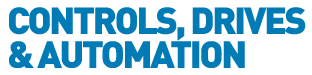
![]() |
Charlotte Stonestreet
Managing Editor |
Home> | AUTOMATION | >Robots | >FREEBIRD - THE THIRD DIMENSION |
FREEBIRD - THE THIRD DIMENSION
24 October 2012
CDA consulting editor, Andy Pye, travelled to Germany via Luxembourg to see Festo last month and found some interesting propulsion experiments going on
Festo’s Bionic Learning Network has been seeking inspiration for new types of system and control concepts, ranging from artificial jellyfish to simulating the motion of birds in flight. "We are constantly seeking out new or relatively unknown motion and drive concepts,” explains Dr Frontzek, head of corporate communication. "Our engineers are working with universities, institutes and development companies in order to transfer mathematical and scientific principles to industrial applications.”
SMARTINVERSION
The most recent project from the Festo Bionic Learning Network was first seen at the 2012 Hanover Trade Fair. The ‘SmartInversion Future Concept’ is not a bird or a plane, but an unusual flying object that propels itself by flipping inside out. Created by engineers at Festo in Esslingen, Germany, the floating band filled with helium takes on different shapes while expanding and contracting to generate thrust and move through the air.
The design is based on the inverted cube shape discovered by the late inventor and mathematician Paul Schatz. Schatz discovered that a third basic type of motion, inversion, was possible in addition to the more familiar rotation (rotary motion) and translation (linear motion). He divided a cube into two star shapes and an invertible cubic belt. The cubic belt is a six-member joint ring, which separates from the two interlocking parts at the corners. It can be continuously inverted and thus take on different shapes.
The flying object itself is made up of six identical prisms filled with helium, held together by a carbon-fibre framework. The combination of lightweight, electric drives and open and closed-loop control makes possible continuous, rhythmicallypulsating inversion in the air.
Three motors drive the motion coordinated by a tiny lithium battery-powered ARM computer processor to power the shapeshifting mechanism. Flight control is done remotely using an iPhone app, so that, by using a smartphone, a person on the ground can guide the object around a room.
Festo still hasn’t come up with a specific use for inversiondriven propulsion. Though one application of sorts is already established as the answer to difficult mixing problems, such as the homogeneous blending of particulate solids – especially those of greatly different specific weight. Unlike most mixing devices, the inversion kinematic is very gentle, so that almost no shear forces are generated. For this reason it is often used in industry to mix explosives. The mixing motion of the Canadian made 88 MIXERS (manufactured by Inversion Machines) is based on the Schatz Inversion Kinematic. One only needs to see one of these mixers in operation to know that you are looking at a truly unusual phenomenon!
APPLICATIONS FOR THIS PRINCIPLE MAY BE FOUND IN THE FACTORY OF THE FUTURE – IN THE FORM OF SELFCONTROLLING, DECENTRALISED, COMPLETE MECHATRONIC SYSTEMS
AQUAJELLIES
What do artificial jellyfish have to do with process automation? Festo’s AquaJellies are artificial, autonomous jellyfish with integral electric drive and an intelligent, adaptive mechanical system. They consist of a translucent hemisphere and eight tentacles which provide forward thrust. A watertight, lasersintered pressure hull is located in the middle of the AquaJelly. This encloses a central electric drive, two rechargeable lithium-ion-polymer batteries of the same size as smartphone batteries, a charging controller and servomotors for the swash plate. Each tentacle is formed as a structure which demonstrates what is known as the Fin Ray Effect.
The Fin Ray Effect is a construction which has been derived from the functional anatomy of the fin. Its peristaltic drive, which is based upon the recoil principle and contracts in a wave-like fashion, is similar to that of its biological model and provides the AquaJelly with the ability to move around.
The swimming replicas, whose natural role models consist of 99% water, function as self-controlled systems in the water with pronounced collective behaviour.
Furthermore, the autonomous jellyfishes are capable of controlling their own supply power by themselves. This is accomplished by means of continuous communication with the charging station. When the artificial jellyfish reaches a charging station which is located above the surface of the water, it is drawn into place by means of suction and supplied with electrical power.
The AquaJelly can use energy saving ZigBee short range radio communication on the surface of the water to exchange status data with the charging station, and to inform other AquaJellies on the surface that the charging station is occupied. In addition to their environmental sensors, which prevent the jellyfishes from colliding with one another, the AquaJellies are also equipped with internal sensor technology which allows for energy status monitoring.
The status of each individual jellyfish can be monitored with the help of an android app. This visualisation of real-time diagnostics allows for, amongst other things, a parameters query regarding the current battery charge level. Each artificial jellyfish decides autonomously which action it will take on the basis of its own status, which depends upon, for example, charge level and drive position, as well as its proximity to other jellyfish.
Applications for this principle may be found, for example, in the factory of the future – in the form of self-controlling, decentralised, complete mechatronic systems, which act autonomously and are networked with each other. And the peristaltic drive used by the jellyfishes with its so-called Fin Ray Effect can just as readily be transferred to actual practice. The DHDG adaptive gripper has already established itself within the market as a serious product. Ultramodern materials, processed by means of laser sintering lamination, have been used to produce AquaJelly’s housing as well.
AND FINALLY....
With the SmartBird, Festo has succeeded in decoding the flight of birds. This bionic technological robotic bird, inspired by a herring gull, can take off, fly and land autonomously without needing an additional drive. Its wings not only flap up and down, they can also adopt specific angles. These movements are driven by an active articulated torsional drive that in combination with a complex control system delivers an unprecedented level of efficiency in flight operation.
The Good Design Award is seen as the Oscar of industrial design. It dates back to 1950 and is now the largest and most important design competition in the world. To win the award, the SmartBird impressed the judges with its unique design. It is an ultralight, yet powerful flight model with outstanding aerodynamics and manoeuvrability.
Key Points
- Festo debuts first pneumatic cobot
- Cantilever electro-mechanical drive
- Festo unveils latest projects from Bionic Learning Network
- PPS becomes Festo Official Partner
- Productivity concepts
- Cost-effective rotary drive
- New Festo.direct online web shop
- New flow control app
- Future perfect form
- Positive evolution: AI in machine control
- Balls to Gravity
- ROBOTS GIVE FASTER CELL TOOL CHANGE TIMES
- ROBOT FOR DELICATE ASSEMBLY
- NUMBER OF ROBOTS IN UK ON THE RISE
- The future is bright - The future is automation!
- High Demand For Grant
- More Capacity, Less Space
- PRECISION ROBOT CELL FOR THE PHARMACEUTICAL INDUSTRY
- ROBOT SALES REACH ALL TIME HIGH
- THE ROBOTICS PACKAGE