminated. In addition, service is much easier, since the motor and controller can be replaced as a single integrated unit. Hence, downtime is minimized and production is maximized.
Users can even change Ethernet protocol by updating the firmware using the MacTalk software.
- New JVL UK Sales Manager
- Intelligent motors
- Profinet for JVL Integrated Servo Motors
- Easily setup for Allen-Bradley PLC
- SERCOS for MAC motor & ServoStep
- Next generation stepper motors
- Actual Position Indicated
- Integrated stepper motors
- Versatile Profinet module
- Stepper motor with industrial Ethernet
- No related articles listed